Robotic compliant grinding of curved parts based on a designed active force-controlled end-effector with optimized series elastic component
ROBOTICS AND COMPUTER-INTEGRATED MANUFACTURING(2024)
摘要
High-accuracy, fast-response, and low-overshoot force control are important to guarantee the material removal accuracy and surface quality of robotic compliant grinding. In order to achieve the above target, this study develops an active compliant force-controlled end-effector based on a series elastic actuator for the robotic grinding of curved parts. Firstly, a decoupled robotic grinding system composed of an industrial robot and an end-effector is developed, and a novel force-controlled end-effector is designed by adding an elastic component between the servo motor and the load to improve compliance. Secondly, the influences of the elastic component and grinding tool stiffness on the stability of the force-controlled end-effector system are analyzed by establishing a contact model of the compliant end-effector and the transfer function of the entire force control system. Then, the stiffness of the grinding tool and the elastic component are optimized with full consideration of the system cutoff frequency and the end-effector compliance. To improve the force tracking accuracies of the developed compliant end-effector, a proportional-integral (PI) controller with first-order differential force feedforward control is designed. Finally, grinding experiments are conducted for verification. The effects of spring stiffness and grinding tool stiffness on the force control system are tested, which match well with the theoretical analysis. Grinding results show that the maximum force control error of the compliant force-controlled end-effector is decreased by 70% compared to that of the rigid force-controlled end-effector, and the overshoot of the force control is reduced from 30% to almost 0 under the same response speed. The maximum and average absolute grinding depth errors using the designed end-effector are reduced by 57.2% and 58.6%, respectively, compared with those of the traditional rigid end-effector, and the average surface roughness of the finished part is reduced by 19.2%. Which demonstrates the effectiveness and advantages of the proposed compliant force-controlled endeffector.
更多查看译文
关键词
Robotic grinding,Curved parts,Active compliance,End-effector,Force control
AI 理解论文
溯源树
样例
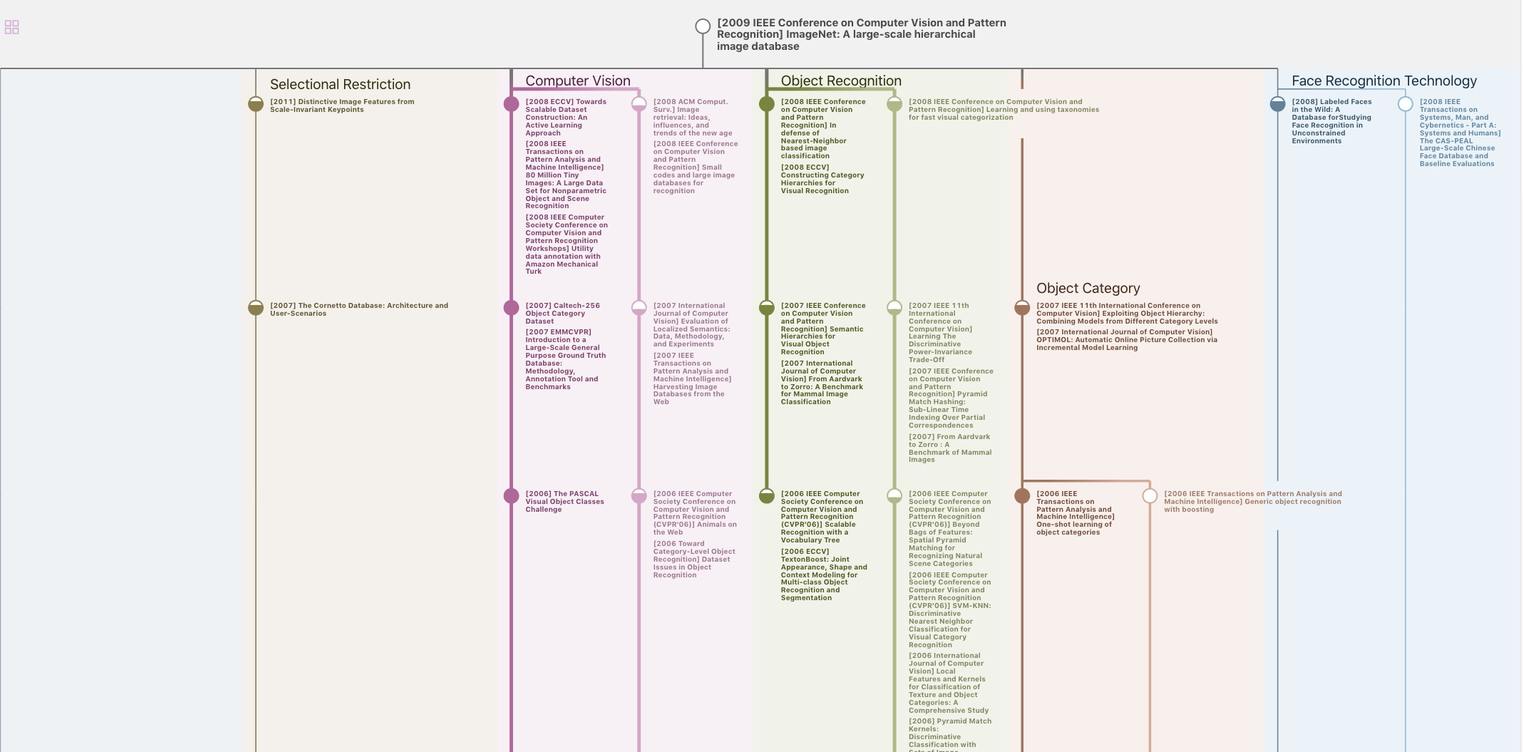
生成溯源树,研究论文发展脉络
Chat Paper
正在生成论文摘要