A General Low-Cost And Flexible Architecture For Robotized Drilling In Aircraft Assembly Lines
2016 INTERNATIONAL SYMPOSIUM ON POWER ELECTRONICS, ELECTRICAL DRIVES, AUTOMATION AND MOTION (SPEEDAM)(2016)
摘要
This paper describes a low-cost and flexible solution to automatize the drilling process in aircraft assembly lines by using anthropomorphic robots. In nowadays aircraft assembly lines, parts to be drilled (e.g., wing upper and lower covers, spars, ribs, fuselage panels, etc.) are either drilled by means of CNC machines or fixtures and jigs. In the latter case, the drilling process is often performed by operators, and the precision constraints are met thanks to reference drilling masks. The devised solution allows to remove the human operator and increase the flexibility of the system. At the same time, it is suitable for existing assembly lines since it requires minimal changes to them and is effective with almost every available manipulators present on the market. To this aim, a well defined procedure that leads a low-cost standard industrial manipulator to meet drilling task requirements is presented. More in detail, a standard arm manipulator carrying a commercial drilling end effector and a force sensor is adopted. The effectiveness of the designed architecture has been tested on a real setup equipped with a Comau SmartSix manipulator in charge of drilling an aluminum fuselage panel.
更多查看译文
关键词
Robotized drilling,Flexible Automation,Force Control
AI 理解论文
溯源树
样例
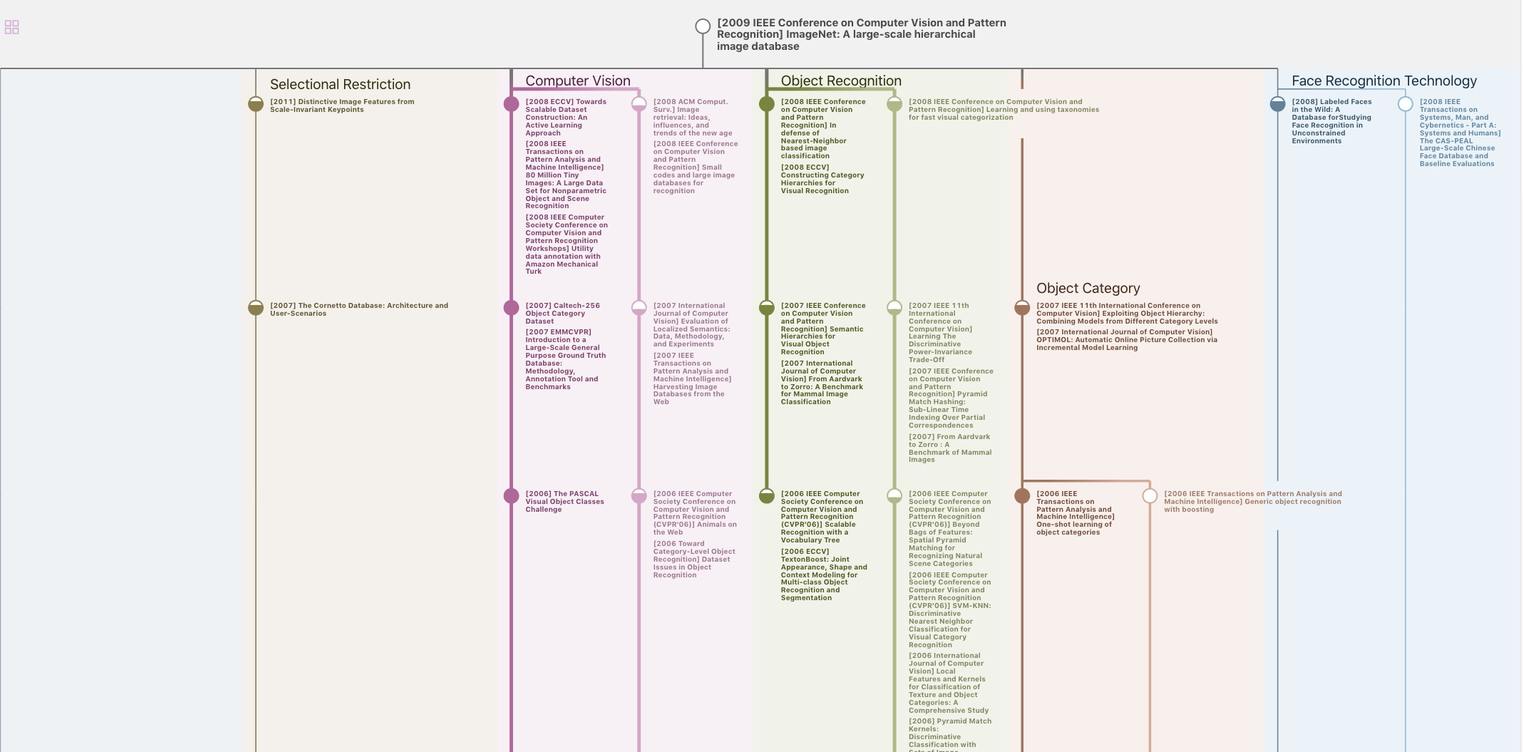
生成溯源树,研究论文发展脉络
Chat Paper
正在生成论文摘要