Comparing the performance of microchannel heat sinks produced by cnc milling versus powder bed fusion
8TH THERMAL AND FLUIDS ENGINEERING CONFERENCE(2023)
摘要
Additively manufactured heat sinks can take advantage of complex, highly optimizable geometries for heat transfer that are not possible to attain using other manufacturing methods. This, combined with a rapid increase in demand for advanced cooling techniques in the field of high-density microelectronics, has driven the development of heat sinks designed specifically for 3D printing. The implementation of mini-/microchannels is a long-established method of increasing the heat transfer coefficient of compact, liquid forced convection heat exchangers, yet there has been little research investigating the viability of integrating microchannels into forced-convection heat sinks produced by powder bed fusion. The relatively low resolution of metal 3D printers begs the question as to whether microchannels manufactured via direct metal laser sintering (DLMS) can still provide a substantial increase in heat transfer at an acceptable penalty in pressure drop. This research compares the forced convection heat transfer and pressure drop performance of aluminum-silicon alloy heat sinks produced by direct metal laser sintering versus CNC milling to establish a baseline for evaluating the effectiveness of microchannels in 3D printed heat sink designs. The results show that aluminum alloy microchannels fabricated by micro-milling have a higher heat transfer coefficient (similar to 60-70%) and lower pressure drop (similar to 10-15%) when compared to microchannels manufactured by DMLS.
更多查看译文
关键词
Microchannel heat sink,Forced convection,Advanced manufacturing,Electronics coolingpierson
AI 理解论文
溯源树
样例
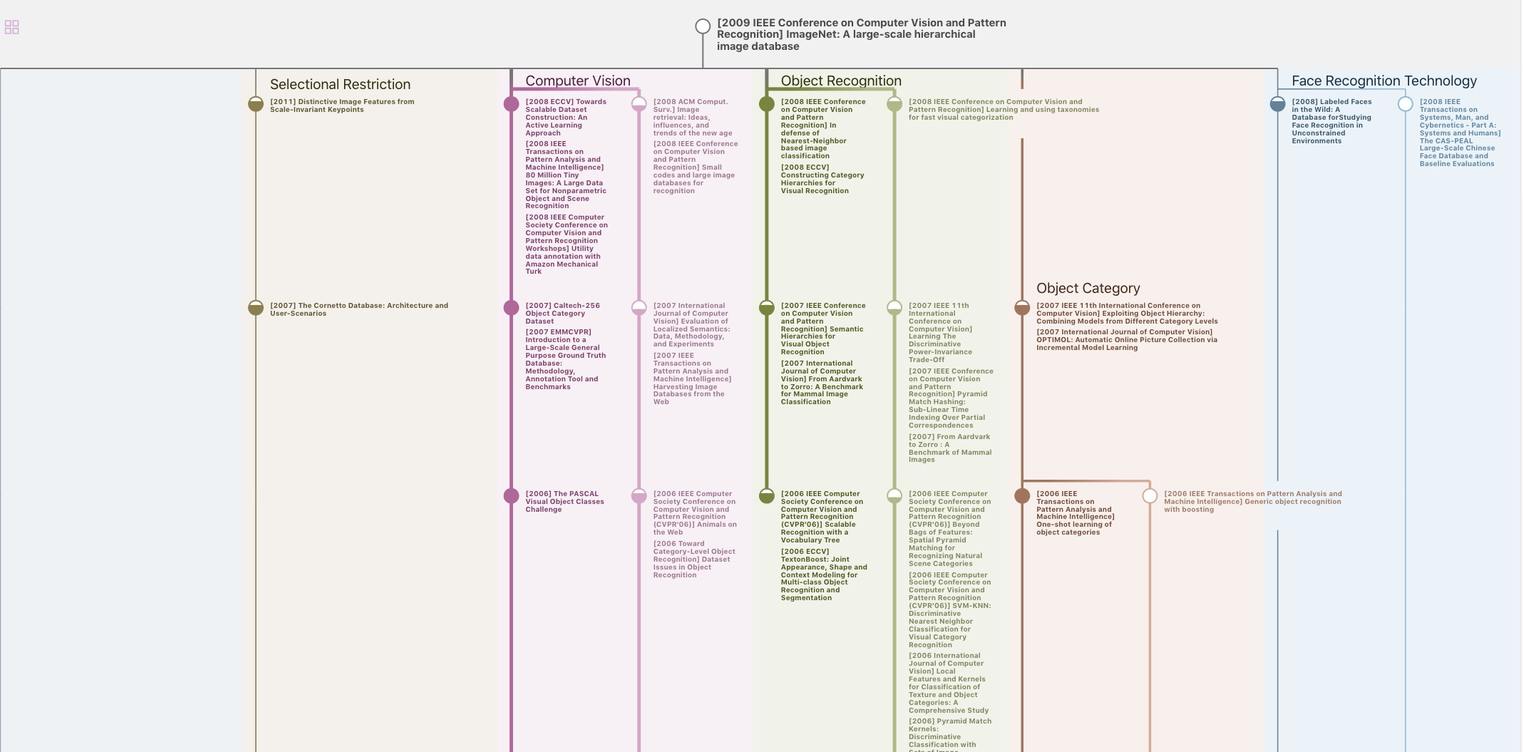
生成溯源树,研究论文发展脉络
Chat Paper
正在生成论文摘要