Computational Thermal-Fluid Dynamics analyses of borated water distribution in the Vacuum Vessel of the Divertor Tokamak Test facility
Fusion Engineering and Design(2024)
摘要
This work presents the full set of 3D Computational Thermal-Fluid Dynamics (CFD) analyses of the Divertor Tokamak Test (DTT) Vacuum Vessel (VV). The VV D-shaped double shell structure, divided into 18 Regular and Special sectors, is actively maintained at the operating temperature of 60 °C by borated water in forced flow to counteract the thermal loads and the heat transfer with the surroundings. Due to manufacturing and integration constraints, the different sectors cannot share the same design: the water will flow in the free space between the two shells composing the VV but, given the complexity of the geometry, a careful hydraulic design is mandatory, to avoid local stagnation points which may cause either overheating or freezing. The different hydraulic paths are separately analysed with the Star-CCM+ software, with a SST k−ω turbulence closure, proving the effectiveness of their design (pressure drop, temperature constraints and stagnation/backflow). In addition, the borated water mass flow rate distribution among the different paths is assessed. To conclude, results from CFD analyses are exploited to approximate the hydraulic characteristic of each sector and to develop a system-level model of the full VV with the Modelica language. The overall VV pressure drop of Δp=2810 Pa, the outlet mixing temperature of Tout,mix=333.06 K and a mass flow rate distribution close to the homogeneous condition (≈2.22 kgs−1 in each sector) confirm that no relevant issues are found in the current VV design from the thermal-hydraulic point of view.
更多查看译文
关键词
DTT,Vacuum vessel,CFD,Thermal-hydraulics,Tokamak
AI 理解论文
溯源树
样例
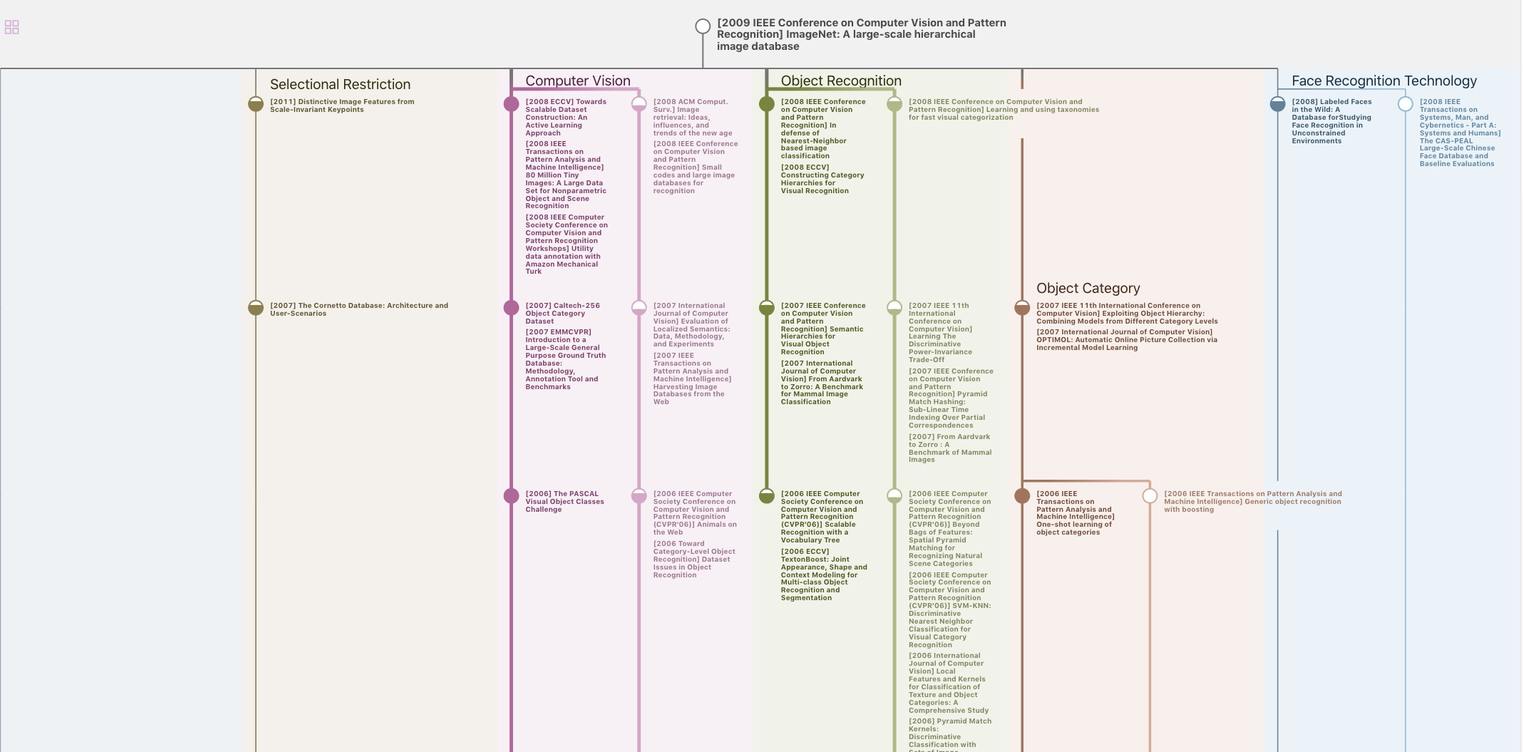
生成溯源树,研究论文发展脉络
Chat Paper
正在生成论文摘要