A novel method for helical gear modeling with an experimental validation
Nonlinear Dynamics(2024)
摘要
Dynamic models are important for developing gear diagnostics methods since they allow physical phenomena occurring during operation to be studied in a relatively simple environment. The main challenge in gear modeling is the calculation of the time-variant gear mesh stiffness, and this challenge is even greater in helical gears. The mechanism of helical gears is more complex than in spur gears; the helix angle both adds an axial component to the contact force and also makes the contact line three-dimensional. This study suggests a novel dynamic model for helical gear vibrations that combines an existing validated dynamic model for spur gears with a unique extension for helical gears. The extension is based on a common method called “multi-slice”, according to which the helical tooth width is divided into infinitesimal slices, and each slice is treated as spur tooth. The suggested model introduces a novel implementation of the multi-slice method that overcomes the aforementioned challenges with only few parameters and calculations, depends on the tooth geometry. Furthermore, for the first time in helical gear modeling, the manufacturing profile errors are integrated to the model to generate scatter in the data that can better reflect the reality. The model is validated experimentally and for two different test-rigs by a qualitative comparison of the RMS of the vibration signal. The simulations and the measured data show similar behavior at different ranges of rotational speed and applied load, emphasizing the potential inherent in the model for future work on gear fault diagnosis.
更多查看译文
关键词
Helical gear model,Gear mesh stiffness,Vibration signature,Model validation,Tooth profile error,Multi-slice method
AI 理解论文
溯源树
样例
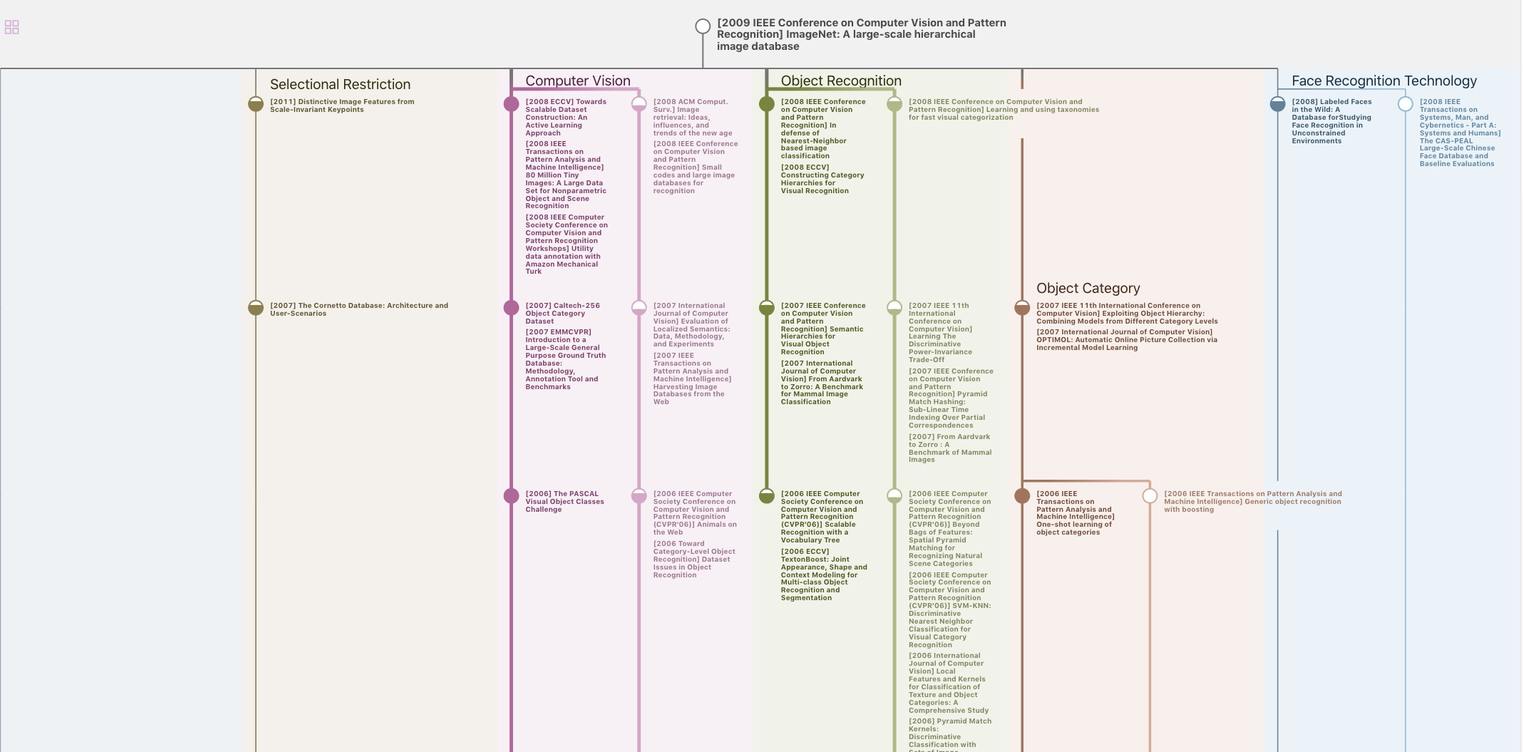
生成溯源树,研究论文发展脉络
Chat Paper
正在生成论文摘要