Surface roughness optimization of hybrid PBF-LB/M-built Inconel 718 using in situ high-speed milling
The International Journal of Advanced Manufacturing Technology(2024)
摘要
We report on the optimization of the surface roughness of hybrid additive manufactured Ni superalloys, combining a conventional laser powder bed fusion process with in situ high-speed milling. This remarkable hybrid approach has only recently been applied to different steel types and barely to Ni superalloys which opposite to steel appear to be challenging for milling processes, particularly within the powderbed of laser powder bed fusion. Different influencing factors on the surface roughness are varied in this study, following the Taguchi method. Their effect is evaluated with respect to the average surface roughness and the maximum surface roughness. The signal-to-noise ratio for the varied parameters infeed, z-pitch, feed rate, and spindle speed is calculated, determining their relevance on the surface roughness, and defining an optimal parameter combination. As the surface quality is optimized to R_a=0.47 μ m , the definition of the optimal parameter combination is of the highest relevance for the application of this novel manufacturing approach for Inconel. Using linear regression, the resulting surface roughness of these parameters is predicted, getting validated by the experimental evaluation. Due to a further analysis, including EDX analysis and a quantitative element analysis at different positions of the flank of the milling cutter, wear characteristics as well as the dissipation of the coating of the milling cutter are detected. The flank wear and the resulting breakage of the cutting edge are defined as the main reasons of a rising surface roughness.
更多查看译文
关键词
Hybrid laser powder bed fusion,Surface roughness,Taguchi method,High-speed milling,Inconel 718,EDX analysis
AI 理解论文
溯源树
样例
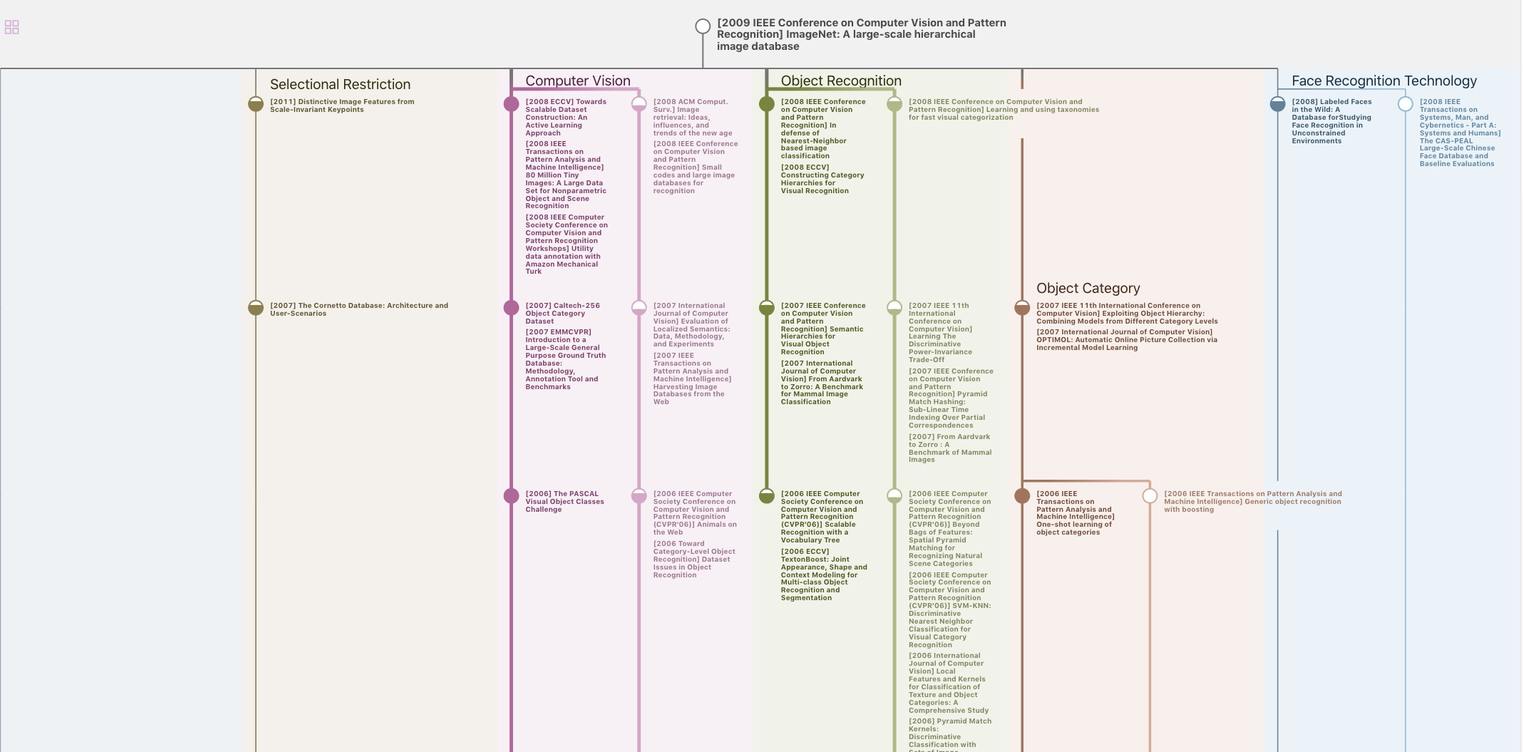
生成溯源树,研究论文发展脉络
Chat Paper
正在生成论文摘要