Talcum powder coated polydimethylsiloxane (PDMS) film flexible large-deformation separation system and stable forming process in bottom-up ceramic vat photopolymerization
Additive Manufacturing(2024)
摘要
In the bottom-up vat photopolymerization process for ceramic materials, the as-built part is generated layer-by-layer from the bottom of the slurry vat. The separation process between the solidified layer and the bottom of the slurry vat introduces significant vertical separation forces due to various resistance forces. Particularly in fabricating large cross-section parts, larger separation forces are more prone to induce crack propagation or detachment of the as-built part from the substrate, resulting in printing failures. This study introduces a novel approach involving the application of a talcum powder-coated polydimethylsiloxane (PDMS) film to address this issue, aiming to reduce the adhesion between the PDMS film and the bottom of the slurry vat. The developed system exhibits flexible separation capabilities during the build platform's lifting process. Compared to traditional unmodified PDMS film separation systems, the modified system demonstrates an average reduction of 93% in the maximum separation force. Notably, as the cross-sectional area of the printing increases, the magnitude of the increase in maximum separation force of the modified system compared to the unmodified system drops significantly. This characteristic facilitates the successful printing of larger-sized parts. The talcum powder-coated PDMS separation system proves effective in successfully printing aviation ceramic cores, triply periodic minimal surface (TPMS) models, teeth model with a cross-sectional size of 85 mm × 65 mm in solid geometry and a bone model exceeding 150 mm in height.
更多查看译文
关键词
Vat photopolymerization,Ceramic,Multiscale complex structure,Talcum powder,Separation force
AI 理解论文
溯源树
样例
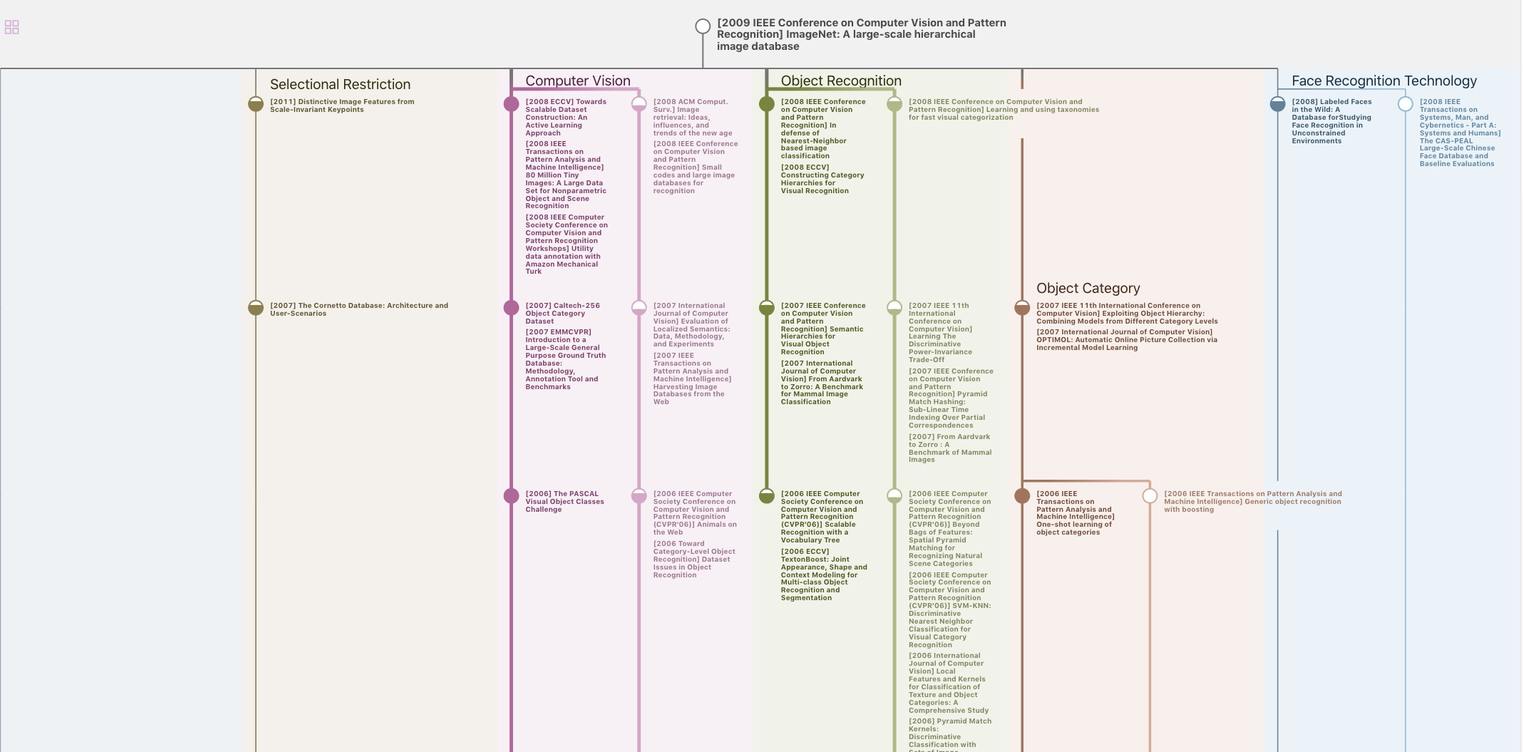
生成溯源树,研究论文发展脉络
Chat Paper
正在生成论文摘要