Experimental and numerical study on the dynamic and lubrication characteristics of the rotor-bearing-frame system in a variable-speed scroll compressor
PROCEEDINGS OF THE INSTITUTION OF MECHANICAL ENGINEERS PART E-JOURNAL OF PROCESS MECHANICAL ENGINEERING(2024)
摘要
The variable-speed scroll compressors can adapt to the various demands of heating and cooling capacity, and the rotational speeds significantly influence the rotor dynamic and bearings lubrication, which might cause performance and reliability issues. In this paper, numerical models for the rotor-bearing-frame system are developed by coupling the Reynolds equation, rotor dynamic equation, and the flexibility equation of the frame. The experimental apparatus is also established to directly measure the journal displacement response in the hermetic high-pressure shell of the compressor. The predicted journal center trajectories are compared with the experimental results and they show good agreement. Results show that the whirl radius decreases with the increase of rotational speed at the measuring point, while the opposite tendency can be observed at the bottom of the main bearing. Transient dynamic analysis of the rotor shows that the tilting and deformation of the rotor vary with respect to different rotational speeds. The displacement of the crank part could lead to the separating tendency between orbiting and fixed scrolls through the coupled orbiting bearing, especially at the lower rotational speed, due to the pull of main balance weight. The numerical results also reveal that the distribution of oil film pressure is dominated by the squeeze effect due to the relatively stable magnitude but the variable direction of loads on the shaft. The influence of the deformation of the cantilevered bearing frame on the oil film thickness is significant but the maximum deformation moves downward at the higher rotational speed.
更多查看译文
关键词
Scroll compressor,dynamic,lubrication,experiment,simulation
AI 理解论文
溯源树
样例
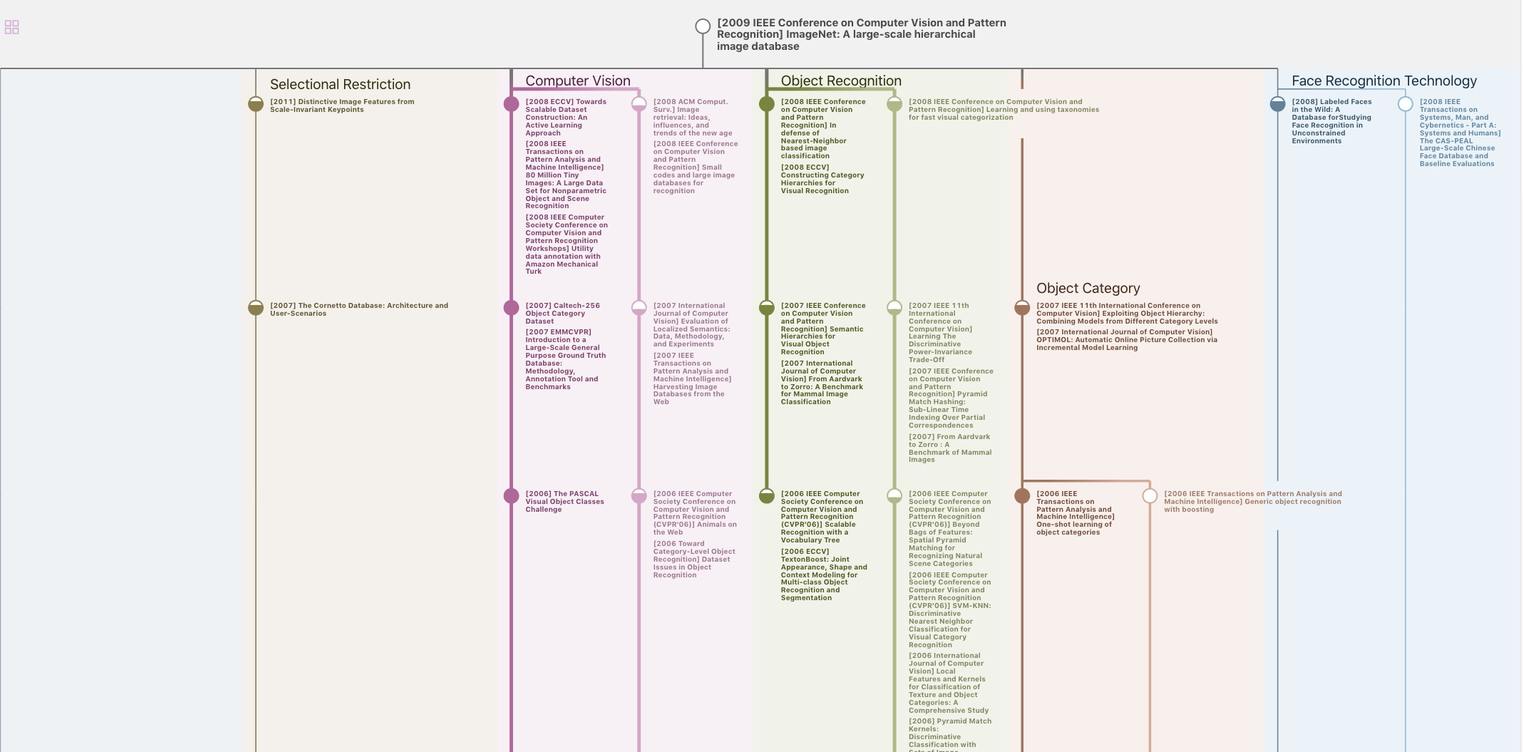
生成溯源树,研究论文发展脉络
Chat Paper
正在生成论文摘要