Influence of blowing ratio and geometric parameters on cooling performance and thermal stress of a double wall structure
THERMAL SCIENCE AND ENGINEERING PROGRESS(2024)
摘要
To improve the turbine inlet temperature of aero engines and optimize gas turbine efficiency, the development of more efficient cooling techniques is critical. However, these techniques produce substantial temperature gradients, which cause the continual increase of thermal stresses. Correspondingly, this exacerbates thermomechanical performance issues. Therefore, this study investigates how aerodynamic and geometric parameters, including blowing ratio, impingement distance and pin-fin diameter, affect the temperature and thermal stress distribution in the double wall structure. Our investigation has shown that there is a significant temperature gradient in both the film plate and pin-fin. The internal surface of the film plate demonstrates noteworthy thermal stresses, especially on the film holes' leading edge and pin-fins' upper edge. Increasing the blowing ratio from 0.5 to 2.0 increases the cooling efficiency. The maximum stress occurs at a ratio of 1.0. Extending the impingement distance from 1 to 3 results in reduced cooling efficiency and higher thermal stress. Increasing the pin-fin diameter from 0.75 to 1.25 produces greater cooling efficiency and lower thermal stress. Thermal stresses are less affected by impingement distance and pin-fin diameter with higher blowing ratios. These findings aid in preliminary design considerations and serve as a basis for assessing life in double-wall structures.
更多查看译文
关键词
Fluid -thermal -solid coupling,Double wall,Overall cooling efficiency,Thermal stress
AI 理解论文
溯源树
样例
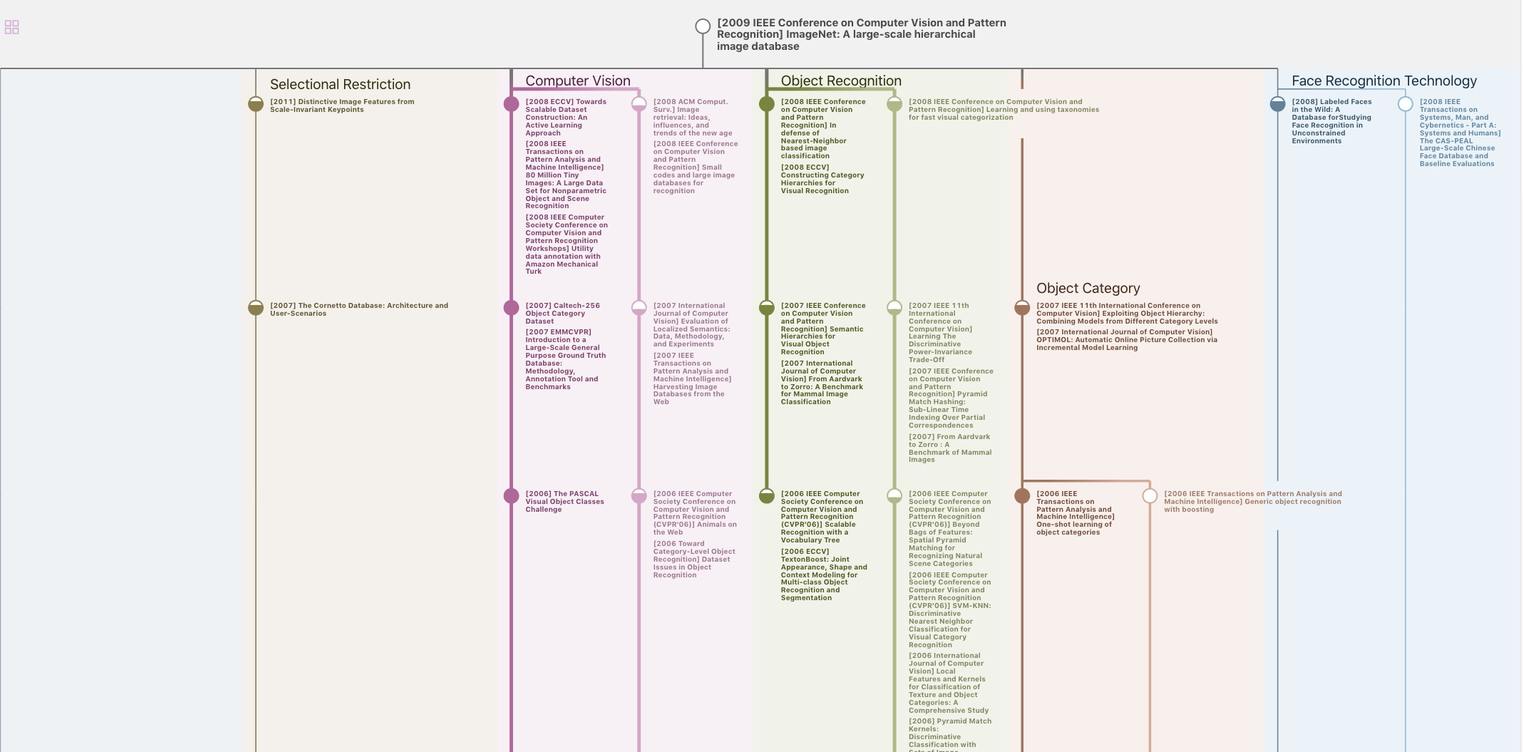
生成溯源树,研究论文发展脉络
Chat Paper
正在生成论文摘要