Data-driven fatigue life prediction of small-deep holes in a nickel-based superalloy after a cold expansion process
INTERNATIONAL JOURNAL OF FATIGUE(2024)
摘要
Cold expansion process (CEP) is an effective anti-fatigue manufacturing technology, which is widely used in the hole strengthening of aviation components. In this study, the multi-convex hulls rotary cold expansion process (MCR-CEP) is applied to improve the fatigue life of hole structures. In order to verify the robustness and effectiveness of MCR-CEP on fatigue life improvement, a series of fatigue tests are conducted for the hole specimens with different hole diameters from 1 to 3 mm under different loading conditions of temperatures from 300 to 700 celcius and maximum stress from 650 to 1100 MPa. Results show that the fatigue life of hole specimens is improved by MCR-CEP at lower temperatures and loading stresses. Subsequently, a data-driven procedure with the combination of finite element method (FEM) and machine learning (ML) models is constructed for predicting the fatigue life of hole specimens. Compared with the experimental results, the data-driven life prediction method based on the random forest regression (RFR) model performs the highest prediction accuracy, and all the data points are located within +/- 2.5 error band. Finally, the feature importance and uncertainty analysis are carried out with the help of the ML-based models. The tested temperature and maximum loading stress are the dominant features of the fatigue life for the hole specimens. More importantly, adequate experimental data and high machining accuracy are essential conditions for the reliability of aviation components.
更多查看译文
关键词
Cold expansion,Fatigue life prediction,Machine learning,Finite element method
AI 理解论文
溯源树
样例
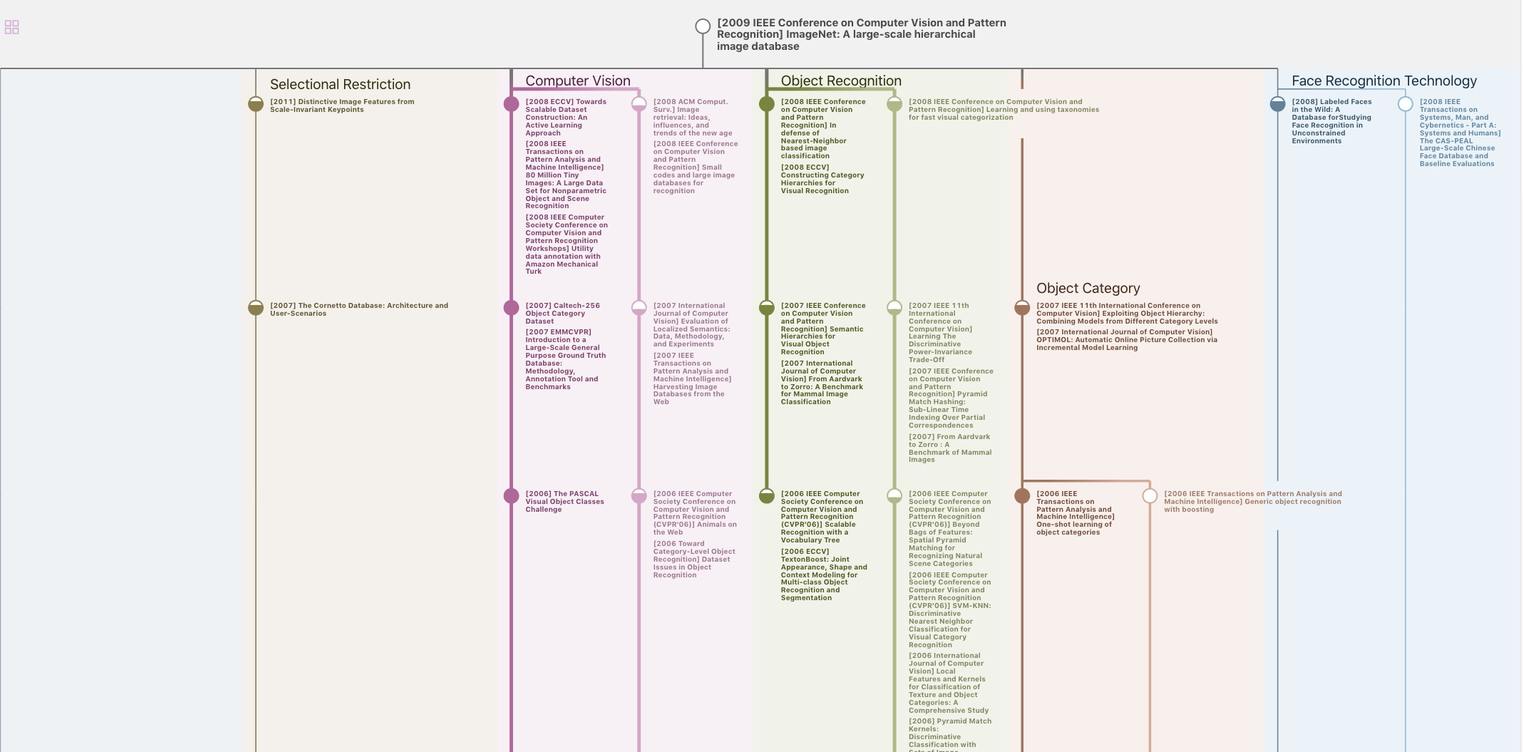
生成溯源树,研究论文发展脉络
Chat Paper
正在生成论文摘要