Volume compensation of large-deformation 3D-printed soft elastomeric elastocaloric regenerators
APPLIED PHYSICS LETTERS(2023)
摘要
Elastomeric elastocaloric regenerators have great potential for use in low-stress elastocaloric cooling devices. However, these regenerators display an asymmetric fluid exchange when operating in an active elastocaloric cooling cycle, due to the large required strains and associated volume change. During strain, the fluid volume increases, which passively forces fluid flow into the regenerator; when the strain is released, the fluid volume decreases, which results in a fluid flow out of the regenerator. During a traditional elastocaloric cooling cycle, there are also active fluid flow periods provided by fluid displacers or pumps. Here, we study the passive fluid flow in high-strain regenerators using a numerical model and experiments in two types of regenerators. Hyperelastic models are used to fit the experimentally measured mechanical behavior of thermoplastic polyurethane elastocaloric elastomers, and the model is subsequently used to conduct finite-element simulations predicting regenerator volume changes for an applied strain of 200%-600%. We validated the results using a specifically designed setup for measuring volume changes using pressure differences on a parallel-plate regenerator. For a strain range of 200%-600%, the predicted volume change ratio is 69.5%, closely matching the experimental value of 66.7%. We observed that the middle region of the regenerator experiences a higher volume change, which can be accurately accounted by the numerical model.
更多查看译文
AI 理解论文
溯源树
样例
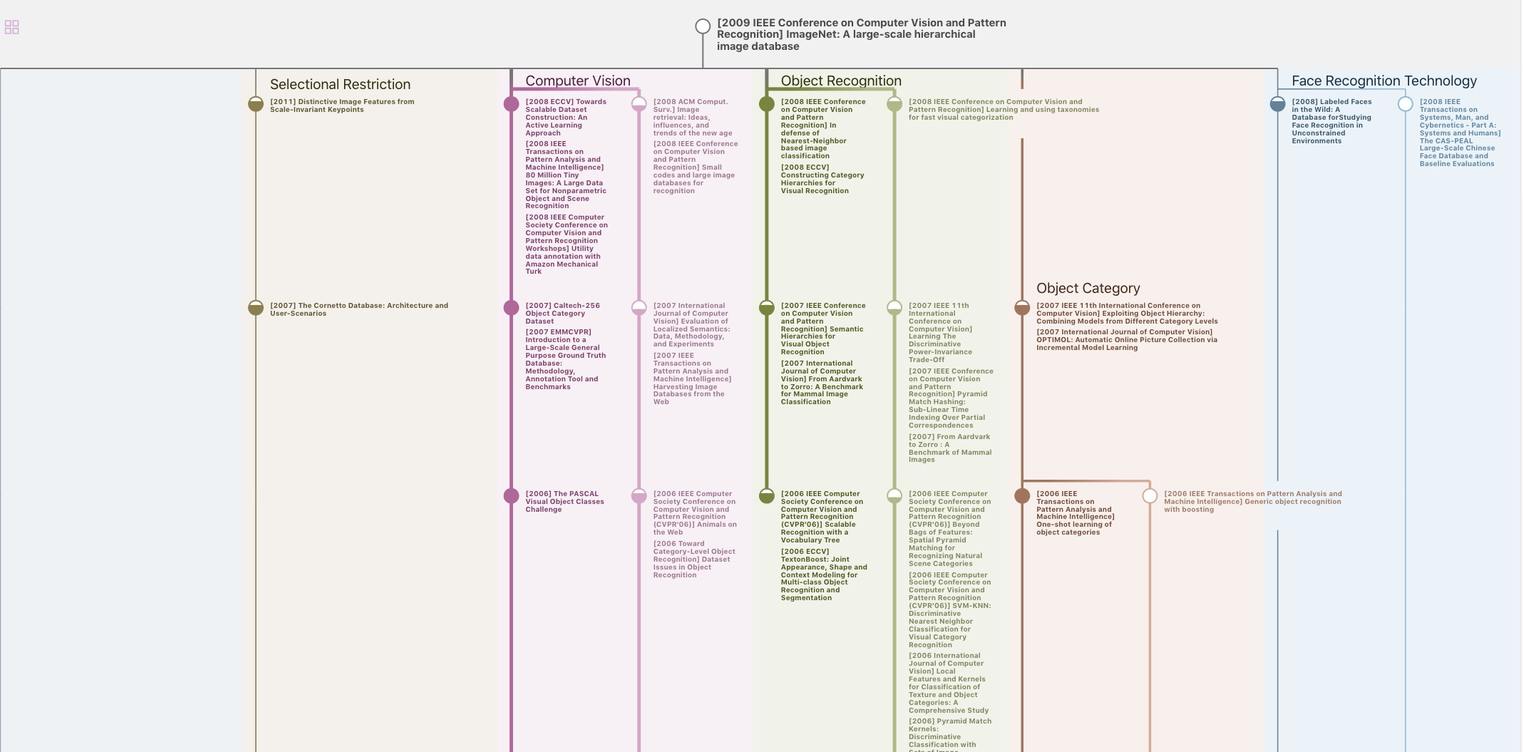
生成溯源树,研究论文发展脉络
Chat Paper
正在生成论文摘要