Integrated vehicle chassis fabricated by wire and arc additive manufacturing: structure generation, printing radian optimisation, and performance prediction
VIRTUAL AND PHYSICAL PROTOTYPING(2024)
摘要
In the automotive industry, the extended design and iteration cycles for integrated chassis typically span 2-3 years, creating a misalignment with swiftly changing market demands. Wire arc additive manufacturing (WAAM) technology presents a viable alternative, overcoming the limitations of conventional chassis production. Our holistic framework significantly condenses the design, optimisation, and validation stages for automotive chassis. Initially, a ground structure method is utilised to outline and generate a skeleton chassis. We then utilise the OpenCV image processing method to select a hollow skeleton chassis with minimal material occupancy (0.476) and suspension printing. Subsequently, we assess the influence of printing radian variations by the robotic arm on the microstructure and stress, employing a cellular automaton-finite element (CA-FE) model at the 150th and 200th layer benchmarks. A Kalman filter (KF) is also implemented to fine-tune the printing radian in regions with coarse grain structures and elevated solute concentrations. The process concludes with collision and modal simulation verifications of the skeleton chassis, affirming the optimisation's success. This streamlined methodology allows the completion of the chassis design and manufacturing cycle within a remarkably condensed time frame of one week, accelerating the development process by a factor of 120.
更多查看译文
关键词
WAAM,FEM,cellular automata,topology,Kalman filtering
AI 理解论文
溯源树
样例
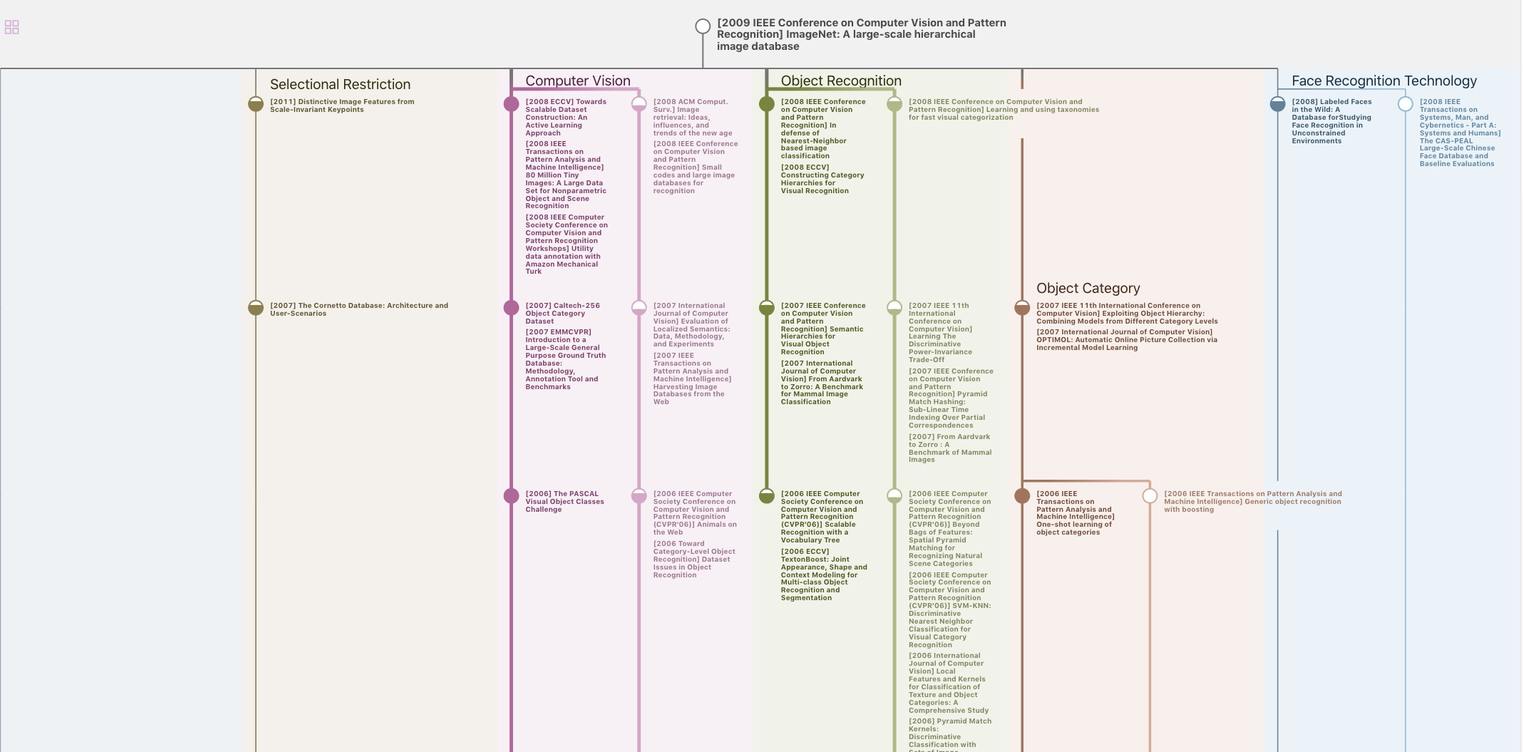
生成溯源树,研究论文发展脉络
Chat Paper
正在生成论文摘要