Specimen Design, Heating Rate, and Temperature Gradients during Heating in an Induction Heated Dilatometer
Journal of Materials Engineering and Performance(2024)
摘要
Solid and hollow cylindrical specimens of ferrite–pearlite and austenitic stainless steel were induction heated at heating rates up to 600 °C·s −1 using a high precision DIL 805L dilatometer. High heating rates were attained for the magnetic state at temperatures below the curie ( A c2 ) temperature and reduced heating rates were observed for the non-magnetic austenite at temperatures above the A c2 . Heating the commonly used 4 mm diameter by 10 mm long specimens at rates above 50 °C·s −1 resulted in non-linear heating rates during transformation to austenite and large transient temperature variations along the specimen length. These limitations in heating rate and variances from ideal uniform heating lead to inaccurate measurement of the A c1 temperature. Induction heating modeling showed that the specimen ends heated more slowly (colder ends) than the center for the magnetic ferrite structure and more rapidly (hotter ends) for the non-magnetic austenite structure. Changing the specimen design to a thin wall tube allowed faster heating rates and modified the pattern of temperature variations within the test sample. The response of selected specimen geometries to induction heating in the dilatometer was characterized by modeling and tests using multiple thermocouples to verify the models. The results demonstrated that the use of properly designed tubular test specimens can aid in more accurately determining the A c1 transformation characteristics during heating at ultra-fast induction heating rates.
更多查看译文
关键词
heat treatment,induction heating,modeling and simulation,rapid transformations,stainless,steel
AI 理解论文
溯源树
样例
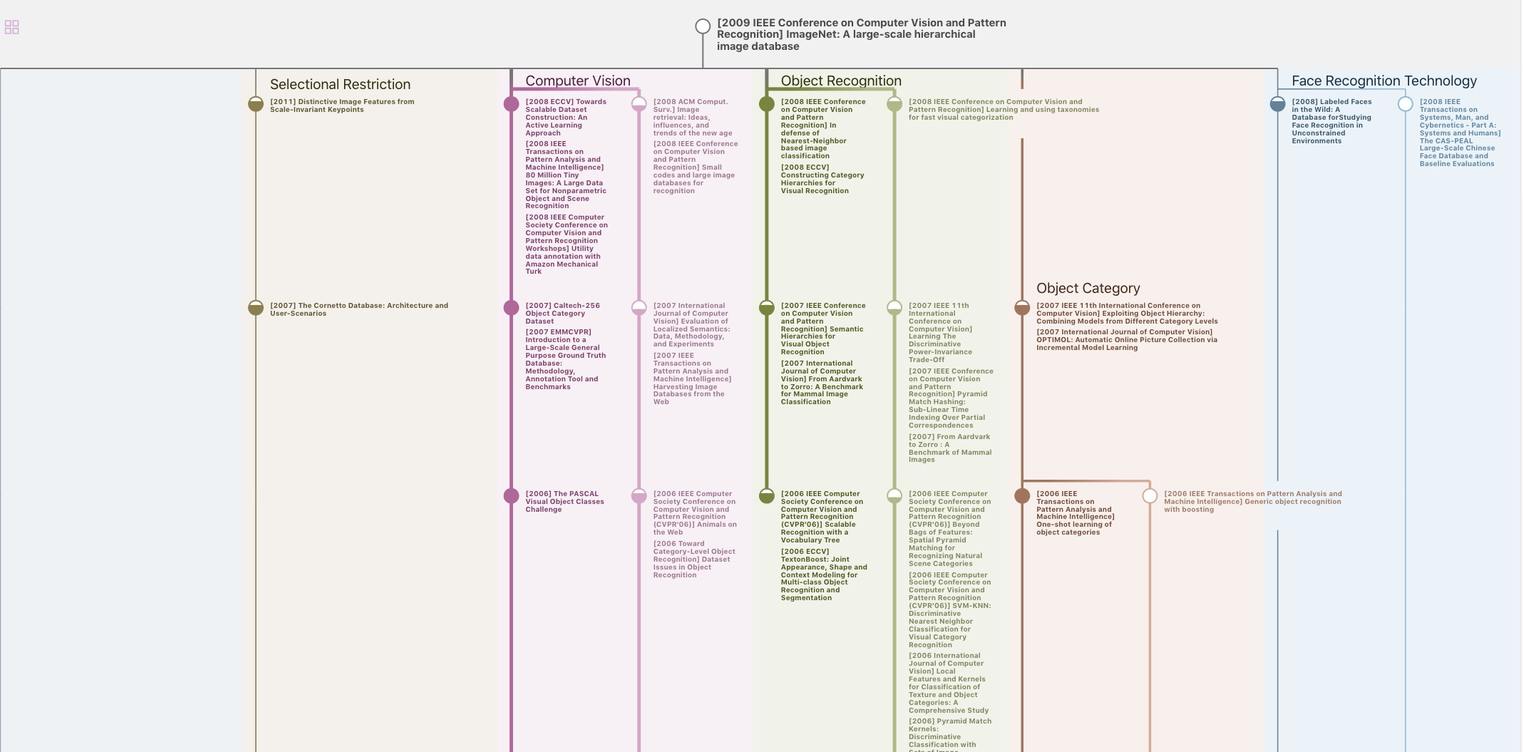
生成溯源树,研究论文发展脉络
Chat Paper
正在生成论文摘要