Direct Winding Thermal Management Schemes Enabled by Additive Manufacturing
2023 IEEE Energy Conversion Congress and Exposition (ECCE)(2023)
摘要
The electrification and hybridisation of ground- and air- transport, in pursuit of Carbon Net Zero, is driving demand for high power-density electrical machines. Power-density and reliability is ultimately limited by the ability to dissipate internally generated losses while respecting the temperature constraints of the electrical insulation system. As the electrical windings are often the dominant source of loss, their enhanced design is in the critical path to improved power-density. Application of metal additive manufacturing is disrupting conventional winding design by removing restrictions on conductor profiles, topologies, electrical insulation materials and thermal management. In particular, the adoption of extended surfaces, integrated heat exchangers or through-conductor cooling channels offer routes to substantial increases in electrical loading. This paper presents a through-conductor fluid cooling scheme which aims to minimise the volume occupied by cooling structures in the active length by strategically placing the fluid channels to provide targetted thermal management. All whilst eliminating the active length temperature gradient seen in the previously reported end-winding heat exchanger scheme. A prototype winding is manufactured and experimentally evaluated, demonstrating the performance improvement potential of direct thermal management.
更多查看译文
关键词
Additive Manufacturing,Thermal Management,High Power-Density,Liquid Cooling,Winding Design
AI 理解论文
溯源树
样例
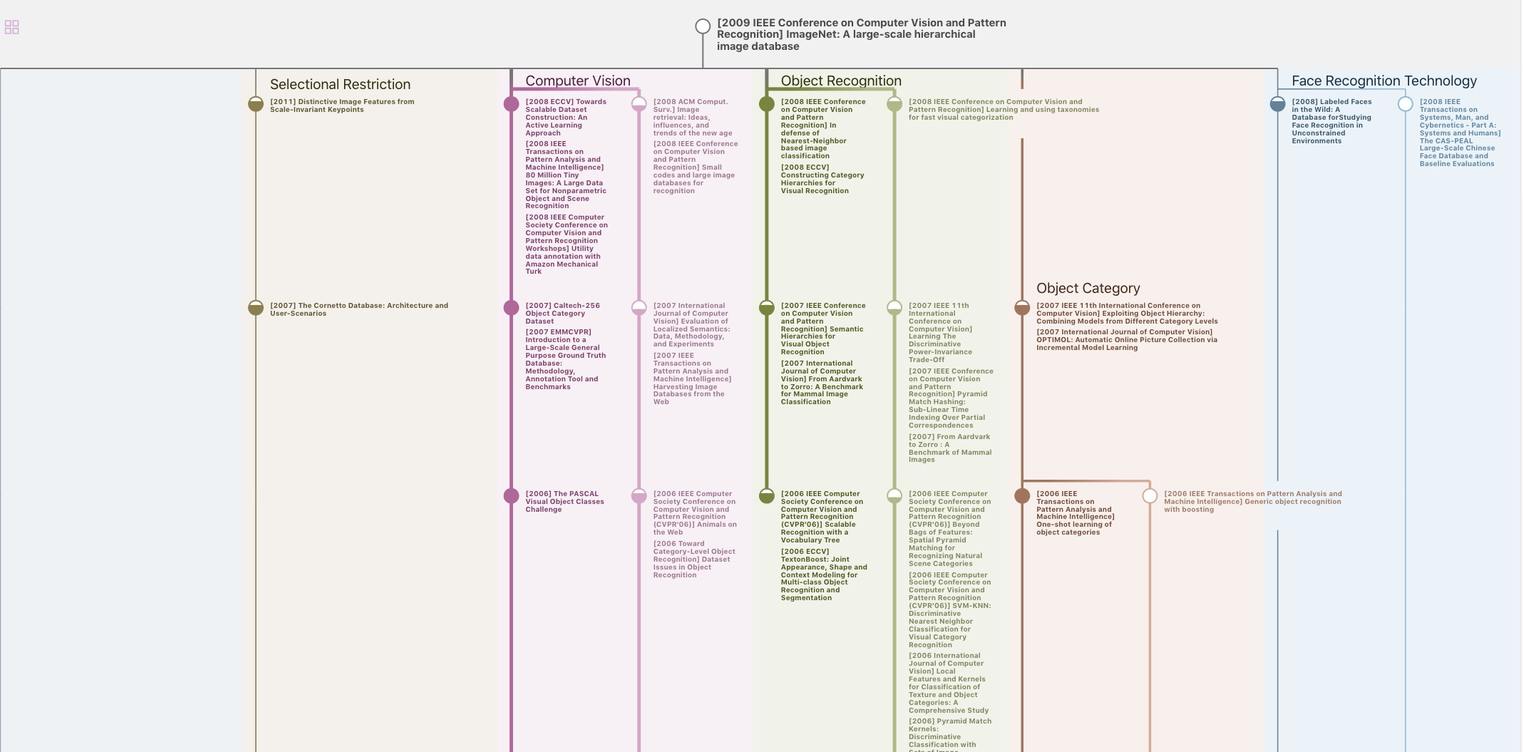
生成溯源树,研究论文发展脉络
Chat Paper
正在生成论文摘要