Research on robot regrinding trajectory planning and surface characteristics of damaged blades
The International Journal of Advanced Manufacturing Technology(2023)
摘要
Aeroengine blades are the power components most relevant to the energy conversion process. Due to the harsh working environment, the blades are seriously damaged after service, which affects their dynamic performance. The regrinding of damaged blades can extend their service life. However, the machining flexibility of the traditional grinding machine tool is insufficient to meet the needs of damaged blade repair, and the regrinding track of the blade cannot be directly generated by its theoretical geometric model. In order to solve the above problems, a robot regrinding scheme and trajectory planning method for damaged blades has been put forward. Based on the morphology measurement results of damaged blades, the point cloud reconstruction and regrinding trajectory research were carried out. The precision regrinding of damaged blades was realized. The comparison results of damaged blade morphology before and after regrinding indicate that the surface quality of the blade was improved significantly after regrinding. There are no obvious scratches, deep grooves, and large area adhesion on the repaired surface. The fractal dimension of the surface after regrinding is increased in different directions, which indicates that the surface structure characteristics after grinding are more fine. The average surface roughness of blades after robot regrinding is reduced from 2.67 to 1.59 μm. The profile error after robot regrinding is reduced from 0.35 to 0.16 mm. The research results provide a reference for the repair and manufacturing of blades.
更多查看译文
关键词
Aeroengine blade,Superalloy,Robot regrinding,Trajectory planning,Surface topography
AI 理解论文
溯源树
样例
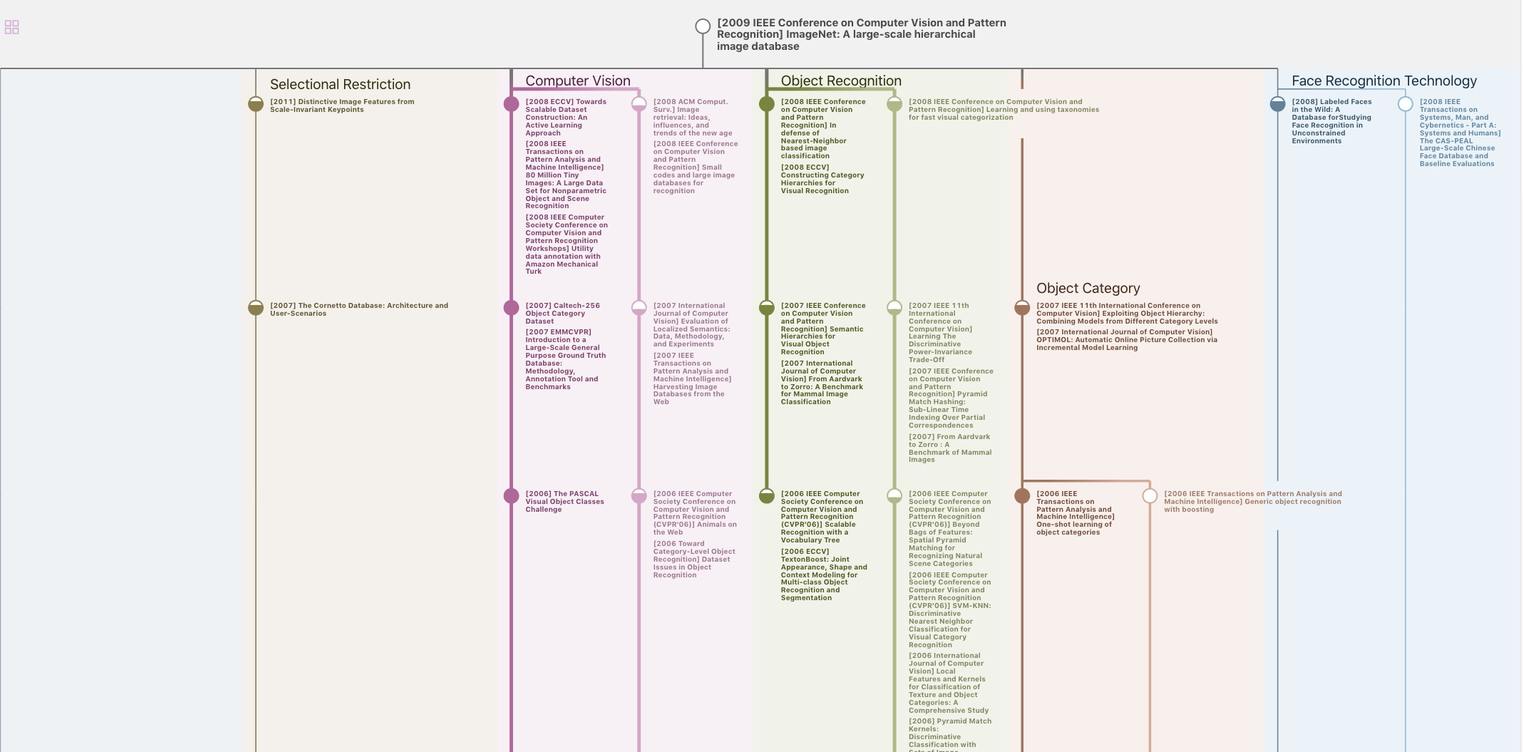
生成溯源树,研究论文发展脉络
Chat Paper
正在生成论文摘要