Wear of Carbide Plates with Diamond-like and Micro-Nano Polycrystalline Diamond Coatings during Interrupted Cutting of Composite Alloy Al/SiC
Journal of Manufacturing and Materials Processing(2023)
摘要
The complexity of milling metal matrix composite alloys based on aluminum like Al/SiC is due to their low melting point and high abrasive ability, which causes increased wear of carbide tools. One of the effective ways to improve its reliability and service life is to modify the surface by plasma chemical deposition of carbon-based multilayer functional layers from vapor (CVD) with high hardness and thermal conductivity: diamond-like (DLC) or polycrystalline diamond (PCD) coatings. Experiments on an indexable mill with CoroMill 200 inserts have shown that initial tool life increases up to 100% for cases with DLC and up to 300% for multilayered MCD/NCD films at a cutting speed of 800 m/min. The primary mechanism of wear of a carbide tool in this cutting mode was soft abrasion, when wear on both the rake and flank surfaces occurred due to the extrusion of cobalt binder between tungsten carbide grains, followed by their loss. Analysis of the wear pattern of plates with DLC and MCD/NCD coatings showed that abrasive wear begins to prevail against the background of soft abrasion. Adhesive wear is also present to a lesser extent, but there is no chipping of the base material from the cutting edge.
更多查看译文
关键词
Al/SiC composite alloy,milling,tungsten carbide,diamond-like coating,micro-nanocrystalline multilayered diamond coating,wear
AI 理解论文
溯源树
样例
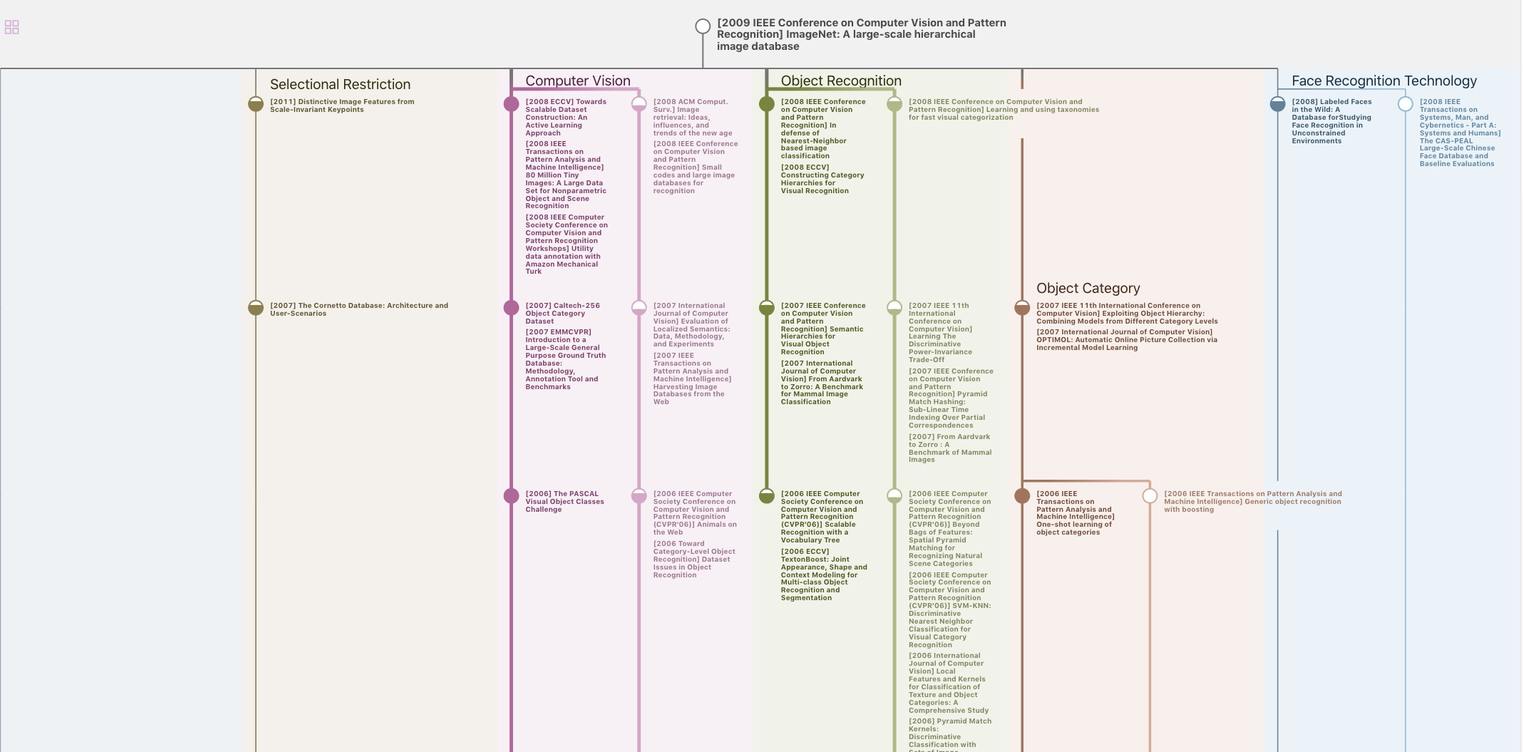
生成溯源树,研究论文发展脉络
Chat Paper
正在生成论文摘要