3D numerical simulation and experimental validation of resin-bonded sand gravity casting: Filling, cooling, and solidification with SPH and ProCAST approaches
THERMAL SCIENCE AND ENGINEERING PROGRESS(2024)
摘要
This article provides a comprehensive investigation into the resin-bonded sand gravity casting process, with a focus on the filling, cooling, and solidification steps. The research combines numerical simulations and experimental validation in a three-dimensional (3D) configuration, utilizing a realistic filling system. The study employs three approaches-experimental tests, Smoothed Particle Hydrodynamics (SPH) simulations, and ProCAST simulations-to analyze the filling, cooling, and solidification steps. Two different molds were used in the experiments. The first mold has a transparent glass component in front of the plate, enabling observation and recording of the filling process, while the second mold, used solely for thermal analysis, did not incorporate any glass component. The SPH approach yields more accurate results for the filling time, liquid level height, and morphology when compared to ProCAST. The discrepancy in final filling time for the desired casting part between the experiment and SPH is 5.13 %, and the difference between the experiment and ProCAST is 15.38 %. Additionally, the cooling and solidification steps are investigated through an analysis of cooling curves. The numerical methods demonstrate slightly higher cooling rates and deviations in solidification times compared to the experimental data, mainly due to the thermal Neumann boundary condition. Furthermore, the average discrepancy in solidification time for five points of the intended casting component between the experiment and SPH is 8.60 %, whereas when compared with ProCAST, the discrepancy increases to 9.13 %.
更多查看译文
关键词
Gravity casting,SPH,Filling time and morphology,Solidification time,3D Printing mold
AI 理解论文
溯源树
样例
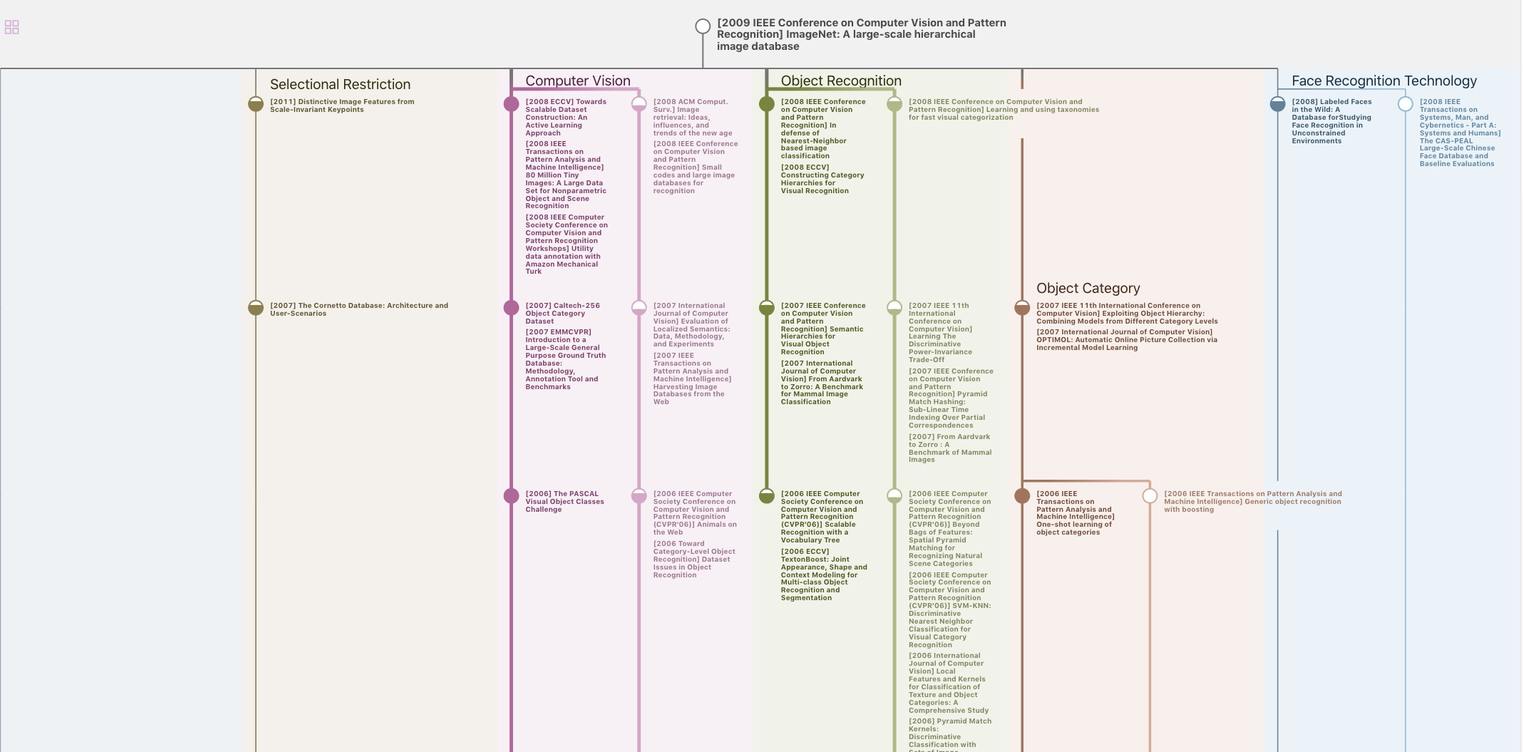
生成溯源树,研究论文发展脉络
Chat Paper
正在生成论文摘要