Rational design process for gas turbine exhaust to supercritical CO2 waste heat recovery heat exchanger using topology optimization
APPLIED THERMAL ENGINEERING(2024)
摘要
Advances in additive manufacturing (AM) technologies and topology optimization methodologies are enabling sophisticated novel designs for heat exchanger performance. These tools have been demonstrated for development of high-performance heat sinks considering local or component-level performance factors (e.g., heat transfer per volume). To leverage such capabilities in larger-scale energy systems, structured design methodologies are needed that consider system-level factors, such as production cost, cycle-level efficiency, and operational constraints. This study seeks to develop and assess a rational approach for designing thermo-economically optimal heat exchangers for such applications. The methodology is illustrated through development of the Primary Heat Exchanger (PHX) for a supercritical carbon dioxide (sCO(2)) power cycle recovering exhaust heat from a 6 MW-scale natural gas turbine. The proposed approach begins with a detailed thermodynamic cycle model, which is then extended to account for techno-economics. Next, an optimal PHX heat transfer capacity target is identified, and a high-level geometry is selected based on operating characteristics. This geometry is then divided into repeating 2D prismatic unit cells, for which topology optimization is applied to identify high-performance heat transfer geometries. A key aspect of this process is that the unit cell geometries are optimized using the total PHX mass as the objective function, which represents a surrogate for production cost. This leads to distinct designs compared with approaches that optimize local heat transfer and flow resistance factors. A second topology-optimized design is developed using a representative local thermal-fluid performance objective function and is found to require 1.6x the mass of the design generated with the system-level techno-economic objective for the same unit cell size. Conventional-type PHX designs with simple longitudinally finned tubes are developed for comparison, and are found to require total masses 1.5x or greater than the design obtained with the proposed process. Integrating this approach with detailed additive manufacturing costing models and experimentally validated fabrication constraints can yield a streamlined workflow for HX design for future energy systems.
更多查看译文
关键词
Topology optimization,Additive manufacturing,Heat exchanger,Supercritical carbon dioxide
AI 理解论文
溯源树
样例
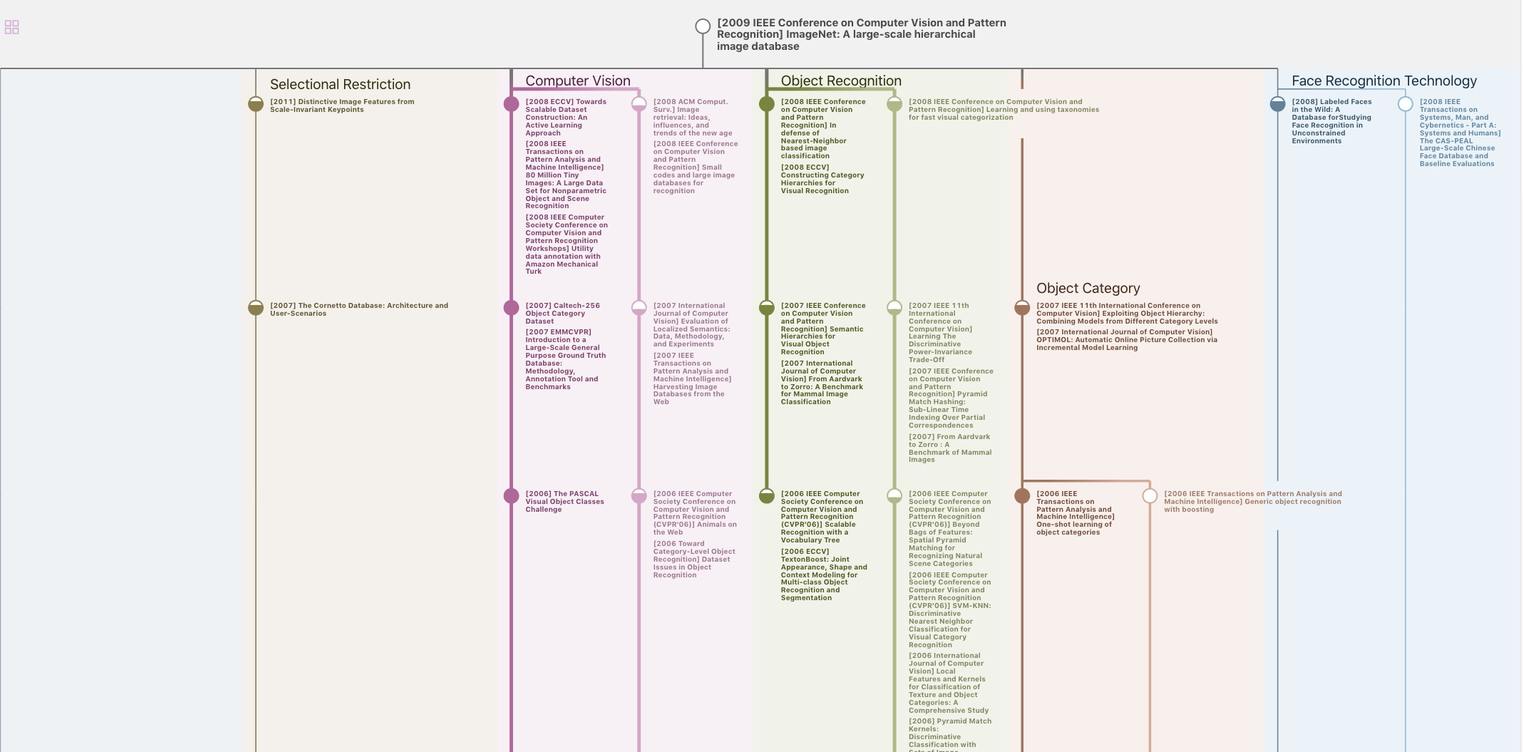
生成溯源树,研究论文发展脉络
Chat Paper
正在生成论文摘要