Investigation of rotary ultrasonic vibration assisted machining of Nomex honeycomb composite structures
The International Journal of Advanced Manufacturing Technology(2023)
摘要
The applications of Nomex honeycomb composite (NHC) structures in aerospace, automotive and defence sectors have been significantly increasing due to their high compressive strength, hexagonal thin-walled structure, ultra-light weight and excellent thermal resistance. Specific applications include composite sandwich structures in helicopter propellers, satellite cabins, aeroplane floors, engine cowls, wings and nacelles. Accuracy of the machined surface of NHC structures is required for adhesive bonding with face-sheets. Conventional machining processes generate machining defects in terms of tearing, damaged cell walls, burr formation, delamination and poor surface quality that result in reduction of strengths of the core structure and its bond with face sheet. Ultrasonic machining is a proven technique to overcome such machining defects and improve the surface quality of NHC structures. Novelty of this research includes the development of a three-dimensional (3D) finite element model to analyse cutting forces, chip formation and machining quality of NHC structures using disc cutter through both ultrasonic and conventional machining processes by providing feed to the workpiece instead of the cutting tool. The significant influence of machining parameters such as depth of cut, feed rate, ultrasonic amplitude and spindle speed on cutting forces was investigated numerically followed by experimental validation. Numerical model in support with experimental results show that cutting forces decrease by increasing ultrasonic amplitude and spindle speed (up to 54.74
更多查看译文
关键词
Nomex honeycomb composites (NHC),Rotary ultrasonic machining (RUSM),Cutting force,Hashin failure criteria,Surface morphology,Finite element model,Disc cutter
AI 理解论文
溯源树
样例
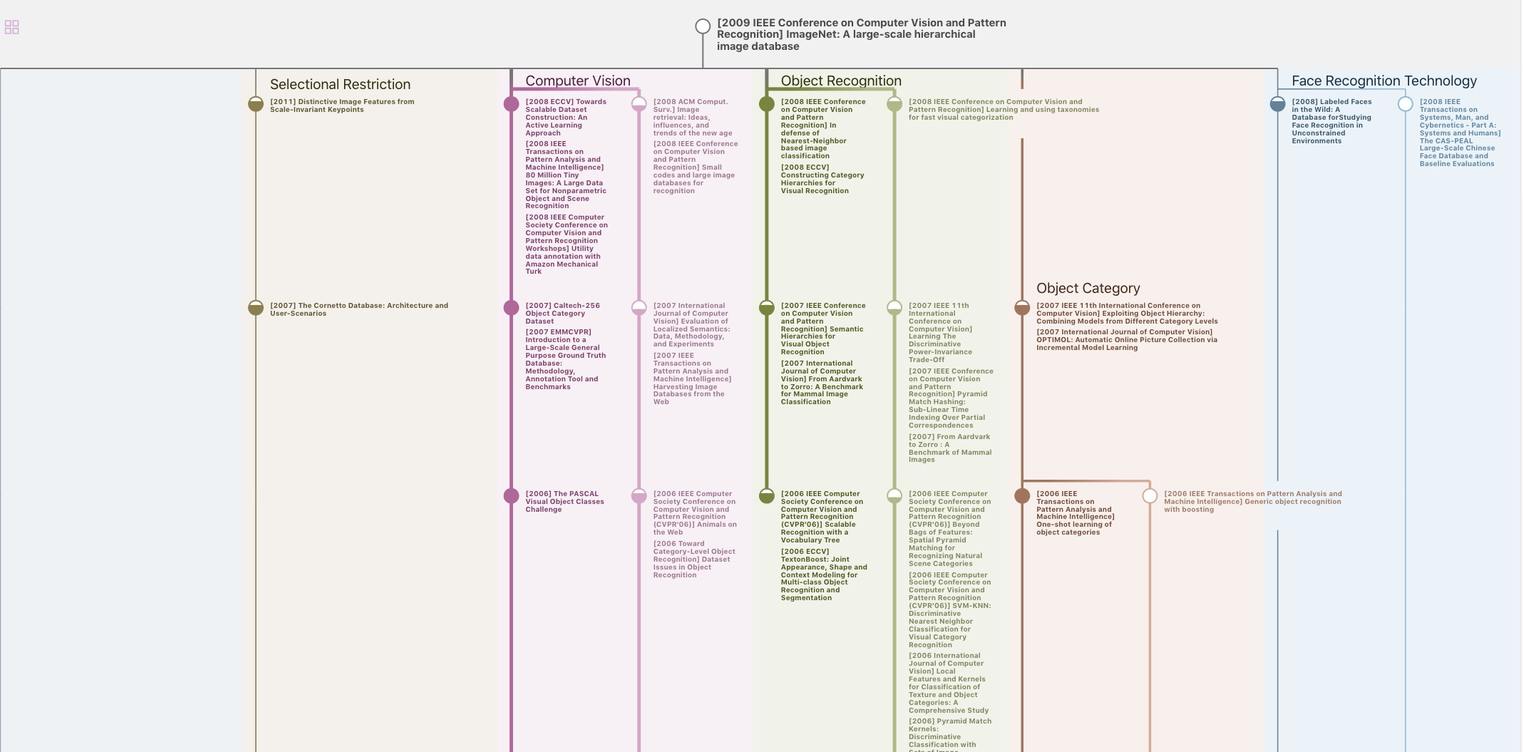
生成溯源树,研究论文发展脉络
Chat Paper
正在生成论文摘要