Effect of Welding Microstructure on Stress Relaxation Cracking Studied by Controlled Residual Stress Generation in a 316L(N) Austenitic Stainless Steel
METALLURGICAL AND MATERIALS TRANSACTIONS A-PHYSICAL METALLURGY AND MATERIALS SCIENCE(2023)
摘要
The influence of heterogeneous welding microstructure on the stress relaxation cracking (SRC) in the SRC-resistant 316L(N) steel was investigated. To trigger SRC, pre-straining by compression was applied after the welding and before subsequent stress relaxation by heat treatment. To this end, compact tension (CT) type specimens were extracted from thick plates welded on both sides. The notch was aligned with the welding centreline and notch root across the thickness, thereby crossing the heterogeneous microstructure. Residual stresses and strain fields induced by welding and pre-compression were estimated by 3D finite element simulations and values of the same order of magnitude were obtained for all regions of the weld. After thermal heat treatment at 575 degrees C for 580 and 1470 hours of the welded and further pre-strained CT samples, intergranular cavities and cracks similar to those found after the creep were observed. Cavities appeared exclusively on intergranular carbides and associated intermetallic precipitates. In the fusion zone (FZ), cavities preferentially nucleated on phases issued from the decomposition of the vermicular ferrite formed during welding. The highest number of cracks was systematically found in the coarse grain heat-affected zone (CGHAZ) of the weld. An increase in both pre-compression load and relaxation time led to an increase in damage after the heat treatment.
更多查看译文
关键词
welding microstructure,austenitic stainless steel,controlled residual stress generation,stress relaxation
AI 理解论文
溯源树
样例
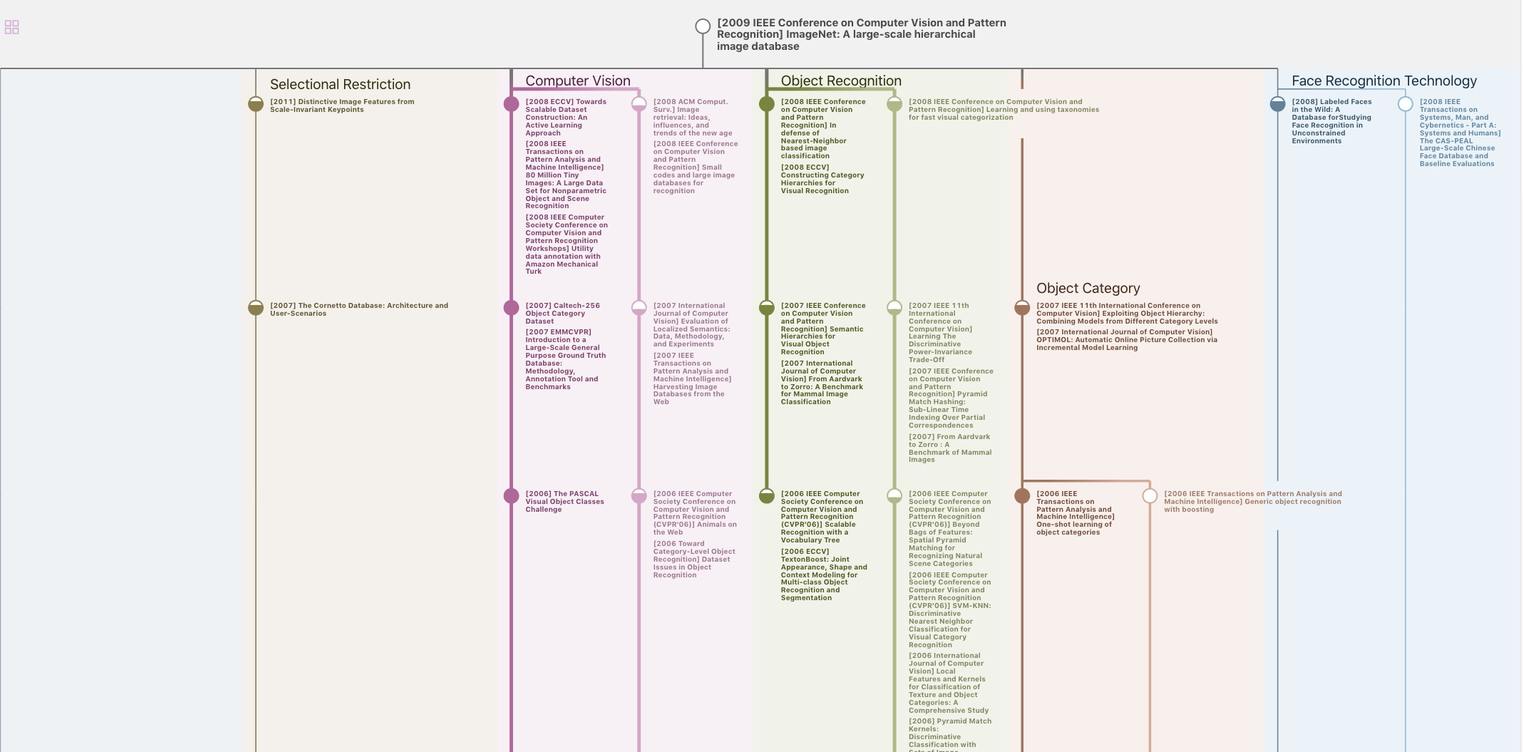
生成溯源树,研究论文发展脉络
Chat Paper
正在生成论文摘要