Formation Mechanisms of Hot Cracks in Laser Additive Repairing Single Crystal Superalloys
ACTA METALLURGICA SINICA(2023)
摘要
Hot cracking is a prevalent defect in metallurgy that often occurs during the laser additive repair of single crystal superalloys. The understanding of the cracking mechanism is vital for defect prevention. Consequently, this study entails combining experimental analysis and theoretical calculations to investigate the hot cracking mechanism in a second-generation single crystal superalloy, DD432, during laser additive repairing. The incident of hot cracking was observed predominantly at high-angle grain boundaries (HAGBs). High-magnitude stress concentrations were identified on both sides of the crack, accompanied by an extensive distribution of MC-type carbides in the crack initiation region. Hot cracking depended on factors such as liquid film stability, stress concentration, and MC-type carbide precipitates. The stability of the liquid film depended on dendrite coalescence undercooling, which in turn was related to the angle of grain boundaries. According to Rappaz's theory of dendrite coalescence undercooling, the calculated dendrite coalescence undercooling at HAGBs was 395 K. This figure was substantially higher than the 38 K liquid film undercooling found within a single dendrite, and far exceeded the undercooling at a low-angle grain boundary (3.6 degrees) with a value of 56 K. The elevated level of stress concentration served as a driving force for crack initiation and propagation. MC-type carbide precipitates promoted crack initiation through a pinning effect on the liquid feed, thereby weakening the interface bonding strength with the substrate.
更多查看译文
关键词
single crystal superalloy,hot crack,additive manufacturing,microstructure,liquid film stability
AI 理解论文
溯源树
样例
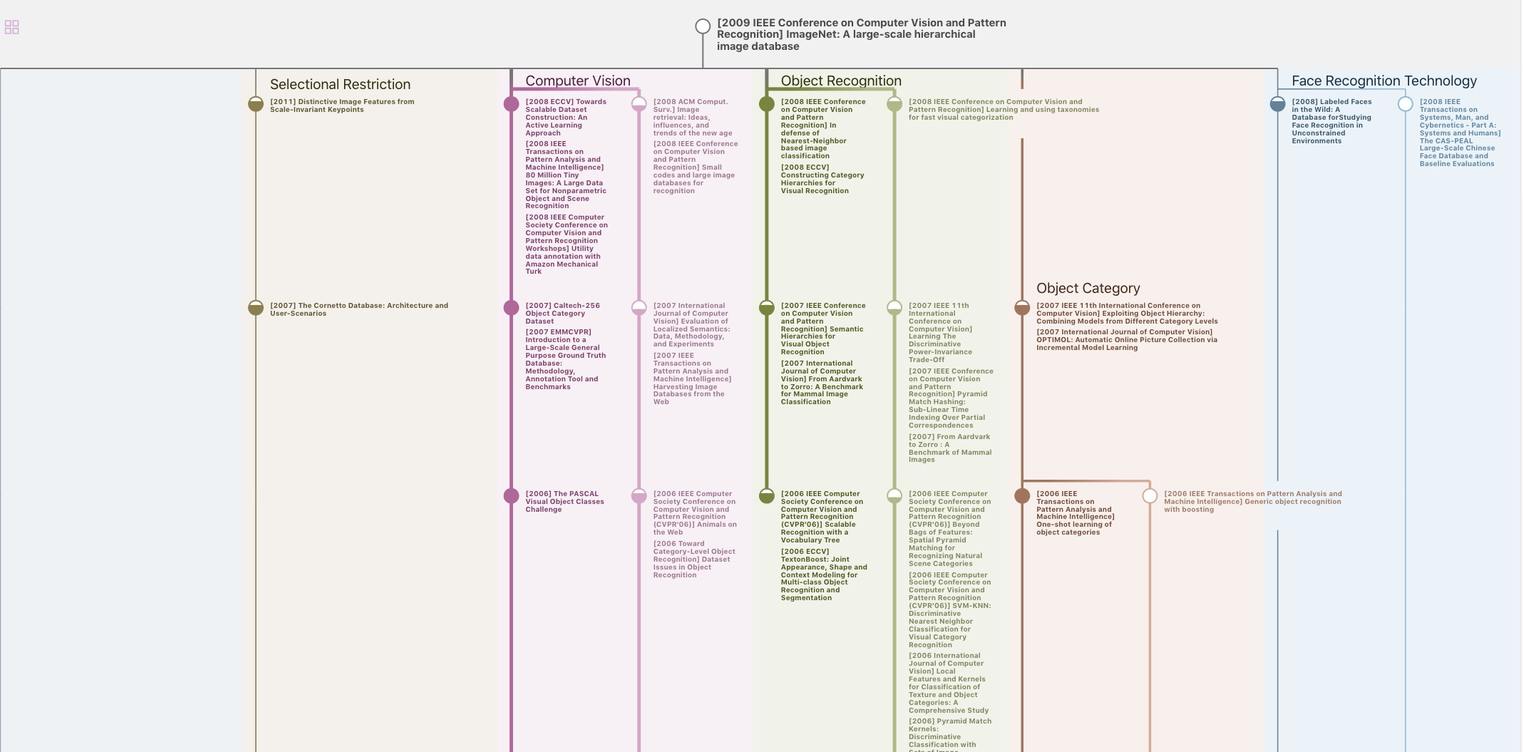
生成溯源树,研究论文发展脉络
Chat Paper
正在生成论文摘要