Improving the wear resistance of 3D printed spur gears through a free-form tooth flank optimization process
MATEC Web of Conferences(2023)
摘要
Involute gears have traditionally been the preferred choice for gear transmission systems due to their simplicity and interchangeability. However, there are applications where they do not provide the most durable and efficient solution. While the cost of implementing optimized non-involute gears in most applications often outweighs their comparative advantages, the advent of additive manufacturing has opened up possibilities for designers to explore alternative gear tooth profiles. This is particularly relevant in the realm of plastic gears, where optimized non-involute gears produced through 3D printing can address their primary drawbacks, such as surface durability and wear resistance. In this study, a comprehensive free-form optimization process was conducted to determine the optimal tooth profile that minimizes wear on 3D printed spur gears during operation. The tooth flank geometry was represented using a 4th order B-spline curve, and a genetic algorithm was employed to determine the optimum positions of the control points aiming to minimize wear depth across the tooth flanks. The spur gears were manufactured using Fused Deposition Modeling (FDM) with PLA material. The parameters of the additive manufacturing process were experimentally fine-tuned to achieve the best possible accuracy. To evaluate the performance of the optimized free-form gears, two case studies were implemented, demonstrating that the optimized gears achieved a remarkable reduction of average wear depth by more than 50% and a reduction of maximum wear depth by more than 69% compared to standard involute gears. To further validate the effectiveness of the optimization method, experiments were carried out using an FZG test rig. The profiles of the tooth flanks were measured on a Coordinate Measuring Machine (CMM) before and after the experiments to compare the wear depth against the standard involute gears. The results revealed a significant improvement in the wear resistance of the tooth flanks, with a reduction of wear depth of 44.1%.
更多查看译文
关键词
spur gears,wear resistance,free-form
AI 理解论文
溯源树
样例
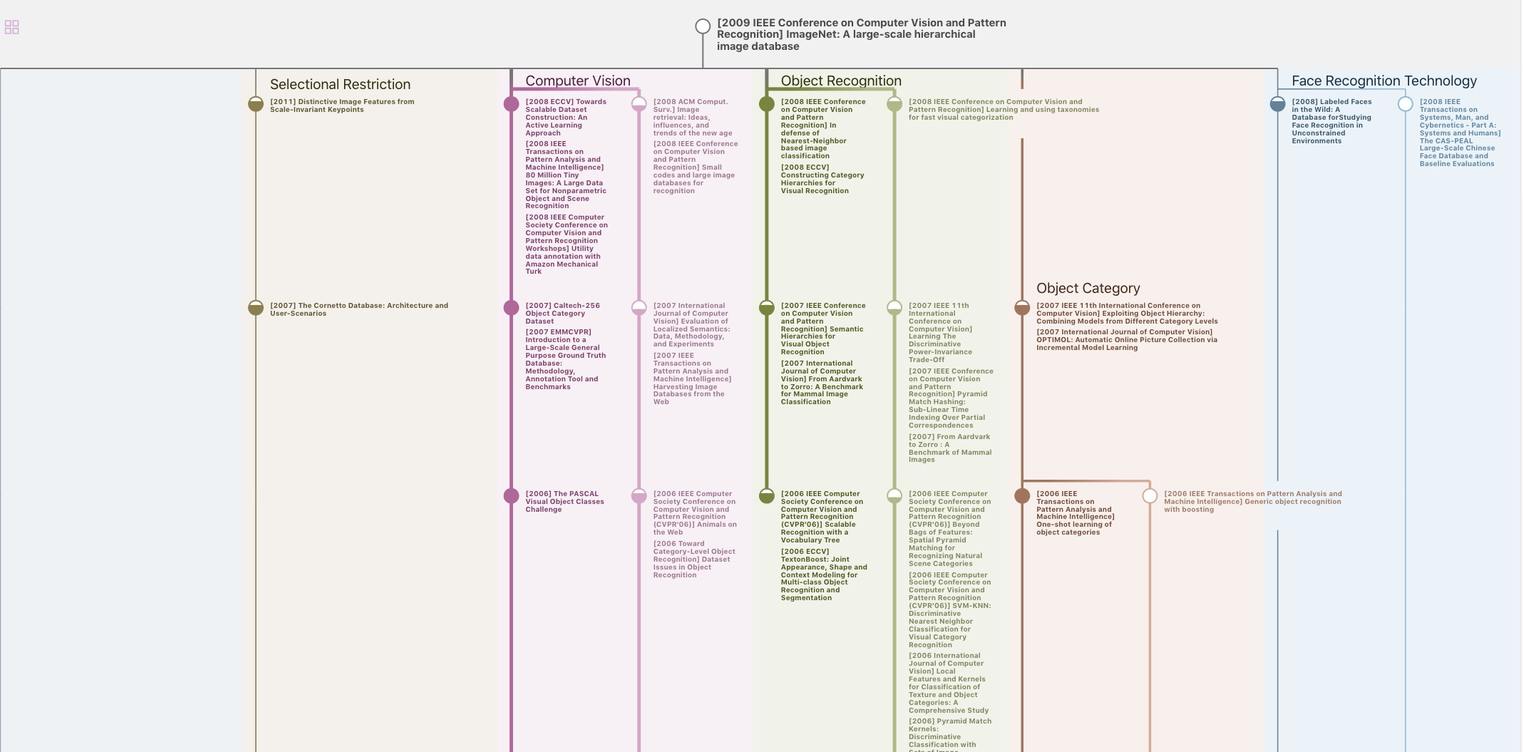
生成溯源树,研究论文发展脉络
Chat Paper
正在生成论文摘要