A Digital Twin Based Framework for Real-Time Machine Condition Monitoring.
CASE(2023)
摘要
Condition Monitoring (CM) is an important approach to extending the life of complex equipment by forecasting the outcome of an event before catastrophic failure occurs. Recent advancements in digital twins (DT) offer additional benefits to machine condition monitoring. In this study, a framework based on DT for real-time condition monitoring of industrial machines is proposed. The multi-layer DT framework consists of a physical entity (PE), virtual equipment (VE), edge device, fidelity service and digital twin services. The virtual equipment is a replica of the physical entity or the monitored machine. It also contains a cloud platform to store data online and an application to interface with the cloud enabling users to check the data remotely. The fidelity service ensures conformity between the PE and the VE. The digital service provides optimal operation and maintenance schedules based on the data from both physical and virtual spaces. The integration of the edge layer enables real-time handling of high-frequency machine data for effective health monitoring. The validity of the proposed framework is demonstrated with a case study based on monitoring a critical component of an industrial drivetrain test rig. The features of the framework allow end-users to visualize the component's real-time health status remotely.
更多查看译文
关键词
additional benefits,catastrophic failure,cloud platform,complex equipment,digital service,digital twin services,edge device,edge layer,effective health monitoring,fidelity service,high-frequency machine data,industrial machines,machine condition monitoring,maintenance schedules,monitored machine,multilayer DT framework,optimal operation,physical entity,physical spaces,real-time condition monitoring,real-time handling,real-time health status remotely,real-time machine condition,store data,virtual equipment,virtual spaces
AI 理解论文
溯源树
样例
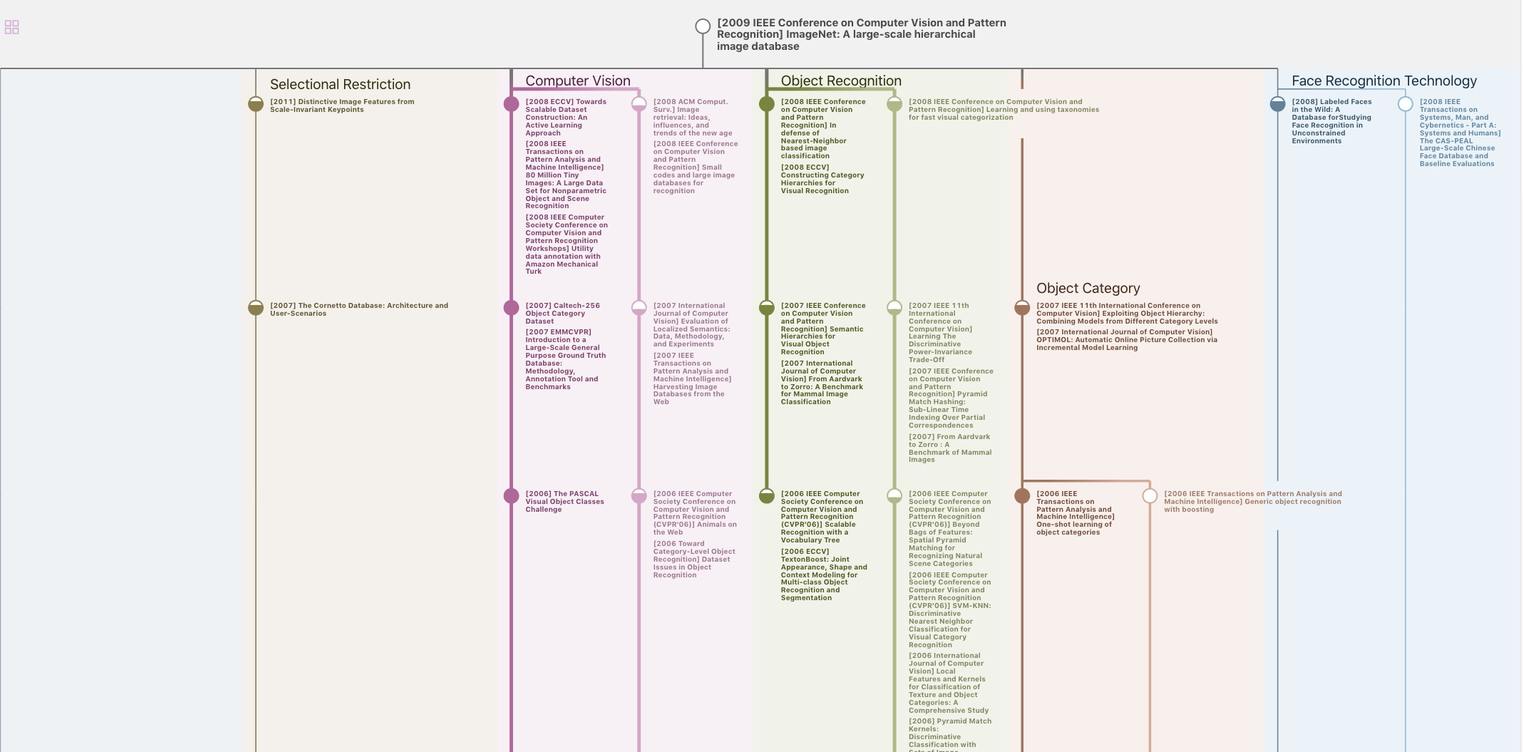
生成溯源树,研究论文发展脉络
Chat Paper
正在生成论文摘要