Influence of non-Newton rheological parameters of drilling fluid on axial-lateral-torsional coupling vibration of rotating drill string
GEOENERGY SCIENCE AND ENGINEERING(2024)
摘要
In the process of drilling, the drill string will inevitably produce vibration, increase the difficulty and risk of drilling, and bring huge economic losses. The effects of drilling fluid properties on unidirectional vibration (axial, lateral and torsional) of drill string have been studied in the existing literature. In order to explore the influence mechanism of non-Newton rheological of drilling fluid on axial-lateral-torsional coupling (ALTC) vibration of drill string, an ALTC nonlinear dynamic model based on Hamilton's principle was established, taking into account the effect of Herschel-Bulkley non-Newton rheological (HBNR) damping, bit-rock interaction and drillstring-borehole contact. The Newmark-beta method was used to solve the nonlinear discrete equations of the system. The validity of the model was verified through the field measurement data. The research results show that larger yield stress and consistency coefficient (tau(Hy) = 7, k = 5), and smaller power-law exponent (n = 0.2) can better suppress the axial vibration of drilling string and reduce the risk of bit jumping. Larger yield stress and consistency coefficient (tau(Hy) = 7, k = 5) and power-law exponent n = 0.8 can better suppress lateral vibration of drilling string and maintain hole diameter. The larger consistency coefficient and power-law exponent (k = 5; n >= 0.8) can better suppress the stick-slip vibration of the drill string and improve ROP. The results can provide a theoretical guidance for drilling fluid reduction vibration control.
更多查看译文
关键词
Rotary drilling,Drill string vibration,Coupling vibration,Drilling fluid rheology,Stick-slip vibration
AI 理解论文
溯源树
样例
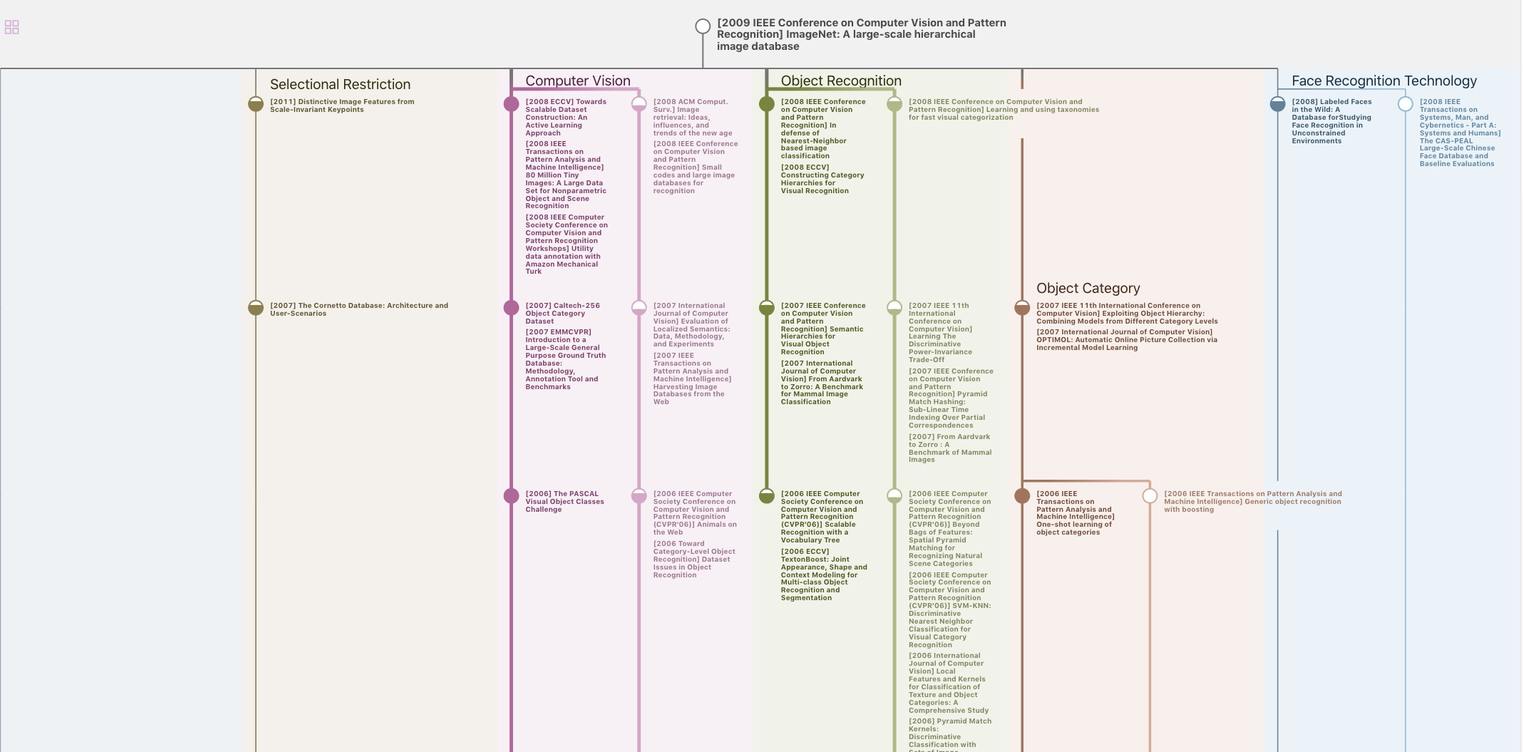
生成溯源树,研究论文发展脉络
Chat Paper
正在生成论文摘要