Properties of 316L Stainless Steel Formed by Dual-Laser Selective Melting
Chinese Journal of Lasers(2023)
摘要
Objective In order to explore the differences of selective laser melting (SLM) formation in three modes: single laser scanning, dual -laser low -power synchronous scanning (the power of two lasers becomes half of the power of the single laser, and the other parameters remain unchanged) and dual -laser high-speed synchronous scanning (the speed of two lasers becomes double of the speed of the single laser, and the other parameters remain unchanged), we investigated the feasibility of forming stainless steel with the dual -laser and the impact of the techniques on forming quality. The study provides experimental support and a theoretical basis for high -efficiency forming research of multi -galvanometer multi -laser selective melting equipment. Methods Self -developed dual -laser synchronous scanning equipment was used to form 316L stainless steel samples under the same energy density through single -laser and dual -laser synchronous scanning. The corrosion samples were used to observe the morphology and microstructure of the molten pool. Finally, according to the above results, appropriate process parameters were selected, tensile samples were prepared, the mechanical properties of the samples formed with three modes were compared, and the fracture morphology was observed. Results and Discussions As far as spatter is concerned, compared with a single laser, dual -laser low -power synchronous scanning method is beneficial for increasing the depth of the molten pool and increases the metallic jet. At the same time, in dual -laser high-speed synchronous scanning mode, owing to the increase in the laser beam energy and shortened interaction time between the laser and powder, a higher temperature gradient occurs, which aggravates the Marangoni effect. The high-temperature bottom of the molten pool flows to the low -temperature sidewalls and rear edges, and more liquid flows from the molten pool at a certain initial velocity, thereby increasing the droplet spatter (Fig. 6). Compared with the single lase forming sampler, the density of dual -laser low -power synchronous scanning formed sample is more sensitive to the laser power and increases linearly with the increase in power. This is owing to the influence of the superposition of the double beams. When the laser power is low, the temperature of the molten pool is relatively low, resulting in poor fluidity, and the retained gas cannot escape the molten pool in time, resulting in internal pore defects, which reduces the relative density of the sample. For dual -laser high-speed synchronous scanning, the density of the sample is comparable to that of a single laser and the range of density variation is extremely small. This may be because the energy threshold required for shaping is achieved even at relatively low laser power. Compared with the single laser mode, the molten pool distribution of dual -laser low -power synchronous scanning was more uniform, and the distance between the bottoms of the molten pools increases by approximately 25%, from 32 mu m +/- 5 mu m to 40 mu m +/- 5 mu m (Fig. 9). Because the laser spot has a Gaussian distribution, when the laser power is reduced, the circular area that can reach the melting point decreases, but the two laser beams are scanned synchronously, and most of the energy of the second beam spot acts directly on the molten pool instead of the powder; hence, the depth of the molten pool increases. However, for dual -laser high-speed synchronous scanning, with the increase of laser power, the molten pool becomes wide and deep from wide and shallow. Compared to the molten pool formed by a single laser, the width direction changed significantly, and the most intuitive change is that the overlap ratio exceeds 50%. The laser beam is in contact with the powder, and heat spreads in the horizontal and vertical directions. For dual - laser high-speed synchronous scanning forming in this experiment, when the power is low, it is easy to produce a wide and shallow molten pool. When the power is increased to 240 W, an excessively high power causes the current layer to combine with the molten pool of the previous layer, resulting in a larger molten pool. Conclusions 1) The dual-laser synchronous scanning method can be used to form 316L stainless steel samples. The density of the samples is above 99%, the tensile strength can reach 720 MPa, and the elongation rate exceeds 40%, meeting application requirements. 2) Both single laser forming and dual-laser high-speed synchronous scanning forming, the interior of the grain is dominated by columnar subcrystals, but the width of the single laser subcrystal is 0.50 p.m, while the latter is approximately 0.35 p.m. Columnar, equiaxed, and elongated equiaxed subcrystals coexist under dual-laser low-power synchronous scanning mode. 3) Dual-laser high-speed synchronous scanning method can double the forming efficiency.
更多查看译文
关键词
laser technique,metal additive manufacturing,selective laser melting,316L stainless steel,dual-laser,energy density,mechanical properties
AI 理解论文
溯源树
样例
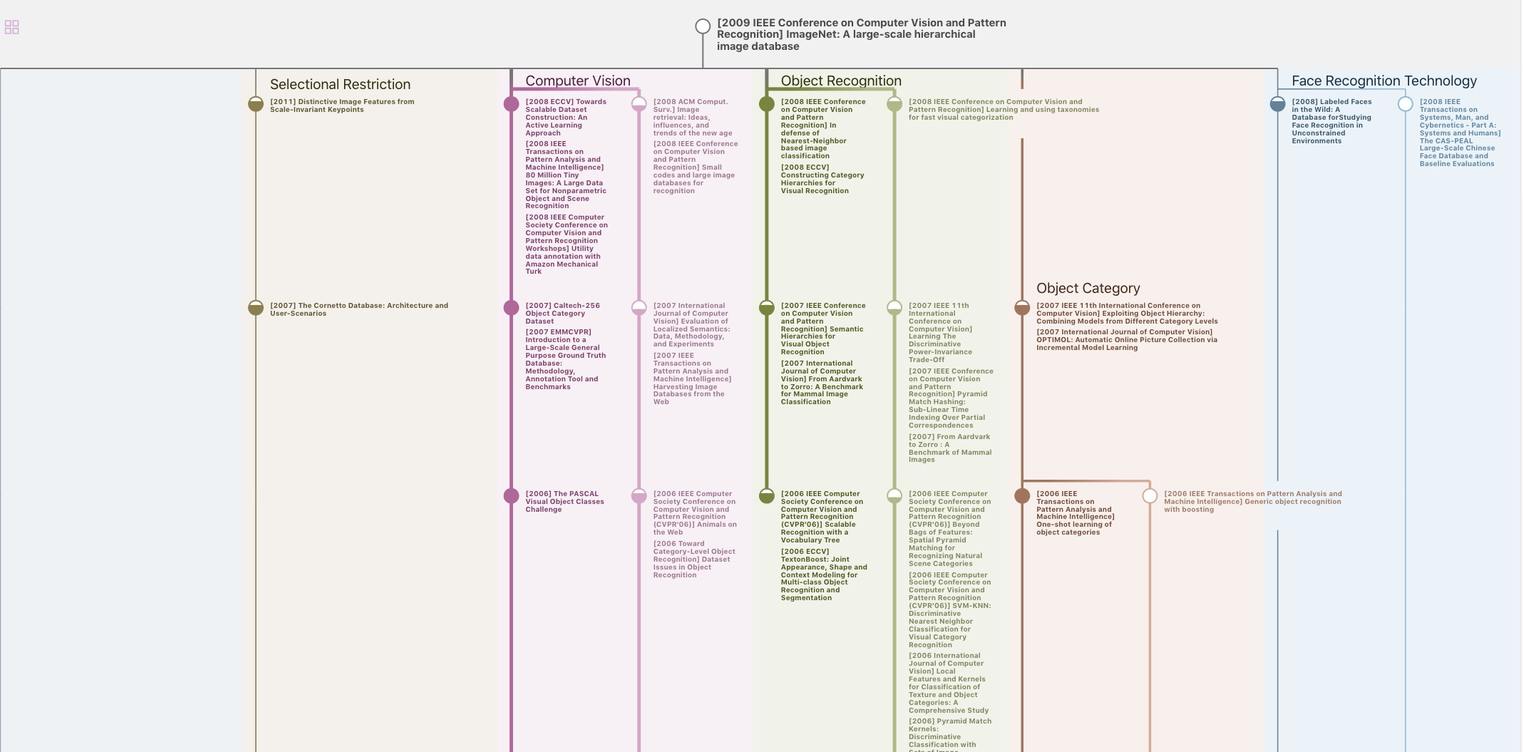
生成溯源树,研究论文发展脉络
Chat Paper
正在生成论文摘要