Path Planning for the Gantry Welding Robot System Based on Improved RRT
ROBOTICS AND COMPUTER-INTEGRATED MANUFACTURING(2024)
摘要
In the shipbuilding industry, various workpieces are often produced in small batches. A new program must be written for new workpiece to be processed, which leads to the inefficiency of the traditional teaching programming method. In particular, some manufacturers have applied large gantry structures to robots to improve their handling space. Although the external positioning device enhances the robot's flexibility, it also increases the difficulty of path planning. The RRT* algorithm based on sampling is widely used in the path planning of manipulator for its efficient expansibility and probability completeness. However, in the robot system equipped with gantry structure, the increase of freedom makes its efficiency relatively low. Therefore, this article presents an improved RRT* algorithm for autonomous path planning of welding robots with a large gantry structure. This method introduces the sampling pool mechanism, and selects the node nearest to the connection line between the starting node and the target node in the sampling pool, which effectively shortens the length of the search path. In addition, it adopts the strategy of limiting the nearest node to prevent the transitional search of the configuration space. The improved RRT* algorithm proposed in this paper is verified in complex environment, and compared with improved algorithms such as IB-RRT*, the path cost and time cost are increased by 22.2% and 32.5%, respectively, and the success rate is relatively stable.
更多查看译文
关键词
welding robots,gantry structure,path planning,RRT*
AI 理解论文
溯源树
样例
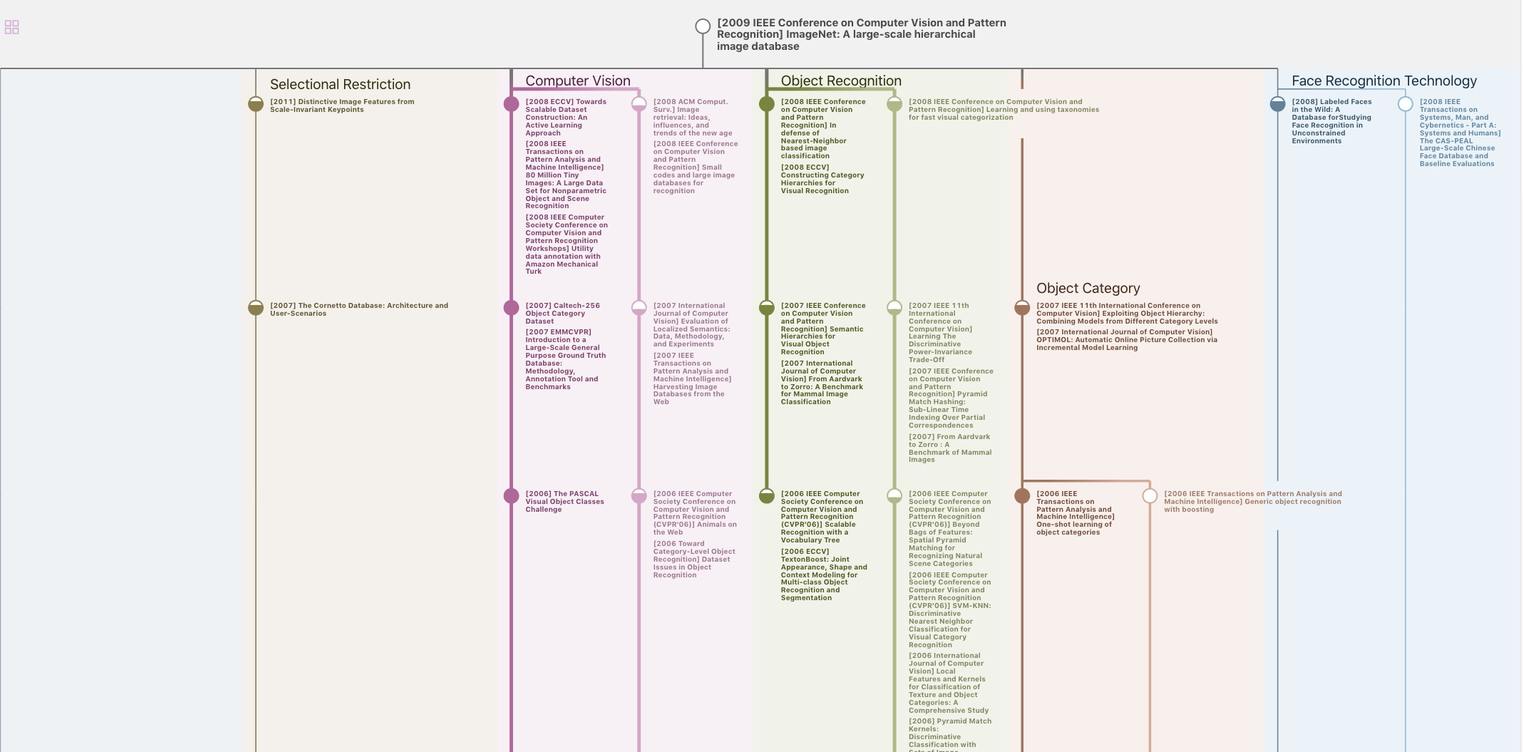
生成溯源树,研究论文发展脉络
Chat Paper
正在生成论文摘要