Effects of Different Process Strategies on Surface Quality and Mechanical Properties of 316L Stainless Steel Fabricated via Hybrid Additive -Subtractive Manufacturing
Chinese Journal of Lasers(2023)
摘要
Objective Laser directed energy deposition (LDED) is an additive manufacturing (AM) technology that uses a high-energy laser beam to melt metal powder and deposit it on a substrate. This technology can directly manufacture large-scale parts with high forming efficiency using a high-power laser. Hybrid additive-subtractive manufacturing can address the inherent problems, such as poor surface quality and low dimensional accuracy of LDED paris. Laser additive-subtractive hybrid manufacturing mainly consists of two methods. One is to perform milling surface-finishing after additive manufacturing is completed. The other is to perform milling during additive manufacturing. In this study, the influence of the interaction between adjacent layers printed using additive manufacturing along with milling subtractive manufacturing on the surface quality and mechanical properties of the final product was discussed. Methods A robotic hybrid additive-subtractive manufacturing system was developed in-house for fabricating 316L stainless steel samples. The laser, powder feeders, and high-speed electric spindles were integrated on two ABB robots. A 316L stainless steel powder with a particle size range of 15-53 pm was used and delivered with high-purity argon as a carrier through the nozzle. A single- factor experiment was designed to assess the optimal hatch space for robotic additive manufacturing. The hatch space was set to 2-4 mm for comparing the cross-sectional size of the single melting channel. An orthogonal design experiment with four factors and three levels was designed to determine the optimal robot parameters for the subtractive milling process. The surface quality and mechanical properties of 316L stainless steel fabricated with different processing strategies were studied using the parameters obtained above. Results and Discussions An excessively large or small hatch space affects the unevenness of the deposited layer, as well as the shape and mechanical properties of the fabricated 316L sample. By comparing the morphology, vertical section (Fig. 4), and mechanical properties [Fig. 5 (b)] of the samples obtained at different hatch space values, the hatch space with the beat comprehensive mechanical properties was 2.5 mm. The variance analysis of the orthogonal experiment results (reported in Tables 3 and 4) demonstrates that the impact of different robot milling process parameters on the surface quality of milling additive manufacturing samples varies; specifically, we obtain the following ordering from large to small influence. the spindle speed, milling width, feed rate, and milling depth. There is no significant difference in the surface roughness and microhardness of the samples between the two processing strategies (Fig. 10), and the surface roughness and microhardness of the top surface of both are better than those of the side. In terms of mechanical properties, there is also no significant difference between the two strategies (Fig. 11). Therefore, we conclude that the additive manufacturing aacompanying with milling does not harm the surface quality and mechanical properties of the formed samples, and adding subtractive manufacturing process in the process of additive manufacturing will not have a negative impact on the samples. The 316L stainless steel valve mould parts were manufactured using additive manufacturing accompanying with milling. The length, width, and surface roughness values of the 3161. part are (225 +/- 0.17) mm. (150 +/- 0.13) mm, and (0.87 +/- 0.03) mu m, respectively (Fig. 15). The successful manufacture of parts verifies the feasibility of additive manufacturing accompanying with milling that is proposed in this study. Conclusion The best comprehensive mechanical properties of the samples can be obtained by additive manufacturing with 2.5 mm hatch space. With a spindle speed of 3600 r/min. feed rate of 3 mm/s, milling depth of 0.3 mm, and milling width of 3 mm. the observed surface roughness of the samples fabricated by additive manufacturing is optimal. There is no significant difference in the mechanical properties and surface quality of the samples fabricated using the process strategy of milling after additive manufacturing and additive manufacturing accompanying with milling, using the same optimized parameters, indicating that additive manufacturing accompanying with milling strategy is feasible. Valve molds are manufactured with additive manufacturing accompanying with milling strategy, which realizes high dimensional accuracy and high surface quality of valve mold parts in the nuclear power field.
更多查看译文
关键词
ltyhrid additive -subtractive nmanufacturing,robotic based directed energy,deposition,subtractive manufacturing through milling,surface quality,valve mold
AI 理解论文
溯源树
样例
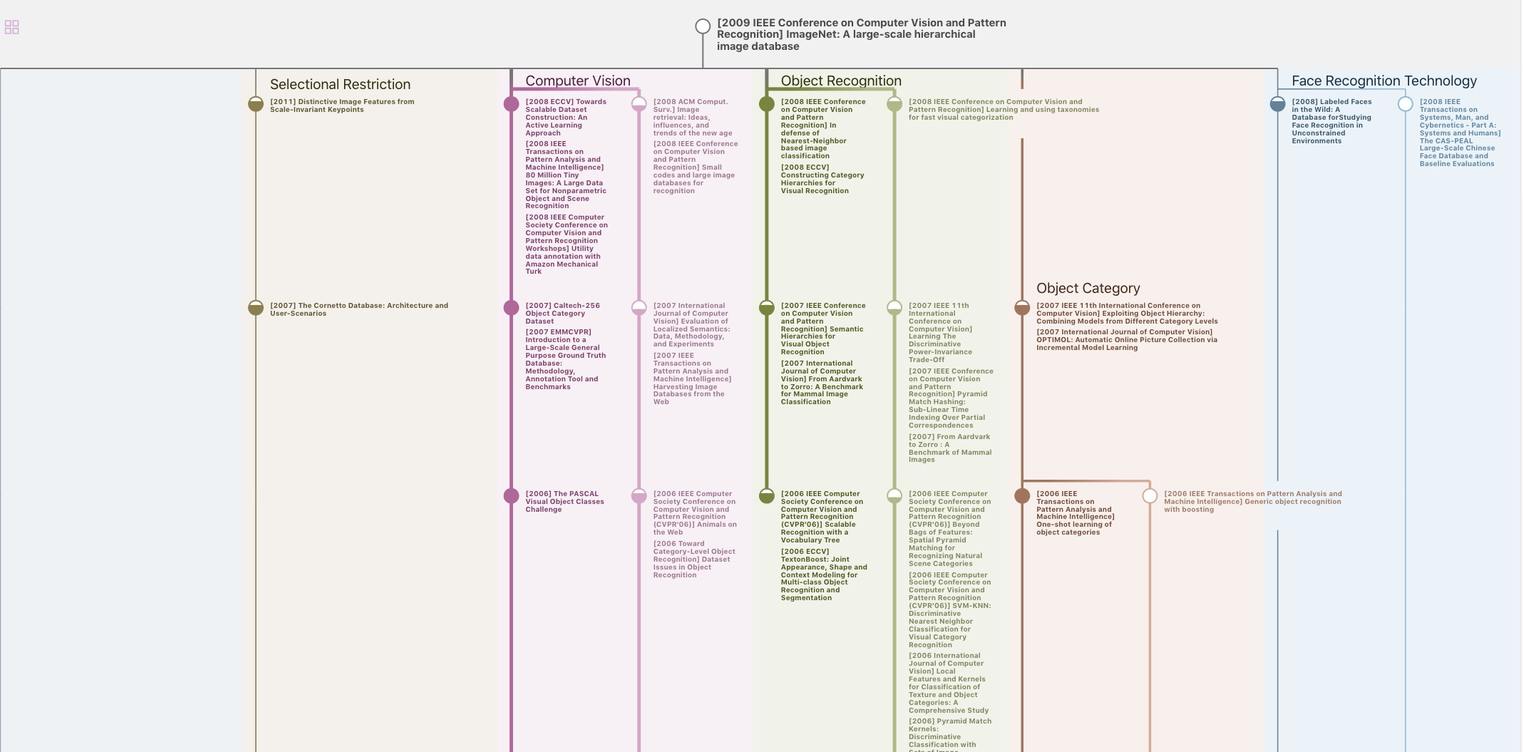
生成溯源树,研究论文发展脉络
Chat Paper
正在生成论文摘要