Role of the position of the laser spot in the failure transition during the tensile test for the laser welding-brazing of galvanized CRRA1000 steel to 5754 aluminum alloy in an overlapped joint
Materials Science and Engineering: A(2023)
摘要
Aluminum-steel dissimilar joints have been widely applied attributing to their advantages to meet the requirements for weight reduction and energy savings. The aluminum alloy 5754 and galvanized CRRA1000 advanced high strength steel (AHSS) are overlap-welded by the laser welding-brazing technique. The tensile test results show that the laser welded joints fabricated with the spot location containing 2/3 steel and 1/3 aluminum are almost failed in the weld metal (WM). The average tensile strength and elongation are 344 MPa and 10%. Larger proportion of laser spot on steel and heat input triggers the formation of the coarsened intermetallic compounds (IMCs), which are rich in elements Fe, Al and Si, in the region near the notch. By decreasing the proportion of laser spot on steel and heat input, uniform IMC layer successfully forms in the interface between the WM and steel. All the welded joints fabricated with the spot location containing 1/2 steel and 1/2 aluminum rupture in the base metal of Al alloy (Al-BM). The average tensile strength and elongation are 345 MPa and 15%. During the tensile test, the cracks are initiated at the notch. The cracks start turning into the WM in the region with coarsened IMC, and the crack propagation direction is mainly along the coarsened IMCs eventually failure in the WM. For the cracks in the uniform IMC, the crack propagation in the uniform IMC is hindered, contributing to the failure transition from the WM to the base metal (BM) of aluminum alloy.
更多查看译文
关键词
galvanized crra1000 steel,laser spot,aluminum alloy,tensile test,welding-brazing
AI 理解论文
溯源树
样例
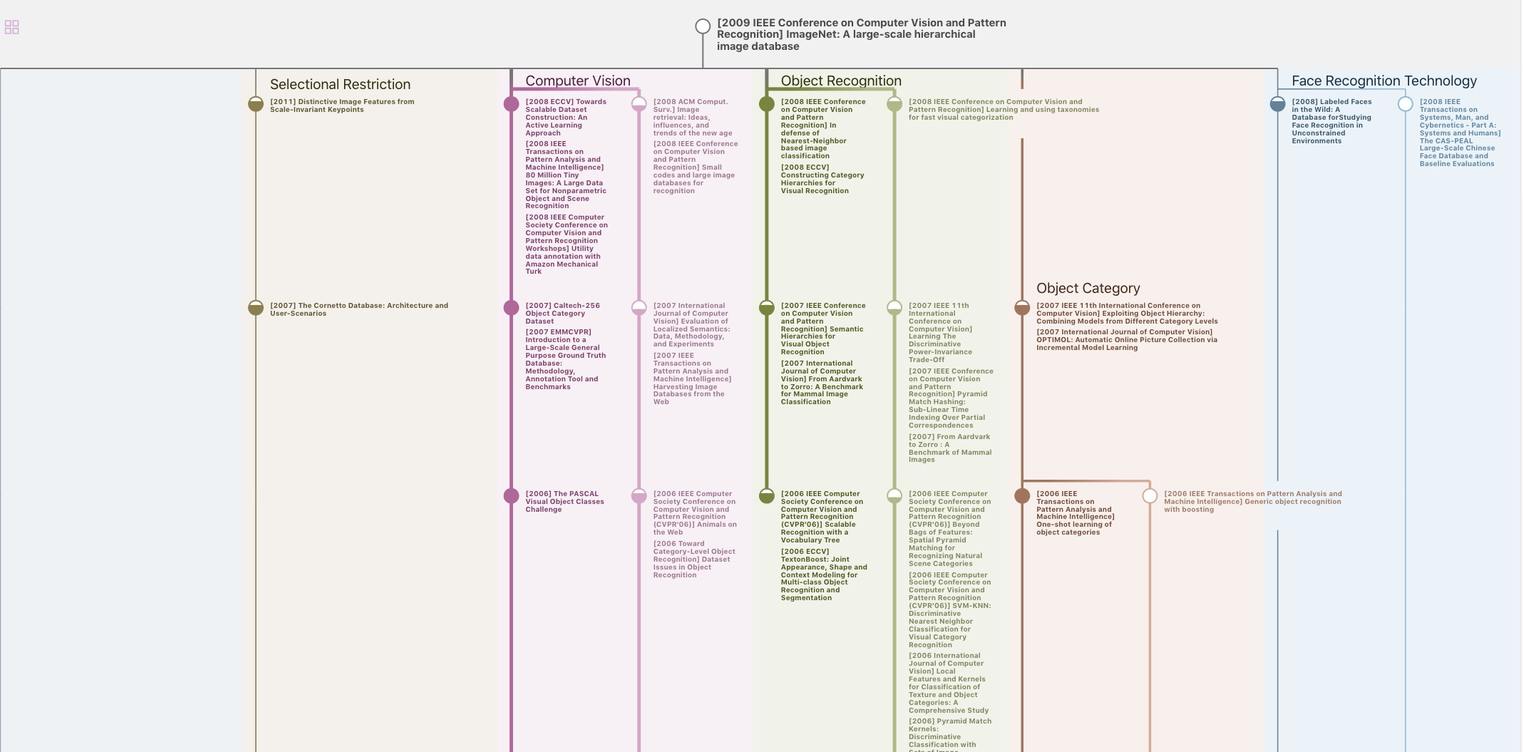
生成溯源树,研究论文发展脉络
Chat Paper
正在生成论文摘要