Effect of Welding Thermal Cycles on Microstructure and Mechanical Properties of Multi-Strand Composite Welding Wire Welded Joints of High Nitrogen Austenitic Stainless Steel
crossref(2019)
摘要
A multi-strand composite welding wire was applied to join high nitrogen austenitic stainless steel, and microstructures and mechanical properties were investigated. The electrical signals demonstrate that the welding process using a multi-strand composite welding wire is highly stable. The welded joints are composed of columnar austenite and dendritic ferrite and welded joints obtained under high heat input and cooling rate have a noticeable coarse-grained heat-affected zone and larger columnar austenite in weld seam. Compared with welded joints obtained under the high heat input and cooling rate, welded joints have the higher fractions of deformed grains, high angle grain boundaries, Schmid factor and the lower dislocation density under the low heat input and cooling rate, which indicate a lower tensile strength and higher yield strength. The rotated goss (GRD) orientation of a thin plate and the cube (C) orientation of a thick plate are obvious after welding, but the S orientation at 65° sections of Euler’s space is weak. The δ-ferrite was studied based on the primary ferrite solidification mode. It is observed that low heat input and high cooing rate result in the increasing of δ-ferrite and high dislocation density was obtained in grain boundaries of δ-ferrite. M23C6 precipitates due to low cooling rate and heat input in weld seam and deteriorates the elongation of welded joints. The engineering stress-strain curves also show the low elongation and tensile strength of welded joints under low heat input and cooling rate, which is mainly caused by the high fraction of δ-ferrite and the precipitation of M23C6.
更多查看译文
AI 理解论文
溯源树
样例
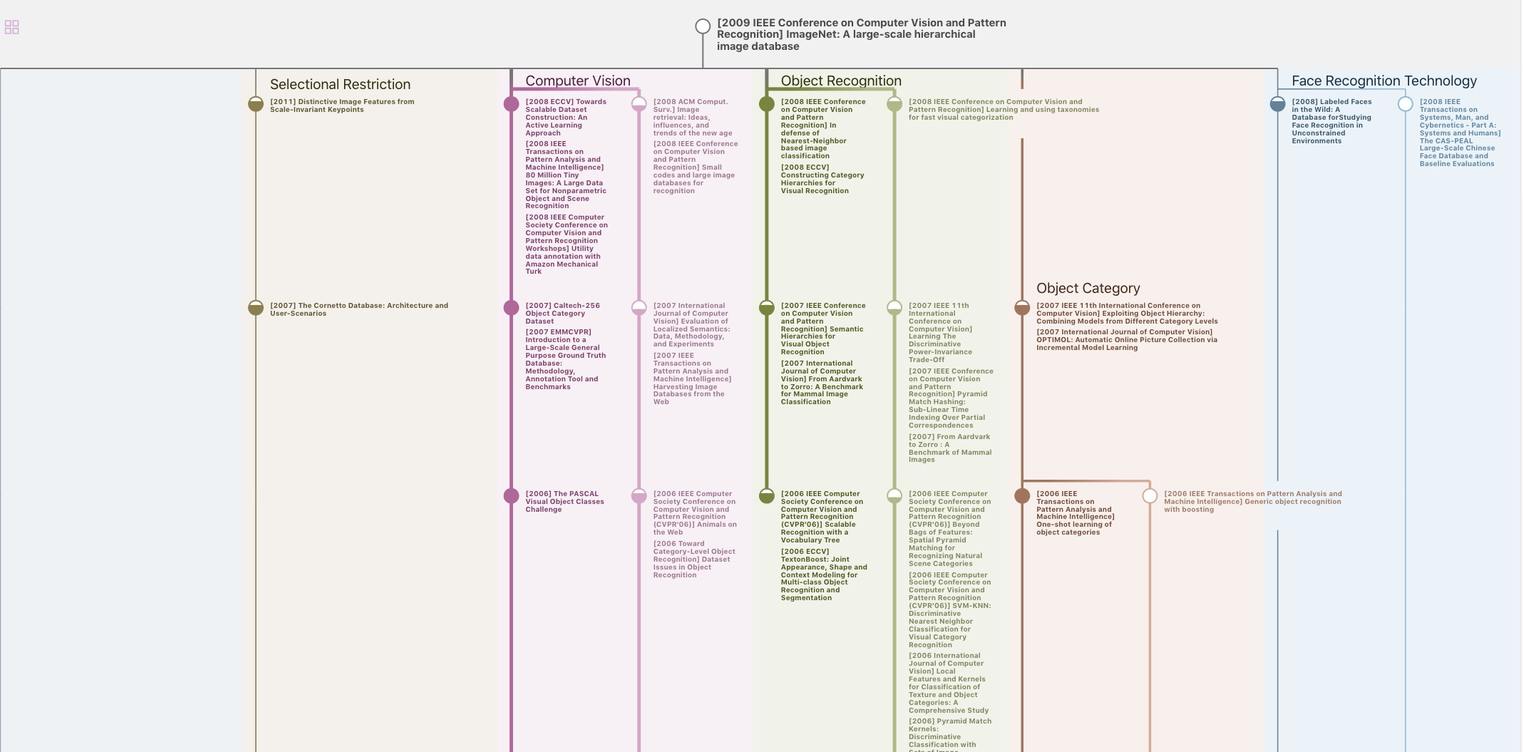
生成溯源树,研究论文发展脉络
Chat Paper
正在生成论文摘要