Integrated 3D Numerical Modelling of Pressure Behavior and Casing Response at Offset Monitor Well During Fracturing
Day 2 Wed, February 01, 2023(2023)
摘要
AbstractOffset monitor wells experience stress, strain and pressure changes due to far-field fracture propagation. The pressure interference as hydraulic fractures propagate and intersect the casing directly results in a casing inner volume change and monitor well surface pressure change. The pressure behavior has been analyzed by a patented method, Sealed Wellbore Pressure Monitoring (SWPM), and it is an effective means to detect frac hits. To extend the understanding of this pressure behavior for wider applications, we proposed a methodology of simulating the casing response and corresponding pressure change of the offset well during hydraulic fracturing. The objective is to investigate the strain/pressure response along the monitor well casing for different scenarios of fracture intersection.In this study, an analytical model for computing the stress/strain in a casing-cement-formation system was developed based on the well-known solution of stress in a thick wall cylinder. The integrated numerical model consists of a fracture propagation model, a 3D geo-mechanical model, and a transient fluid flow model. Prior to analyzing the monitoring well pressure response, fracture propagation is modeled using a commercial software to give information of fracture geometry and fracture net pressure. The 3D fluid flow model and the geo-mechanical model of fractured rock and monitor well casing were established with finite-element method. With the input parameter of fracture geometry and net pressure distribution from the fracture propagation model, the integrated model can be used to solve the total stress-displacement behavior within the simulation domain. Using this approach, the volume change of the monitor well casing, and the corresponding surface pressure behavior can be estimated. The simulated strains along the monitor well casing of a radial fracture show the numerical simulation results agree well with the existing analytical solution.When a fracture crosses the monitor well, the standard surface pressure behavior is: (A) pressure increases due to fracture intersection; (B) pressure increase slows down as fracture tip travels some distance away from the casing; (C) pressure declines after the treatment well is shut-in. The first pressure increase is caused by casing radius reduction while the pressure fall-off is greatly affected by the far-field leakoff coefficient and permeability. The simulated results, and also the published data indicate that the typical pressure response for a single fracture hitting is on the order of 1 psi. When multiple fractures intersect the casing, a higher surface pressure increase is observed compared to single fracture case due to higher net pressure, and longer impacted section along the casing. Combined with the interpretation of DAS, this approach can identify the number and locations of the fractures that intersect the far field monitor well.
更多查看译文
AI 理解论文
溯源树
样例
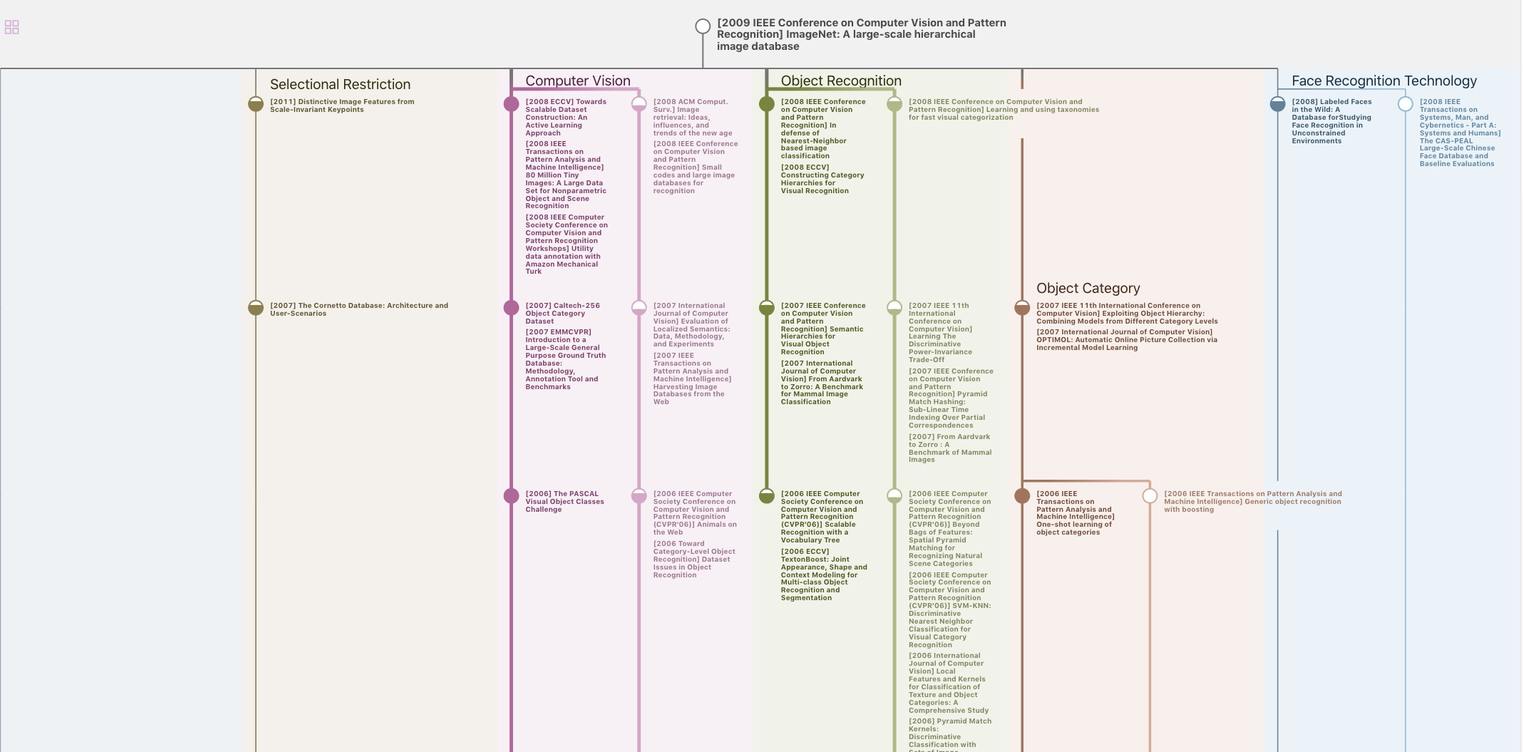
生成溯源树,研究论文发展脉络
Chat Paper
正在生成论文摘要