Effect of multiple cavities and tip injection on the aerothermal characteristics of the squealer tip in turbine stage
Applied Thermal Engineering(2023)
摘要
For modern gas turbines, the blades of the first-stage high-pressure turbines are subject to significant aerodynamic and thermal loads. As the region where the aerothermal environment is most severe, the aerothermal performance of the blade tip is crucial. Either the tip injection or squealer tip with ribs can effectively improve the tip leakage flow distribution, and thus reduce the tip thermal loads, while the effect of the combination of the two remains to be explored, especially when the number of ribs increases. To further understand the combined effects of the rib number and the tip injections on the aerothermal characteristics, steady-state numerical simulations of the first stage turbine aerothermal field are carried out with varied rib numbers and tip injection configurations in the current study. The k & omega; SST turbulence model was used to solve the 3D Reynolds-Averaged Navier-Stokes (RANS) equations. The heat transfer coefficient distributions and the leakage flow rate distributions are compared with those of the conventional squealer tip case. The results show that adding a rib inside the tip cavity would reduce the size of the reflux vortex near the leading edge of the blade (LE), and effectively reduce the averaged heat transfer coefficient on the tip. In addition, an increase in the rib number would make the coolant accumulate in the cavities, thus increasing the cooling performance. The averaged heat transfer coefficient of the coolant injected squealer tip with three ribs (Rib3C) decreases by 19.55%, compared with the performance of the conventional squealer tip, due to the combined action of adding the multiple ribs and the coolant injection. Comprehensively considering both improving the aerodynamic performance and reducing the blade tip heat load using TOPSIS analysis, the coolant injected squealer tip with two ribs (Rib2C) achieves the best overall performance. In general, ribs arranged in the upstream region of the blade would improve the coolant coverage by blocking the separation region at the cavity bottom. To improve the harsh tip thermal environment and reduce the tip aerodynamic loss, optimizing the rib layout inside the cavity and the coolant injection configurations is a practical solution.
更多查看译文
关键词
Gas turbine,Squealer tip,Rib,Tip injection,Heat transfer,Numerical simulation,Multiple cavities
AI 理解论文
溯源树
样例
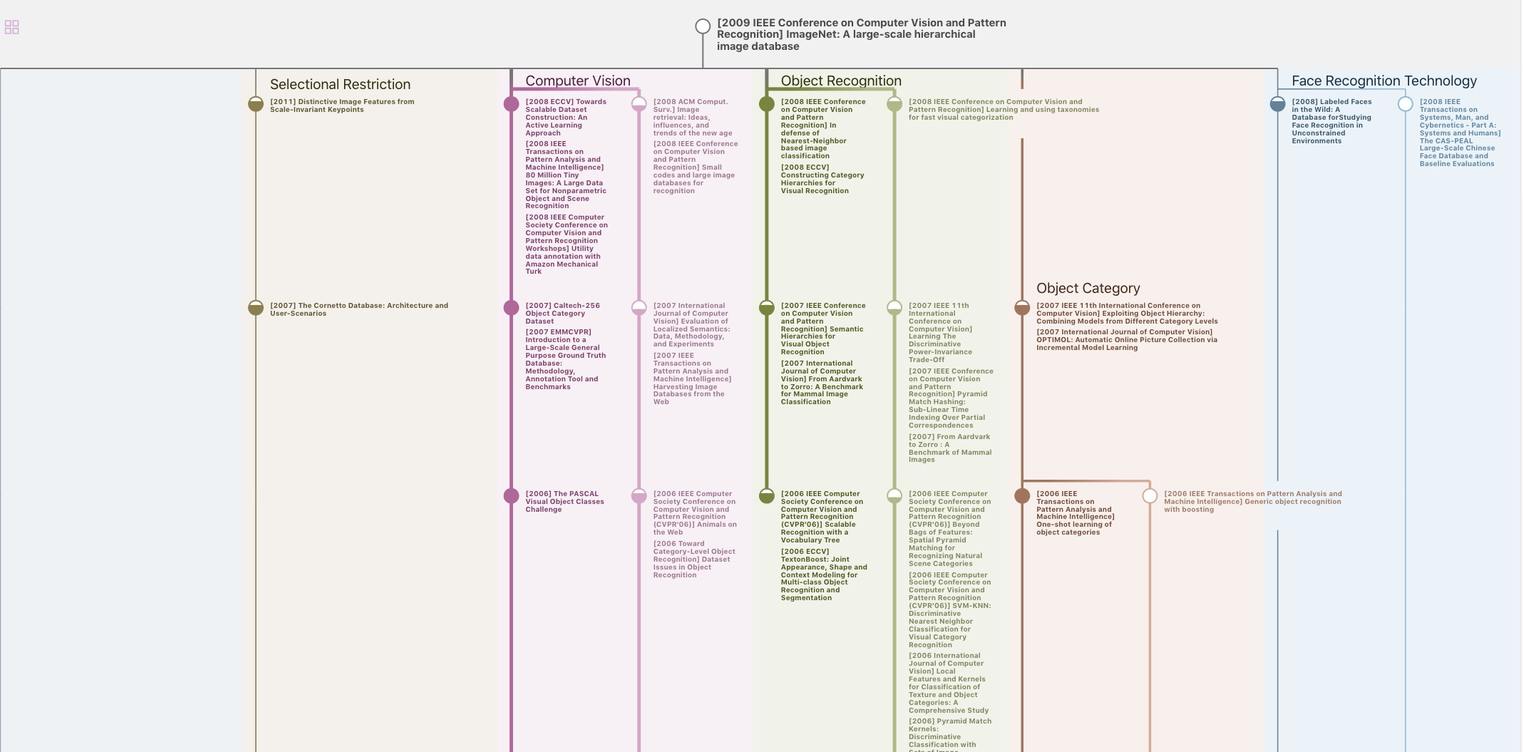
生成溯源树,研究论文发展脉络
Chat Paper
正在生成论文摘要