Multi-Objective Optimization of Predicted Magnetic Properties From Multifield Processing Conditions in Polymer Matrix Particle Composites
ASME 2022 Conference on Smart Materials, Adaptive Structures and Intelligent Systems(2022)
摘要
Abstract Additive manufacturing, no longer reserved exclusively for prototyping components, can create parts with complex geometries and locally tailored properties. For example, multiple homogenous material sources can be used in different regions of a print or be mixed during printing to define properties locally. Additionally, heterogeneous composites provide an opportunity for another level of tuning properties through processing. For example, within particulate-filled polymer matrix composites before curing, the presence of an applied electric and/or magnetic fields can reorient filler particles and form hierarchical structures depending on the fields applied. Control of particle organization is important because effective material properties are highly dependent on the distribution of filler material within composites once cured. While previous work in homogenization and effective medium theories have determined properties based upon ideal analytic distributions of particle orientations and spatial location, this work expands upon these methods generating discrete distributions from quasi-Monte Carlo simulations of the electromagnetic processing event. Results of simulations provide predicted microarchitectures from which effective properties are determined via computational homogenization. These particle dynamics simulations account for dielectric and magnetic forces and torques in addition to hydrodynamic forces and hard particle separation. As such, the distributions generated are processing field dependent. The effective properties for a composite represented by this distribution are determined via computational homogenization using finite element analysis (FEA). This provides a path from constituents, through processing parameters to effective material properties. In this work, we use these simulations in conjunction with a multi-objective optimization scheme to resolve the relationships between processing conditions and effective properties, to inform field-assisted additive manufacturing processes. The constituent set providing the largest range of properties can be found using optimization techniques applied to the aforementioned simulation framework. This key information provides a recipe for tailoring properties for additive manufacturing design and production. For example, our simulation results show that stiffness for a 10% filler volume fraction can increase by 34% when aligned by an electric field as compared to a randomly distributed composite. The stiffness of this aligned sample is also 29% higher in the direction of the alignment than perpendicular to it, which only differs by 5% from the random case [1]. Understanding this behavior and accurately predicting composite properties is key to producing field processed composites and prints. Material property predictions compare favorably to effective medium theory and experimentation with trends in elastic and magnetic effective properties demonstrating the same anisotropic behavior as a result of applied field processing. This work will address the high computational expense of physics simulation based objective functions by using efficient algorithms and data structures. We will present an optimization framework using nested gradient searches for micro barium hexaferrite particles in a PDMS matrix, optimizing on composite magnetization to determine the volume fraction of filler that will provide the largest range of properties by varying the applied electric and magnetic fields.
更多查看译文
AI 理解论文
溯源树
样例
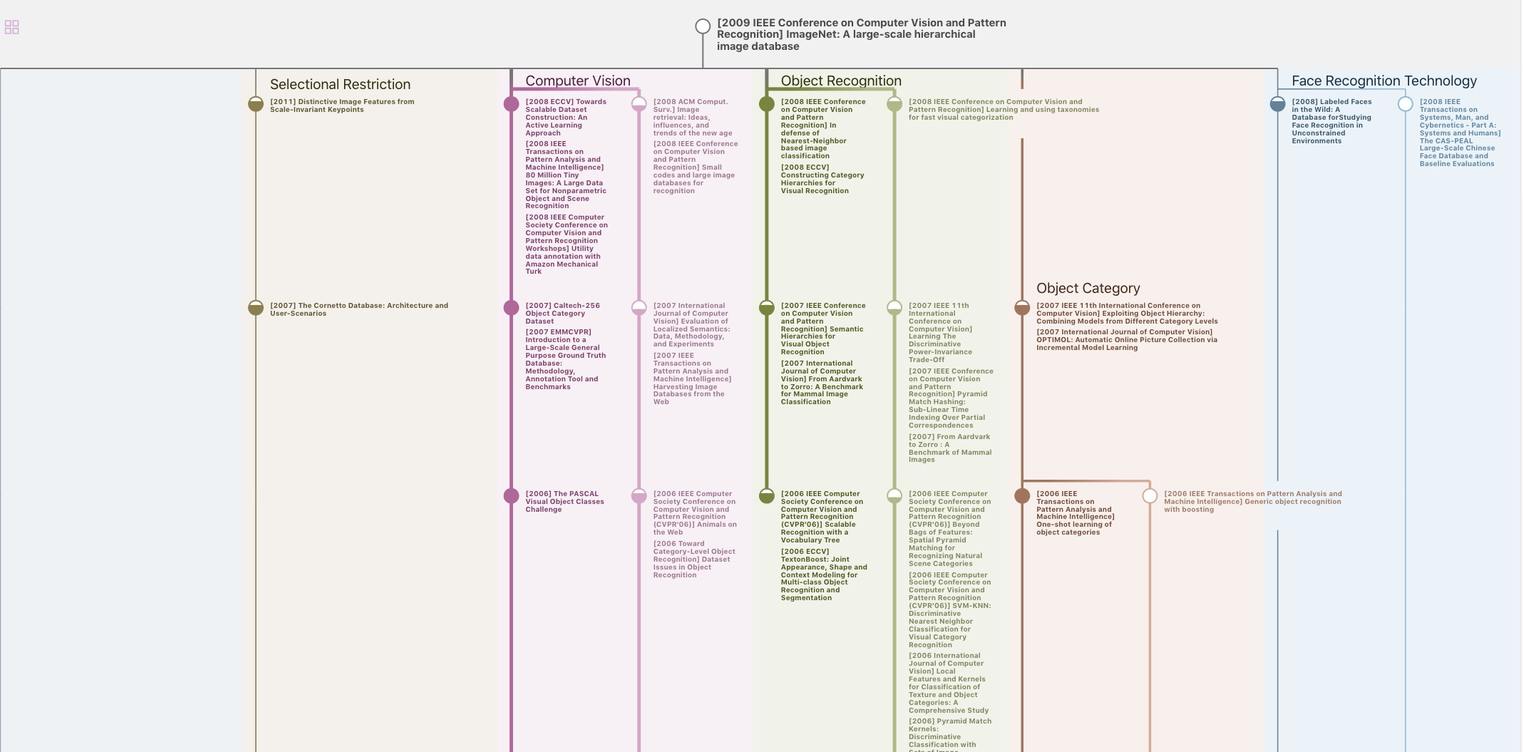
生成溯源树,研究论文发展脉络
Chat Paper
正在生成论文摘要