Winding Layout Considerations for Variable-Pole Induction Motors in Electric Vehicles
IEEE TRANSACTIONS ON TRANSPORTATION ELECTRIFICATION(2023)
摘要
Winding layout plays a crucial role in enabling variable-pole operation in an induction machine (IM). Several winding design alternatives, which consist of toroidal and distributed single- and double-layer windings, have been shown to increase speed range and improve partial load efficiency in traction applications. These windings have different pole-changing capability, end-winding length, leakage, harmonic content, and inv erter requirements. This article compares these winding alternatives with a generalized variable-pole machine design framework that captures the impact of winding selection on key performance metrics such as losses, volume, and torque-speed envelop. This framework shows that the core aspect ratio, defined as ratio of stack length to rotor diameter, selected to minimize losses depends on whether a distributed or toroidal winding is used. When a toroidally wound IM is designed with a low aspect ratio, it can provide the largest torque-speed envelop with highest efficiency over a wide speed range. An experimental toroidally wound IM driven by an 18-leg converter is used to validate the design framework. The experimental setup is configured externally to emulate a single-layer winding and to show benefits gained from the extra pole-changing flexibility of a toroidal winding.
更多查看译文
关键词
Electric vehicles (EVs),induction machine (IM),motor design,motor windings,multiphase drives,pole changing,traction
AI 理解论文
溯源树
样例
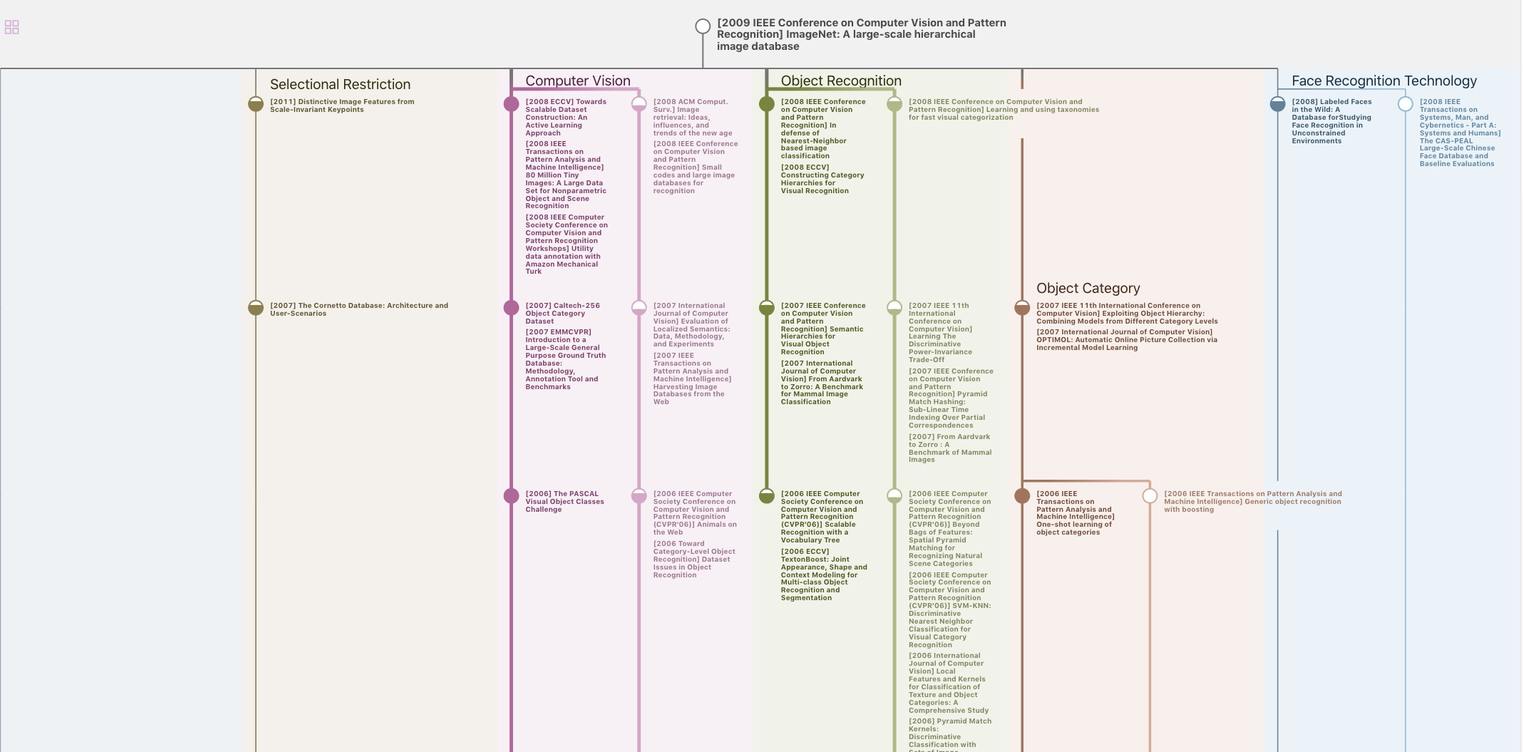
生成溯源树,研究论文发展脉络
Chat Paper
正在生成论文摘要