Unsteady Simulation and Analysis of Energy Loss Mechanism of a Vertical Volute Pump Under Stall Conditions
Journal of Fluids Engineering(2023)
摘要
This study comprehensively investigates the flow features and energy loss mechanisms under stall conditions based on computational fluid dynamics (CFD) and hydraulic loss visualization techniques. The three-dimensional unsteady Reynolds-averaged Navier- Stokes (URANS) equations were solved using the shear stress transport (SST) k-omega turbulence model. Furthermore, the entire flow domain of the vertical volute pump was considered to capture the boundary flow behavior accurately. The results illustrate that the critical stall condition occurs at 0.7Q(d), where the H-Q curve exhibits a positive slope, and the deep stall condition occurs at 0.65Q(d). The growth rate of energy loss from critical stall to deep stall is 182.2%. In the stall condition, a secondary vortex appears at the impeller inlet. A high energy loss occurs at the suction side and trailing edge in the impeller caused by the reduction in the effective inflow area. The energy loss in the blade suction side guide vane is primarily due to the friction loss under the critical stall condition. By contrast, under the deep stall condition, the energy loss in the outlet of the guide vane is mainly the impact loss from the volute of the rear gunner. The impact effect can result in high energy losses near the volute tongue. The entropy production analysis demonstrates that the hydraulic losses in the diffuser are literately greater than that in the impeller and inlet pipe. Hence, optimization of such components can be taken into consideration in future works for performance improvement.
更多查看译文
关键词
pump,computational fluid dynamics,hydraulic analysis,loss visualization
AI 理解论文
溯源树
样例
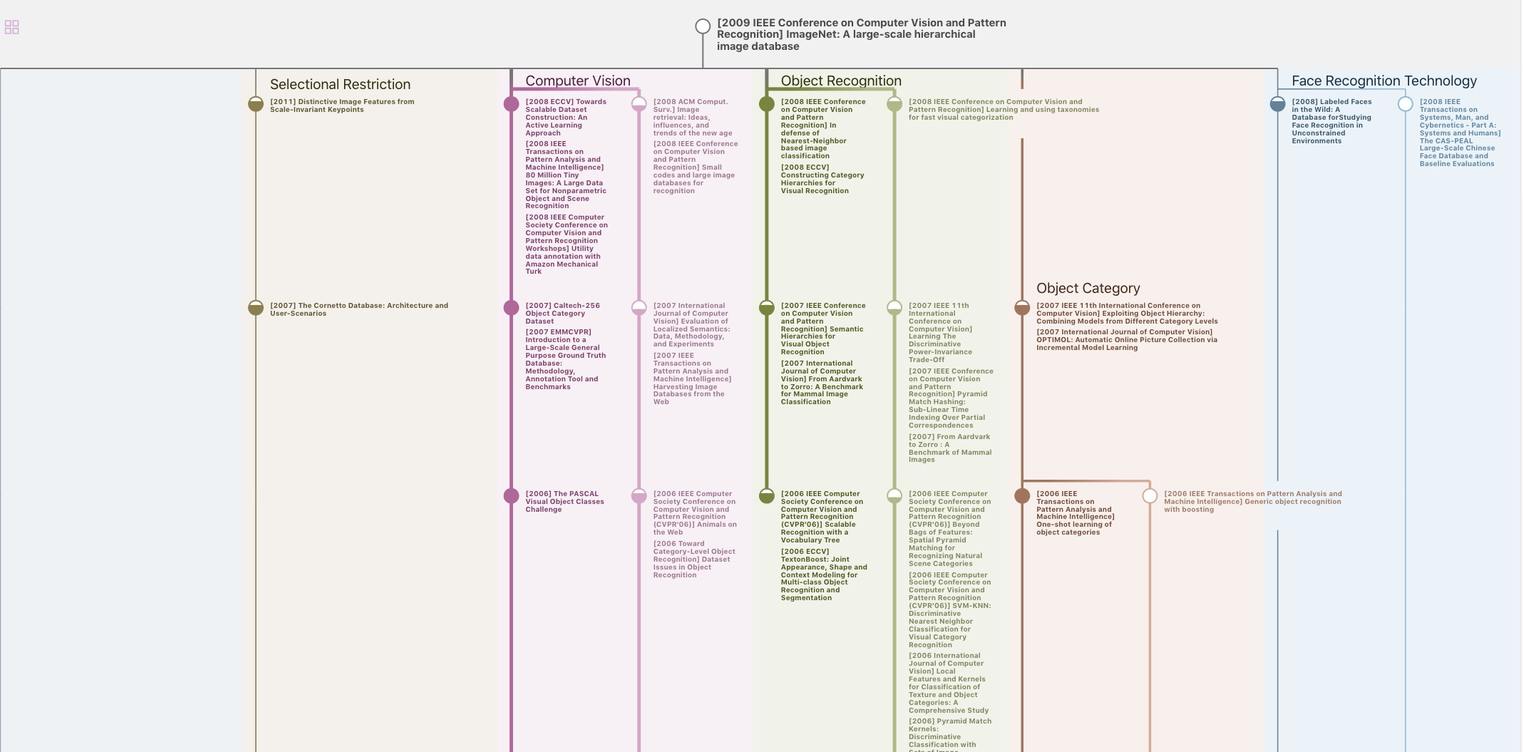
生成溯源树,研究论文发展脉络
Chat Paper
正在生成论文摘要