Multiaxial fatigue of additively manufactured metallic components: A review of the failure mechanisms and fatigue life prediction methodologies
PROGRESS IN MATERIALS SCIENCE(2023)
摘要
Additive manufacturing techniques offer significant advantages over conventional manufacturing methods. These include the possibility of realizing highly customized components in which not only can the geometry be defined with a high degree of freedom, but the material composition or geometrical properties can also be manipulated throughout the component by introducing lattice structure zones. Such variations cannot be realized using conventional manufacturing techniques. However, the application of additively manufactured parts at the industrial scale is still limited owing to the high variability in mechanical properties, which also makes it difficult to define feasible tools to assess their structural integrity and determine their expected fatigue life with a sufficient degree of reliability. In addition, real components often experience multiaxial stresses at critical locations owing to their geometry or service-loading conditions. Thus, a proper under-standing of the fatigue performance of additively manufactured components with complex ge-ometries cannot neglect the consideration of multiaxial stress states. This review presents an overview of multiaxial fatigue in additively manufactured metallic components, providing in-sights into crack initiation sites and growth orientations and relating them to the fatigue failure mechanisms in these components. The principal life prediction methodologies applied for the fatigue damage assessment of additively manufactured components under multiaxial fatigue loading are presented, with a particular focus on their accuracy in correlating fatigue data ob-tained for different loading conditions.
更多查看译文
关键词
Additive manufacturing, Multiaxial fatigue, Fatigue damage assessment, Crack initiation, Crack growth, Life predictions
AI 理解论文
溯源树
样例
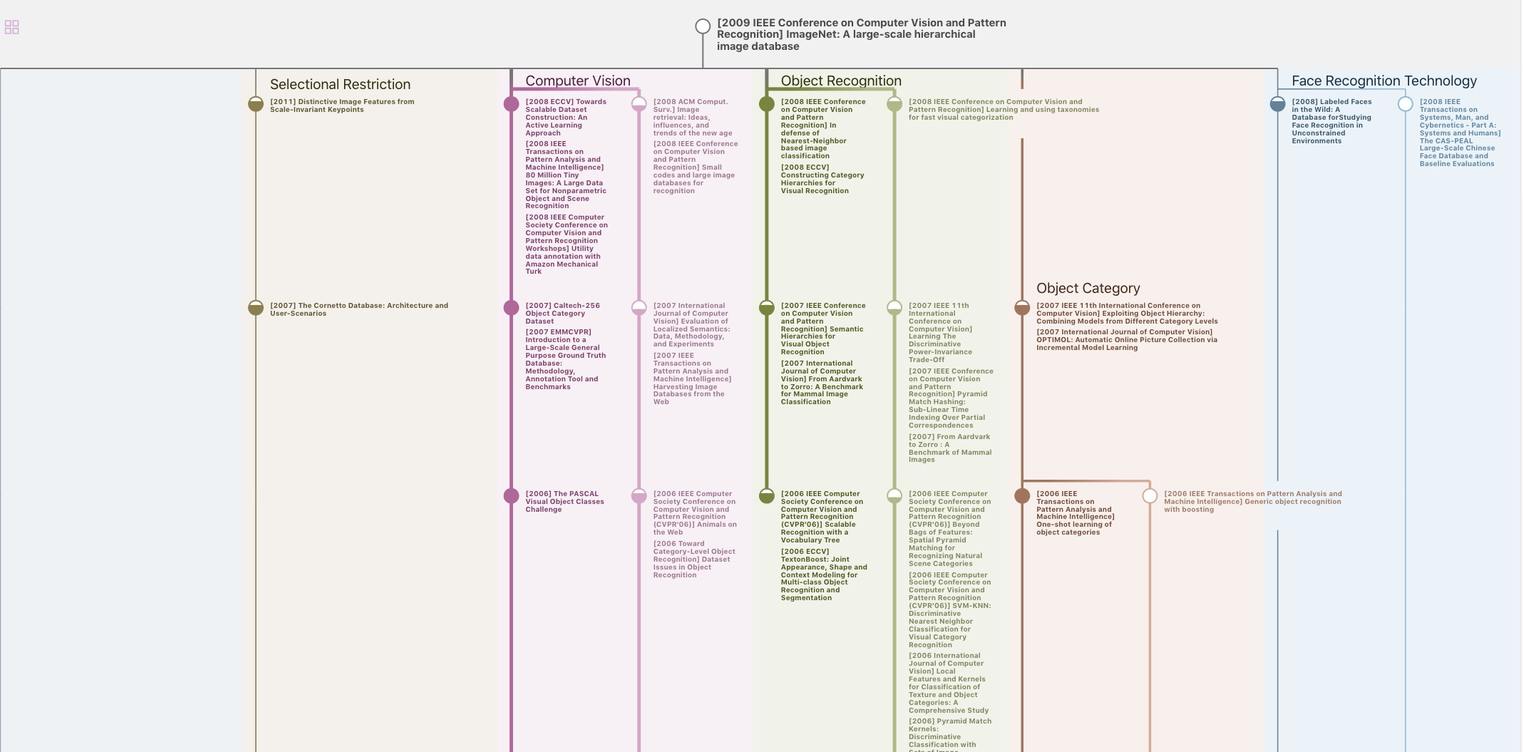
生成溯源树,研究论文发展脉络
Chat Paper
正在生成论文摘要