Combination of topology and shape optimization with finite element modeling in the case of an aerospace component produced by laser based additive manufacturing
JOURNAL OF LASER APPLICATIONS(2023)
摘要
The present work applies a design for additive manufacturing-driven design methodology to an aeronautical component to be fabricated through an additive manufacturing (AM) process. This involves simulation of the process using Abaqus Finite Element software as well as the development of a design methodology concerning topology and shape optimization utilizing SIMULIA Tosca. A benchmarking AM simulation is performed first to provide validation and general guidelines needed to properly implement a low-resolution AM simulation in Abaqus. The structural optimization is started by volume minimization topology optimization. Solid isotropic material with penalization fails to achieve convergence with frequency response constraints, while mass interpolation material penalization converges to a well-connected design. The design interpretation with polyNURBs results in a single component with a weight reduction of 2.29% compared to current two component assemblies. Further implementation of shape optimization to address stress design requirements allows achieving stress homogeneity and a lower weight, resulting in a 5.12% weight reduction. The AM simulation process is applied to a scaled version of the final design to both assess the printability of the part itself as well as implementation of key tools to define the AM simulation. Maximum distortion of the part appears at expected regions with an overhanging material.
更多查看译文
关键词
finite element modeling,aerospace component,optimization,finite element
AI 理解论文
溯源树
样例
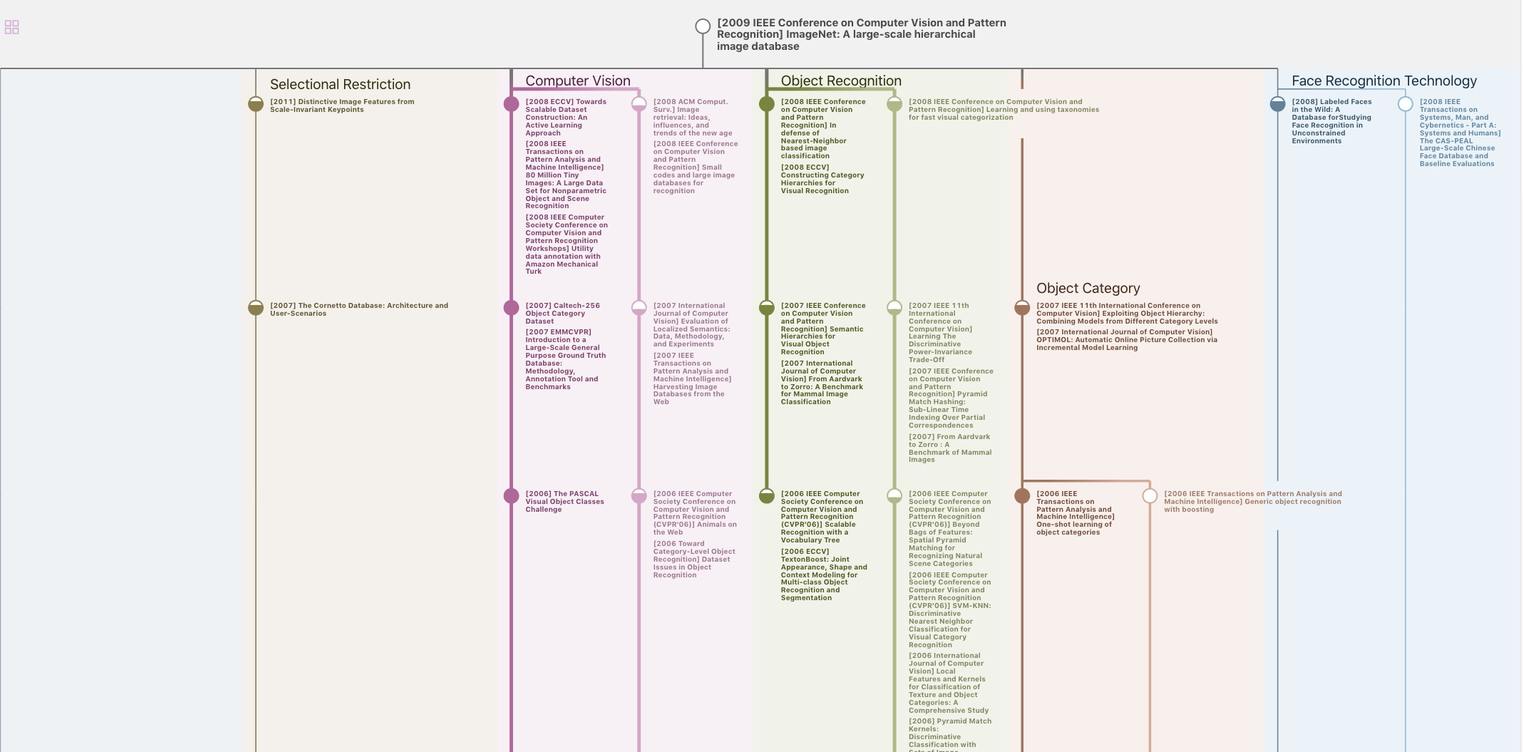
生成溯源树,研究论文发展脉络
Chat Paper
正在生成论文摘要