Influence of Scanning and Building Strategies on the Deformation Behavior of Additively Manufactured AlSi10Mg: CPFEM and Finite Element Studies
METALS AND MATERIALS INTERNATIONAL(2023)
摘要
A novel computational framework has been presented in this work for understanding the mechanical deformation behavior in additively manufactured parts. AlSi10Mg parts were additively manufactured and investigated for effects on microstructure due to changes in process parameters. The morphological characteristics of the printed parts were assessed, and 2D statistically equivalent representative volume elements (SERVEs) were created and analyzed for deformation under tension computationally with crystal plasticity finite element method (CPFEM) with a combined MATLAB and ABAQUS interactive framework. For assessing the CPFEM parameters, an interactive ABAQUS and MATLAB environment was implemented using MATLAB’s genetic algorithm (GA) toolbox. Various results like von Mises stress distribution, maximum in-plane stress distribution, and L 2 -norm of Green Lagrange’s strain were compared, and it was found that the vulnerability of the structures is related to the change in process or build parameters. CPFEM analyses on 3D microstructures generated through DREAM. 3D further confirmed the validity of results for CPFEM in 2D. The developed 2D framework also predicted the texture that correlated well with the tension test findings. Parallely, a finite element framework was developed to study the localization effects on AM specimens due to the presence of pores. This work has reported two separate viewpoints in terms of porosity and microstructure. Graphical Abstract
更多查看译文
关键词
additive manufacturing,AlSi10Mg,statistical microstructure,crystal plasticity,localization behavior,porosity studies
AI 理解论文
溯源树
样例
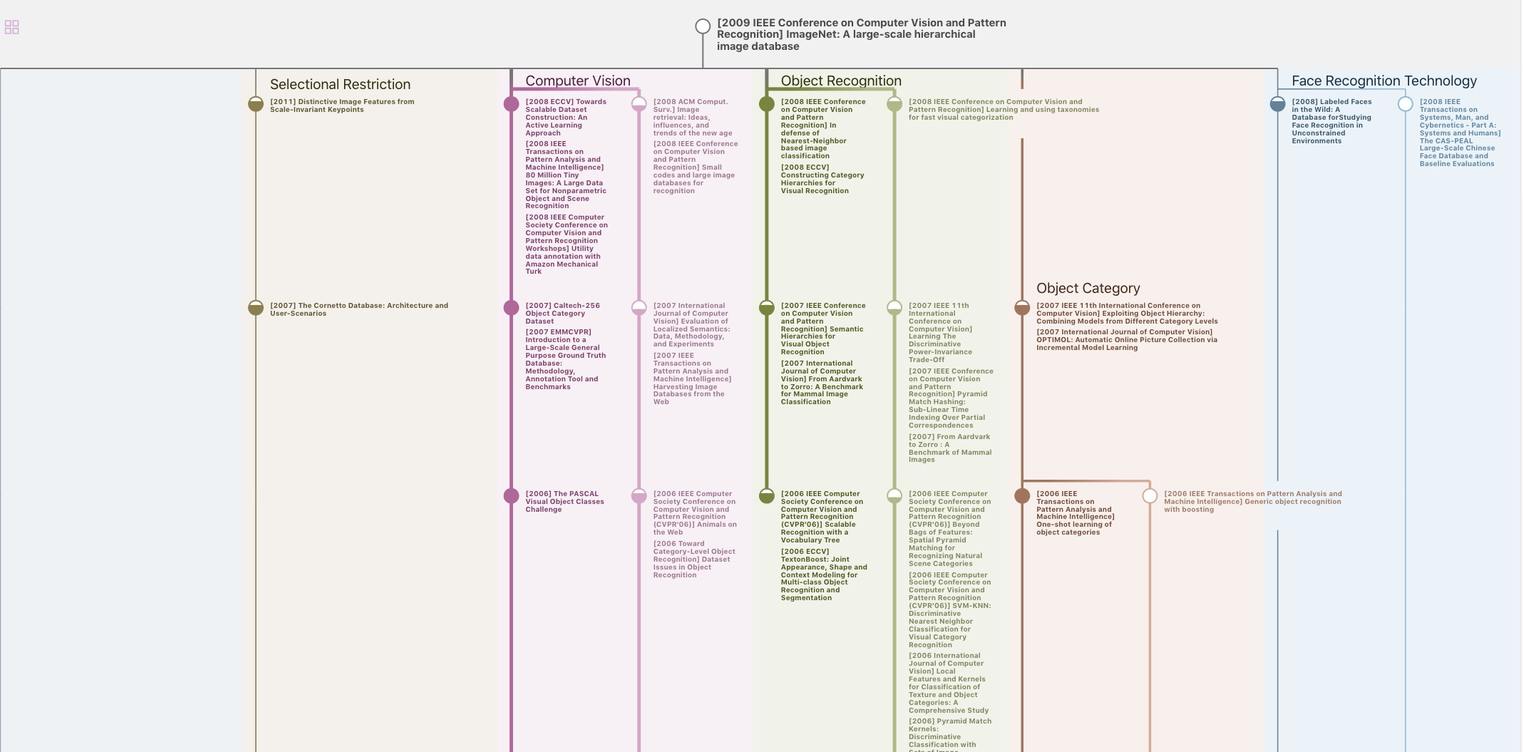
生成溯源树,研究论文发展脉络
Chat Paper
正在生成论文摘要