Experimentation with the EDM parameter through a full factorial technique and optimization using regression analysis with carbon nanotubes
INTERNATIONAL JOURNAL OF INTERACTIVE DESIGN AND MANUFACTURING - IJIDEM(2023)
摘要
Using an unconventional method of machining, electric discharge machining is capable of processing extremely hard materials that are inaccessible to more traditional machining methods. Electric discharge machining is a metalworking technique that uses an electric erosion effect in conjunction with an electrosparking spark. A current discharge takes place in a narrow space between the work piece and the electrode, melting and vaporizing the unwanted material and separating it from the parent metal in the process. When it comes to enhancing material removal rates and decreasing tool wear, powder-mixed electrical discharge machining is one of the most recent techniques. The machining mechanism, the cost-effectiveness of powder, the powder concentration in the working fluid, and the safety and environmental impact of this new development are just a few of the many questions that remain unanswered. As a result, it sees very little use in the manufacturing sector. EN-31 with aluminium as a tool electrode was examined in this study to determine its machining characteristics during EDM processing. The EDM procedure is used to study the MRR, TWR, and SR of the MWCNT combined with dielectric fluids. EDM process output parameters were predicted using regression models. Predictive models were built using the peak current, pulse on time, and pulse off time parameters of machining. In order to collect data, we used a full factorial design. ANOVA is used to identify the most influential input parameter that has the greatest impact on the final outcome. Using design expert software, the characteristics of EN-31 steel were improved and regression equations with and without MWCNT were compared using an electro-destructive method (EDM). Carbon nano tube combined as dielectric fluid improved surface roughness by an average of 30% while improving MRR by an average of 19% while decreasing TWR by 8.51 percent.
更多查看译文
关键词
Powder mix EDM,TWR,MRR,Surface roughness,Multi wall carbon nanotubes (MWCNT),Parameter optimization
AI 理解论文
溯源树
样例
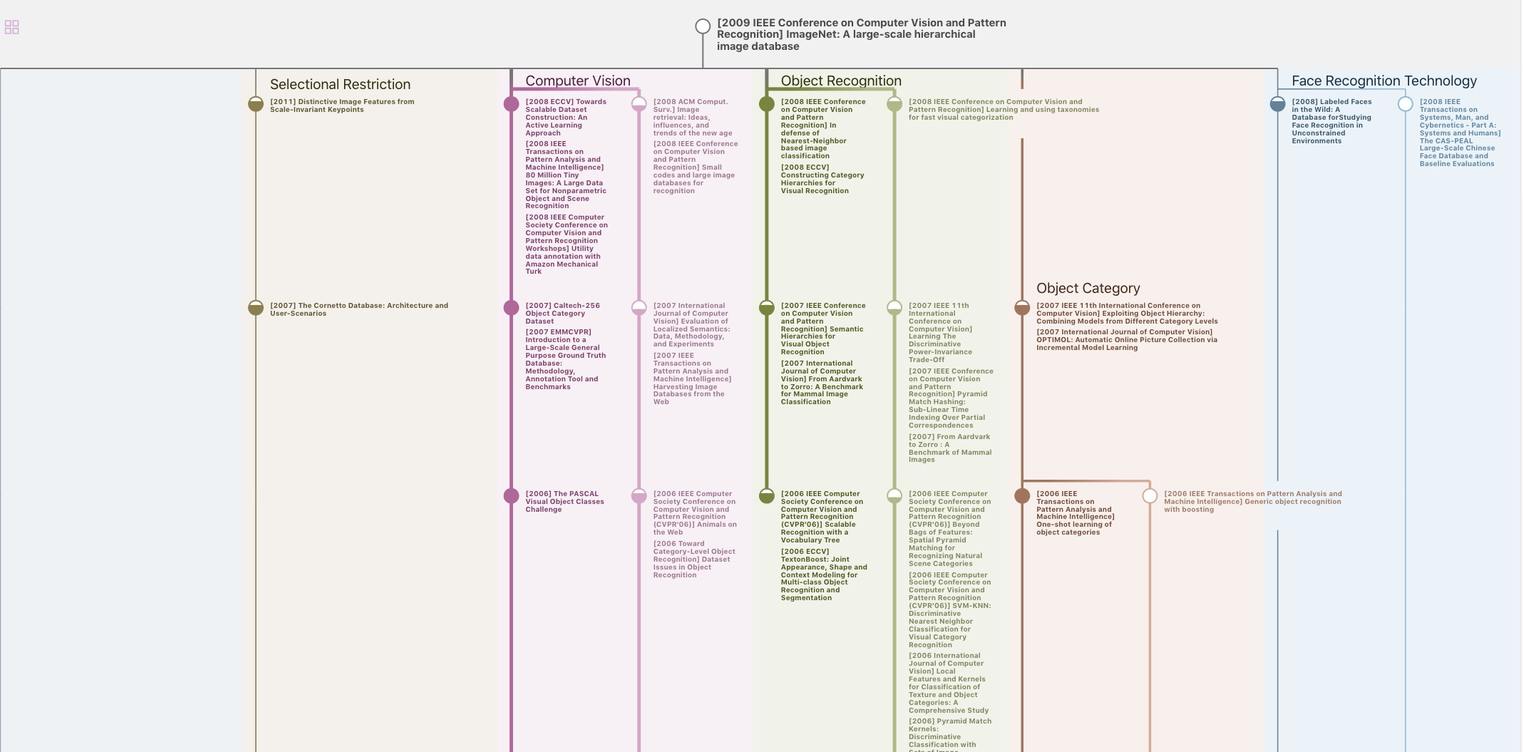
生成溯源树,研究论文发展脉络
Chat Paper
正在生成论文摘要