An Improved Combined Framework of Force Measurement With Friction Model for Harmonic Gear
IEEE Sensors Journal(2023)
摘要
To obtain accurate output torque of robot joint for torque control, a built-in torque sensor is designed in this article. To enhance the performance of harmonic gear (HG), it is urgent to deal with the key issues in terms of the errors of sensing and positioning, and torque ripple interference. To handle these aforementioned key issues, four pairs of symmetrically distributed strain gauges are pasted on the bottom of the flexspline. Then, a precise positioning method based on laser marking is proposed to improve the positioning accuracy of the strain gauges. Moreover, Kalman filter (KF) is utilized to reduce torque ripple interference in the output signal of the strain gauges. Additionally, the designed device is evaluated by experimental tests which are conducted on prototype trial production. Synchronously, the relationship between the flexspline torque and the joint output torque is verified and the polynomial is used to represent the relationship of the measured torque for the built-in torque sensor and the standard torque sensor in the static and dynamic conditions. Finally, a friction model is presented and identified. Comprehensive comparative experiments is performed the performance of the build-in torque sensor in terms of estimation accuracy and control and it shows that the designed built-in torque sensor with friction compensation (FC) can be improved ten times in comparison with that of without FC in terms of steady-state mean error and mean value of measurement error. What is more, this designed build-in torque sensor holds tremendous potential for making the compact and lightweight motion joint module, especially for cooperative robot and robotic supernumerary limb.
更多查看译文
关键词
Built-in torque sensor,harmonic drive,Stribeck friction model,torque control
AI 理解论文
溯源树
样例
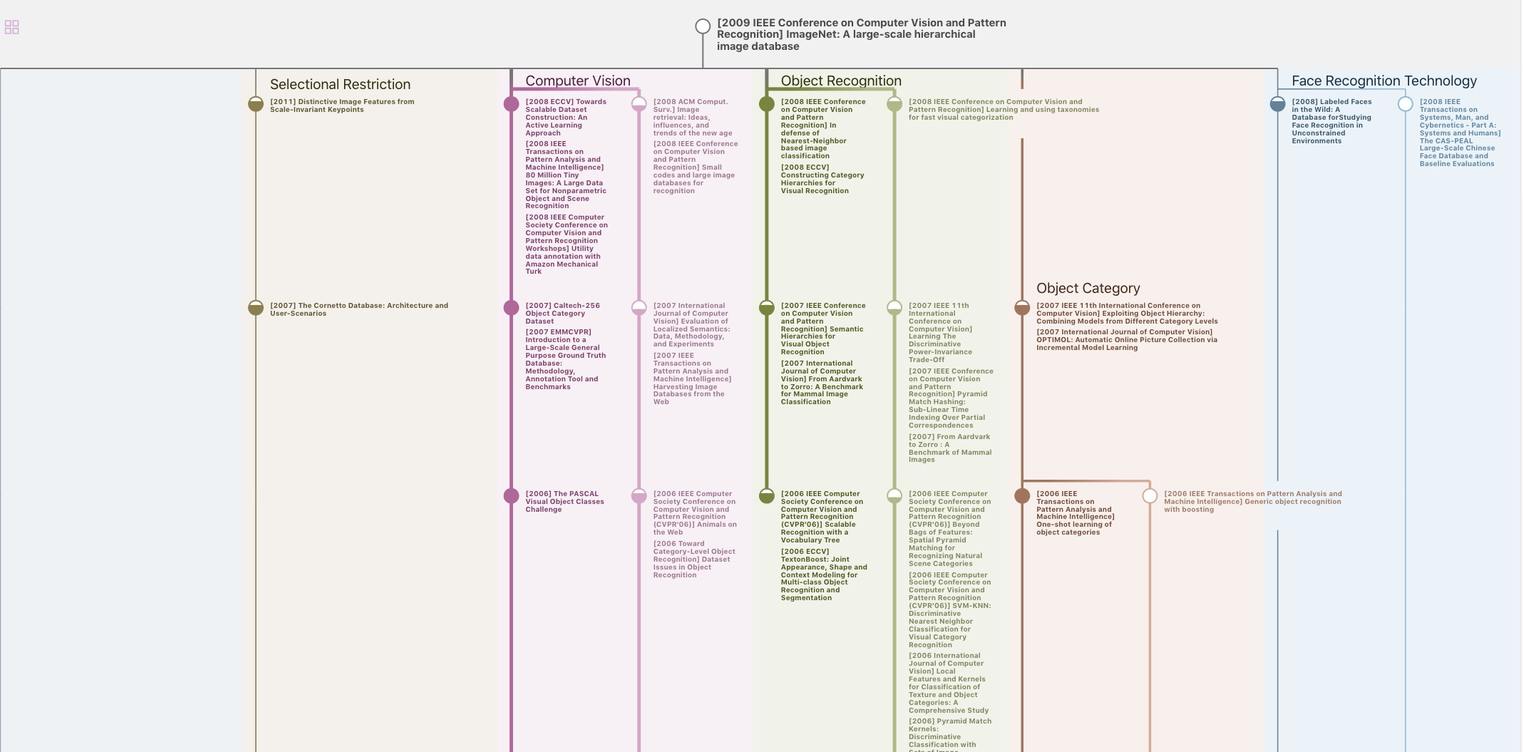
生成溯源树,研究论文发展脉络
Chat Paper
正在生成论文摘要