Convexity and Surface Quality Enhanced Curved Slicing for Support-Free Multi-Axis Fabrication
JOURNAL OF MANUFACTURING AND MATERIALS PROCESSING(2023)
摘要
In multi-axis fused deposition modeling (FDM) printing systems, support-free curved layer fabrication is realized by continuous transition of the printer nozzle orientation. However, the ability to print 3D models with complex geometric (e.g., high overhang) and topological (e.g., high genus) features is often restricted by various manufacturability constraints inherent to a curved layer design process. The crux in a multi-axis printing process planning pipeline is to design feasible curved layers and their tool paths that will satisfy both the support-free condition and other manufacturability constraints (e.g., collision-free). In this paper, we propose a volumetric curved layer decomposition method that strives to not only minimize (if not prevent) collision-inducing local shape features of layers, but also enable adaptive layer thickness to comply with a new volumetric error-based surface quality criterion. Our method computes an optimal Radial Basis Functions (RBF) field to modify the fabrication sequence field, from which, the iso-surface layers are extracted to design the corresponding multi-axis printing tool paths. A method to fine-tune variable nozzle orientations on each resulting curved layer is then proposed to overcome possible collisions in high-genus geometries. To validate the concept and exhibit its potential, several support-free fabrication experiments and comparisons with the conventional geodesic field-based slicing are presented, and the results give a preliminary confirmation of the feasibility and advantages of the proposed method.
更多查看译文
关键词
multi-axis additive manufacturing,support-free 3D printing,radial basis functions (RBF),weighted distance field,non-planar 3D printing
AI 理解论文
溯源树
样例
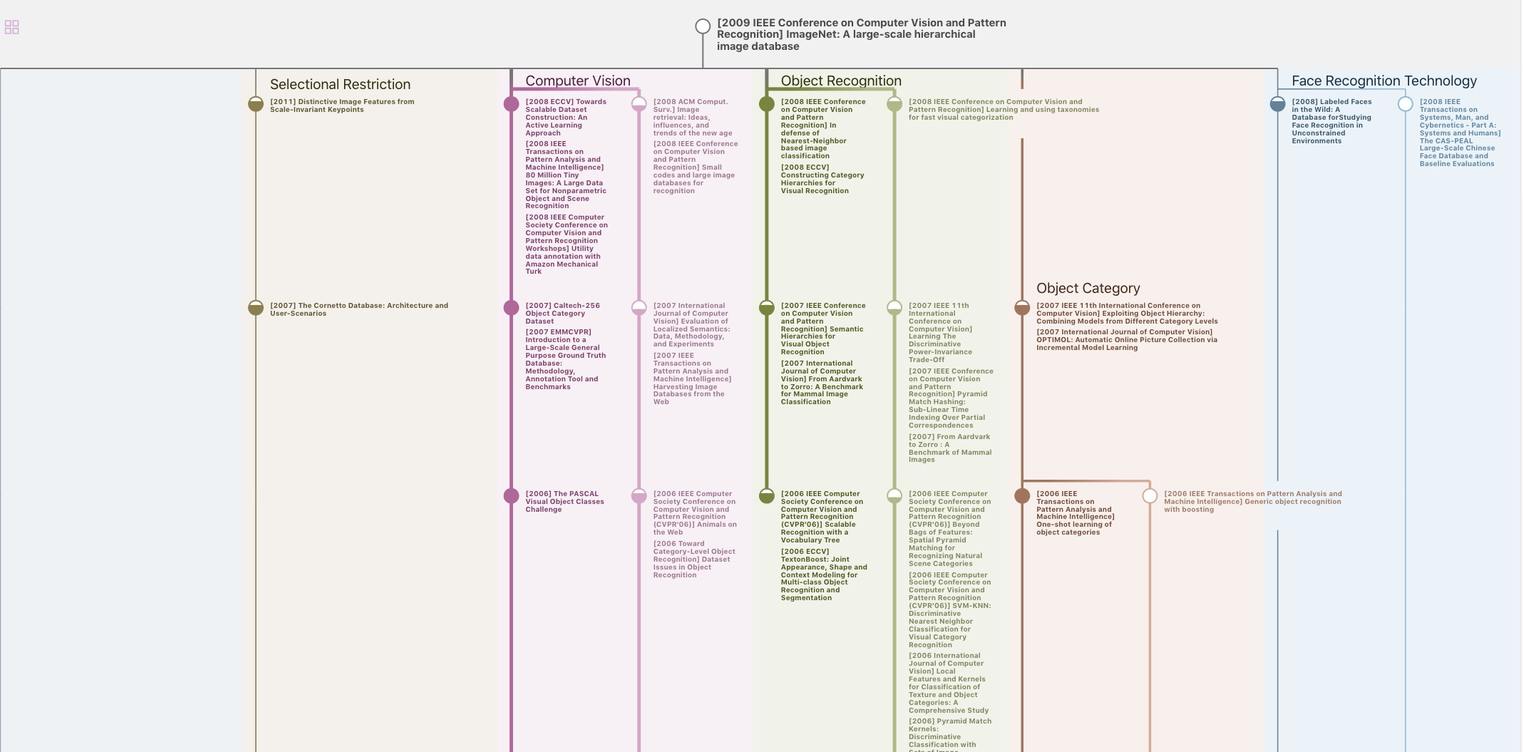
生成溯源树,研究论文发展脉络
Chat Paper
正在生成论文摘要