Comparison of the surface morphologies of ceramic reinforced metal matrix composite cams after wear tests under dry and wet conditions
JOURNAL OF COMPOSITE MATERIALS(2023)
摘要
The integral engine parts, such as camshaft members, are usually not preferably made of ceramic-reinforced MMC because the margin of compromise on the engine performance is small. However, the lightweight and wear-resistant nature of the mentioned materials can benefit fuel consumption without necessarily compromising engine performance. In this study, Al (AA2124) matrix is reinforced with ceramic particles of two different types (SiC, B4C), size distributions (B4C: 1-7, SiC: 2 and 20 mu m), and volume fractions (0, 10, 20, 30 vol.%) to manufacture camshaft cams (lobes). While MMC cams are manufactured by powder metallurgy (300 MPa, 615 degrees C, 30 minutes), spherical graphite cast iron (GGG40) cams are prepared by casting, induction hardening, and machining. The wear behavior of MMC cams is compared with the reference unreinforced AA2124 and conventionally used cast iron cams under dry and virtually created engine-like wet conditions. It was attempted to correlate the percentage increase in the roughness and weight loss with the structure of the cams using SEM, EDX, and macroscopy analysis. Results showed that the initiation of a three-body abrasive wear mechanism for 30 vol.% of the larger SiC particles caused lower wear resistance in the cams under dry conditions. As for the wet conditions, although the cams' wear resistance increased with increasing ceramic particles' content, it resulted in enhanced wear in the counterface when larger ceramic particles were used as reinforcement. Overall, higher ceramic content and larger particle size encourage three-body abrasive wear between the interacting surfaces and assist in degraded wear resistance under wet conditions.
更多查看译文
关键词
Metal matrix composites,camshafts,tribology,powder metallurgy,cam materials
AI 理解论文
溯源树
样例
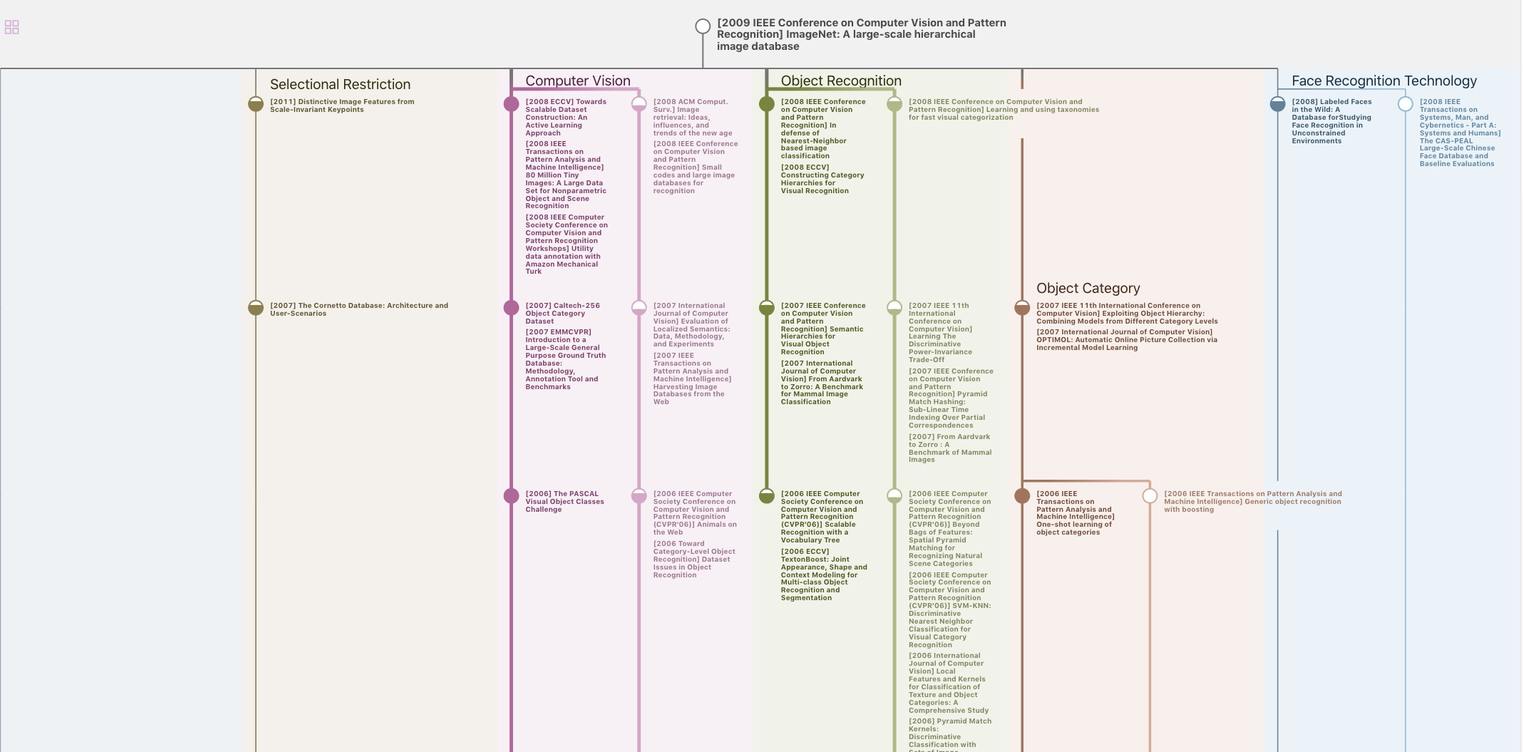
生成溯源树,研究论文发展脉络
Chat Paper
正在生成论文摘要