Investigation of forming defects in 5A06 aluminum alloy cold stamping of thin-walled shell with corner
INTERNATIONAL JOURNAL OF ADVANCED MANUFACTURING TECHNOLOGY(2023)
摘要
Aluminum alloy thin-walled shells with corner are important components of aircraft lubricating oil tank for protective. The existing process mainly adopts cold stamping combined with manual multi-pass straightening and shape correction. Due to its asymmetrical shape and corner, there are serious defects such as wrinkling and springback during stamping, which restrict the mass production of this kind of products. In this paper, the forming mechanism of defects and the influence of process parameters on it were investigated numerically and experimentally. The results demonstrated that the wrinkling concentrated on the side wall of workpiece was caused by more feeding and metal accumulation in local areas due to stress concentration. There was obvious thinning at the small diameter edge (SDE) of workpiece which can reach 10.0% locally. The springback in different areas of workpiece varied greatly. Massive positive springback occurred at the SDE and the large diameter edge (LDE), and a small amount of negative springback occurred at the top left of the workpiece due to insufficient material extension. The wrinkling and springback can be ameliorated by increasing the blank holder force (BHF) while the thinning will be aggravated. Besides, the increase of friction coefficient and die closing pressure (DCP) can also reduce the wrinkling and springback, respectively. For the workpieces in this paper, the forming defects can be greatly improved within the following process parameters: the BHF of 15 to 20 kN and the stamping speed of not less than 20 mm/s and the DCP of above 350 kN.
更多查看译文
关键词
Cold stamping,Forming defects,Aluminum alloy,Blank holder force
AI 理解论文
溯源树
样例
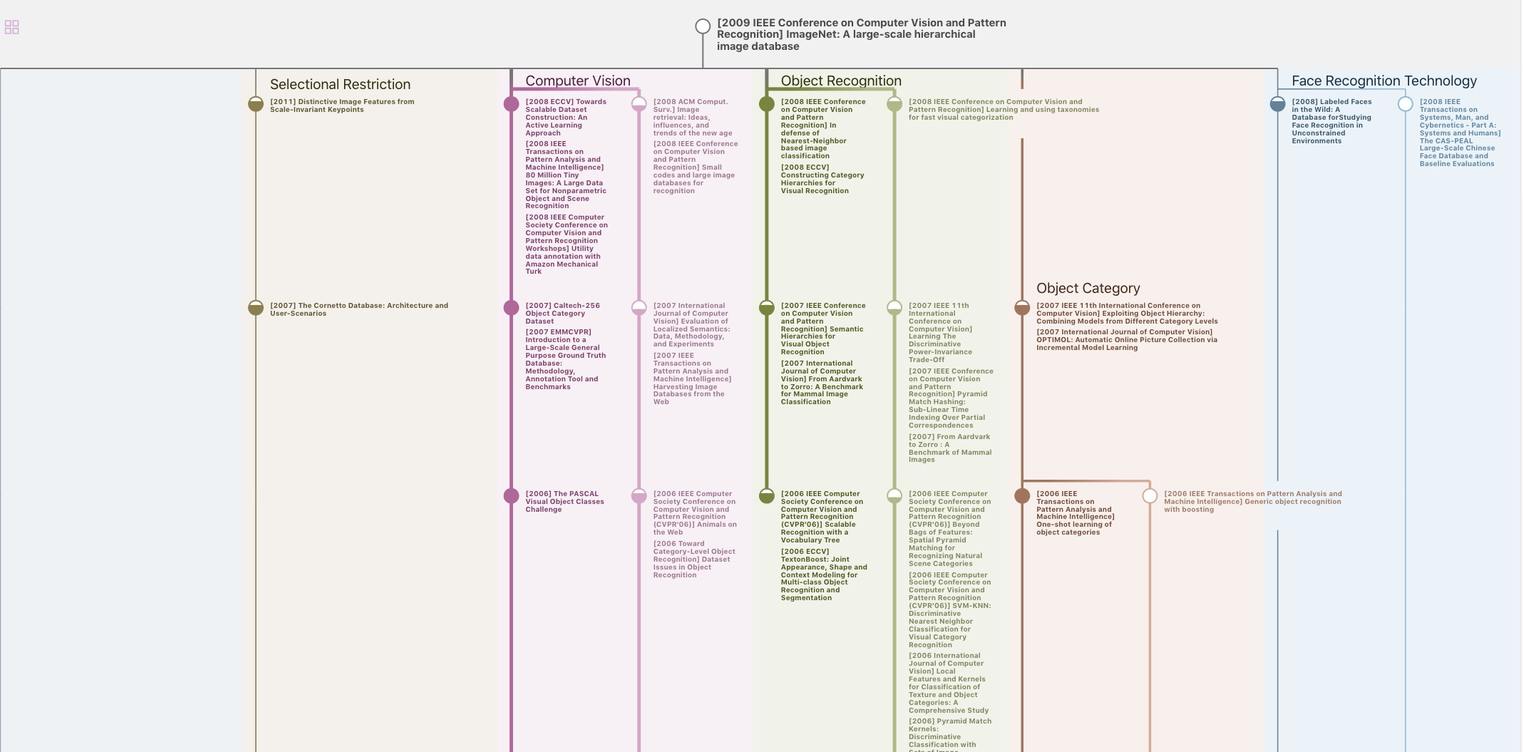
生成溯源树,研究论文发展脉络
Chat Paper
正在生成论文摘要