Establishing cutting conditions for dry drilling of aluminium alloy stack materials
PROCEEDINGS OF THE INSTITUTION OF MECHANICAL ENGINEERS PART B-JOURNAL OF ENGINEERING MANUFACTURE(2024)
摘要
Aside from their remarkable lightness, high strength and corrosion resistance, aluminium alloys have dominated aircraft manufacturing for decades. The combination of aluminium alloys 2024 and 7150 is widely used in the fabrication of airframe structures. Numerous holes must be drilled through the materials in order for them to be connected. Due to structure size and use of mobile drilling machines, lubricant oil is released during the drilling operation and either becomes airborne or accumulates on the floor. The primary motivation for dry drilling development is to avoid this oil discharge. A significant disadvantage of the drilling process for aluminium alloys is the workpiece's proclivity to stick to the cutting tool, especially when temperatures are high. This research investigated the selection of cutting conditions that enable dry drilling of stack aluminium panels. The selection of cutting parameters for experiment use was made based on the assessment of literature pertaining to drilling with carbide cutting tools. Apart from literature, the assessment of cutting parameters also took into consideration existing practices in Airbus UK. Results indicated that optimum cutting performance was achieved by drilling at higher feedrates and lower interaction time compared to existing fluid based processes. In addition, this paper outlines the aspects of energy and cutting forces in current cutting processes as well as focuses on determining optimum conditions that minimise energy input.
更多查看译文
关键词
Dry drilling,aluminium alloy,stack material,hole quality
AI 理解论文
溯源树
样例
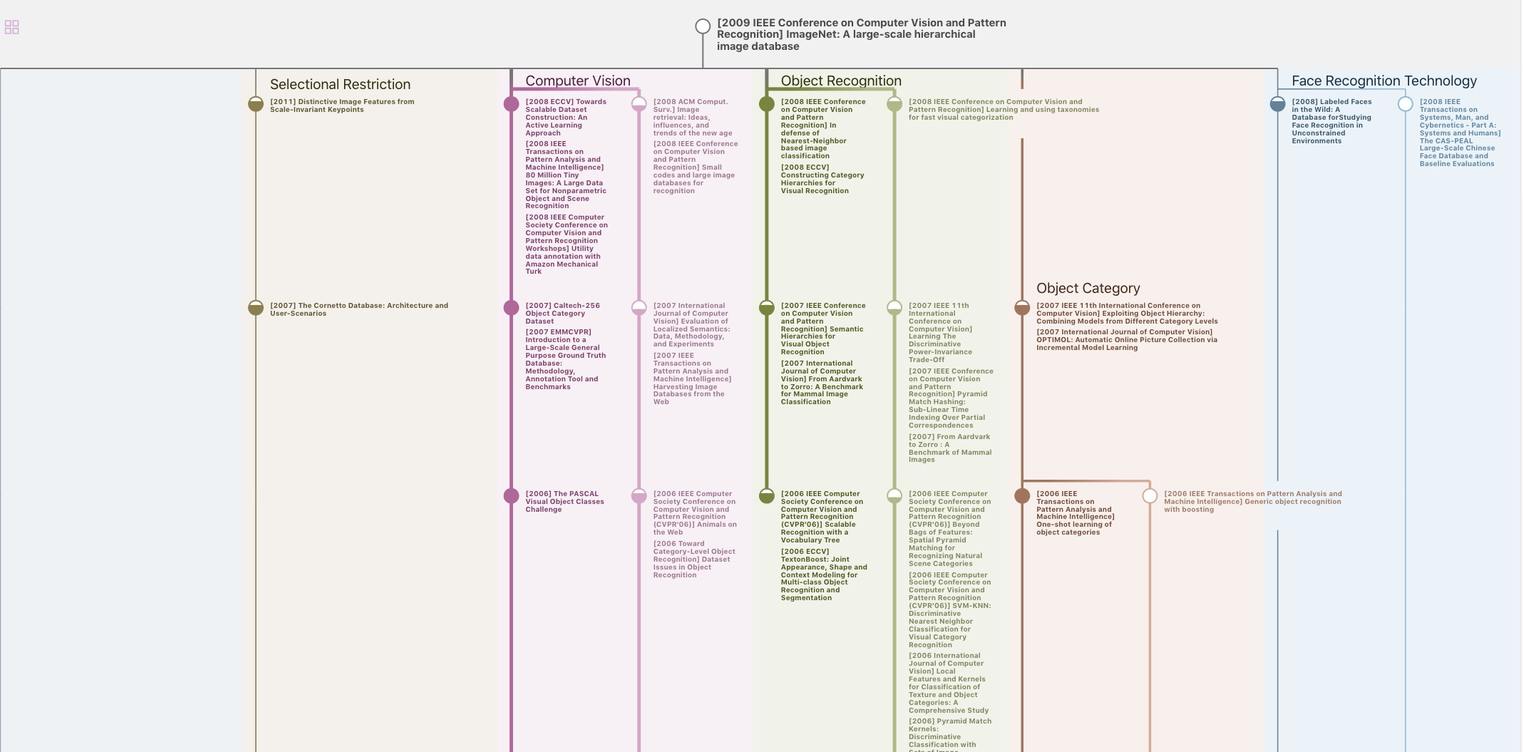
生成溯源树,研究论文发展脉络
Chat Paper
正在生成论文摘要