Effects of process parameters on friability and surface quality in the rapid investment casting process
INTERNATIONAL JOURNAL OF ADVANCED MANUFACTURING TECHNOLOGY(2022)
摘要
This research investigates surface erosion of ceramic shells in the rapid investment casting (RIC) process using a friability test and microscopy analysis. The impact of different pattern materials, shell facecoat composition, and burnout temperature is explored. Acrylonitrile butadiene styrene (ABS), polylactic acid (PLA), and polyvinyl butyral (PVB) feedstock are used to make patterns by 3D printing, while a fourth benchmark set is produced from foundry wax in a rubber mold. The patterns are made in a cylindrical shape and invested in silica-based ceramic shells. The facecoat composition is varied by the addition or the absence of stucco in the primary slurry coat. The shells are burned out at temperatures of 700, 900, and 1100 °C and used for a friability test. Additionally, a set of smaller shell samples is made for microscopic analysis of shell erosion at the pattern-ceramic interface. Results show that among 3D printing feedstock, ABS produces the most surface erosion as revealed by friability measurements and micrographs, while PVB is the least and is comparable to conventional foundry wax. The absence of stucco in the facecoat reduces friability by 25%, 35%, 55%, and 80% for ABS, PLA, PVB, and wax, respectively. Burnout temperature has a varying effect on friability depending on the pattern material. A strong link between the surface quality of castings and friability is found.
更多查看译文
关键词
Friability,Fused filament fabrication,Polyvinyl butyral,Rapid investment casting,Stucco penetration,Surface tension
AI 理解论文
溯源树
样例
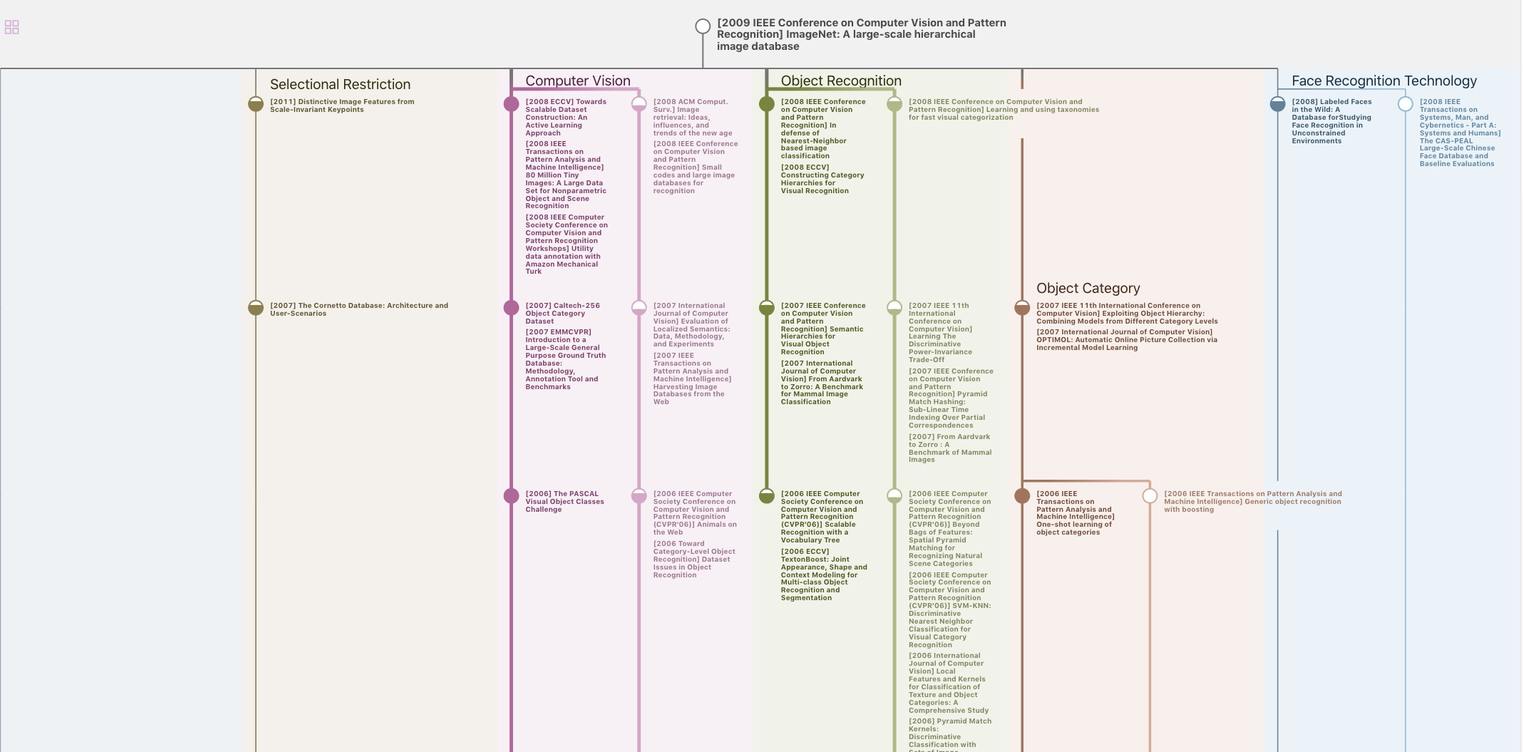
生成溯源树,研究论文发展脉络
Chat Paper
正在生成论文摘要