Modeling and simulation method of trajectory in double-side autonomous grinding considering the dynamic friction coefficient
INTERNATIONAL JOURNAL OF ADVANCED MANUFACTURING TECHNOLOGY(2022)
摘要
Double-plane grinding plays an important role in the processing of high-precision flat parts. A double-side autonomous grinding (DSAG) method was proposed and investigated to improve the uniformity of the abrasive grains of the grinding disc on the surface of the workpiece by releasing the constraints on the workpiece. In DSAG, the main driving force of workpiece movement comes from the friction force generated by the relative movement of the upper and lower grinding pads. Experiment of dynamic friction coefficient measurement between workpiece and grinding plates is carried out to take into account the differences of dynamic friction factor under different speed and force conditions. A mathematical model of the relative motion trajectory between the particles on the upper and lower plate and the workpiece is established based on kinematics and dynamics theories. Then, the effects of the linkage mode of the lower plate, grinding pressure, and speed ratio of the upper and lower plates on the frequency and direction uniformity of the grinding trajectory of the abrasive particles on the workpiece surface are simulated and analyzed. Aiming at the trajectory uniformity, the grinding parameters are optimized through orthogonal experiment and verified on the independently developed experimental platform. The flatness and roughness of the workpiece are detected. The results show that the DSAG performs well in obtaining the better roughness and flatness of the workpiece surface than that of planetary grinding.
更多查看译文
关键词
Double-side autonomous grinding,Sliding friction coefficient measurement,Trajectory model,Motion trajectory
AI 理解论文
溯源树
样例
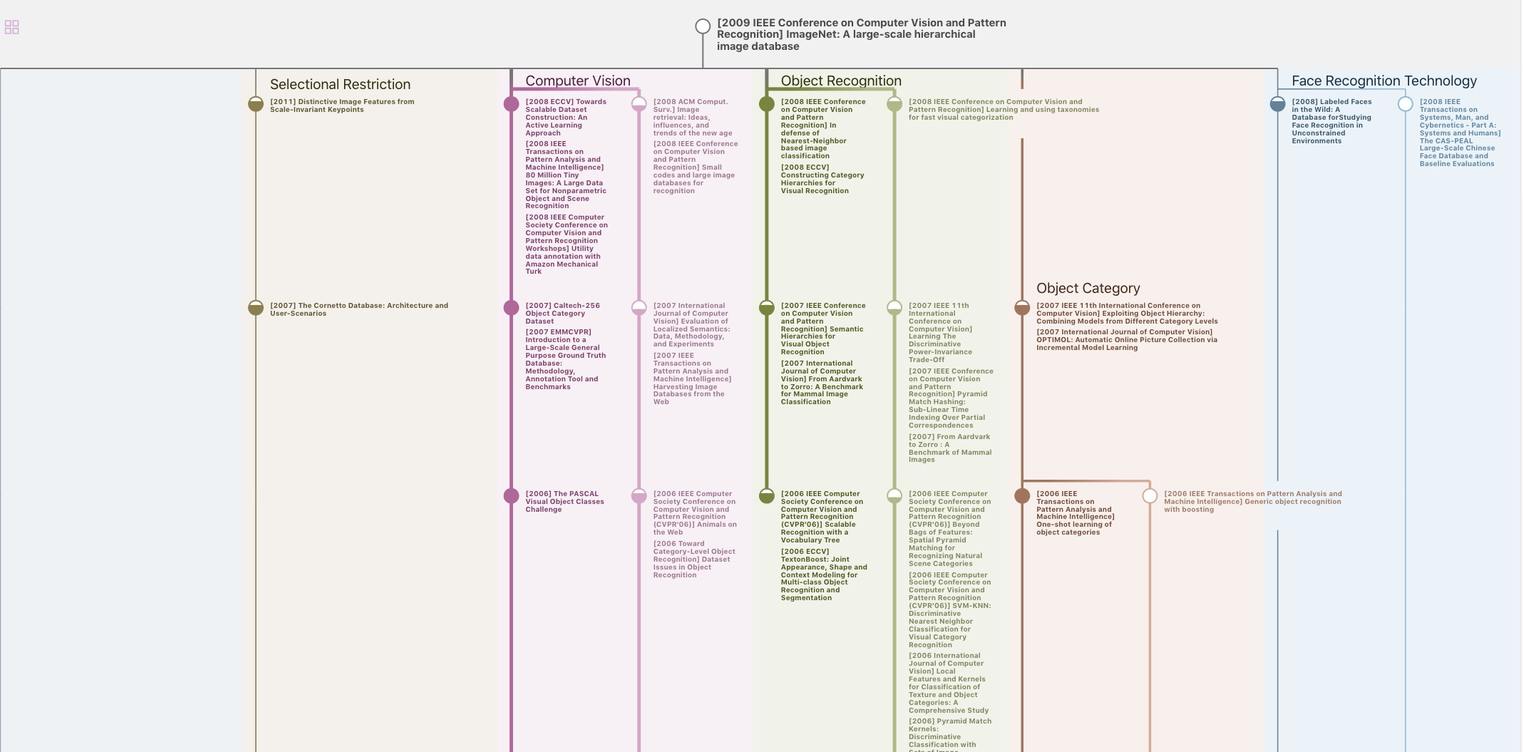
生成溯源树,研究论文发展脉络
Chat Paper
正在生成论文摘要