The Effect of Partial-Load Operation on a Gas Turbine Compressor of an Advanced Combined Cycle Power Plant
Volume 10D: Turbomachinery — Multidisciplinary Design Approaches, Optimization, and Uncertainty Quantification; Turbomachinery General Interest; Unsteady Flows in Turbomachinery(2022)
摘要
Abstract Gas turbine combined cycle (GTCC) power plants daily undergo start-up, shutdown and partial-load operations to maintain load invariance of electric power supply. The off-design conditions in this process may give rise to unexpected and unsteady flow behavior in the gas turbine, resulting in fatigue failure. JERA Co. Inc. currently operates gas turbines at many advanced combined cycle (ACC) power plants using a start-up and a partial-load operations. During the start-up procedure, some machine vibrations were reported at the ACC power plant when acoustic emission (AE) measurements were applied to the gas turbine compressor. A small crack in the first-stage stator blade was found at another unit during the overhaul. The partial-load operation may be in a similar condition to that in the startup procedure. This study elucidated the cause of machine vibration measured in an actual gas turbine compressor of an ACC power plant using full-annulus flow computation to indicate the possibility of blade failure. The full-annulus unsteady flows through the inlet guide vanes (IGV) and 1.5 rotor and stator stages in the compressor were simulated. The frequency of the simulated vibration was compared with that of the natural vibration of the blades, which was obtained by conducting eigenvalue analysis. The results for the partial-load condition captured an abnormal vibration resulting from a rotating stall. The rotating stall frequency closely matched the second-mode frequency of the first-stage stator blade’s natural vibration. This result suggests that the partial-load condition could be related to the cause of the blade failure due to the blade vibration.
更多查看译文
AI 理解论文
溯源树
样例
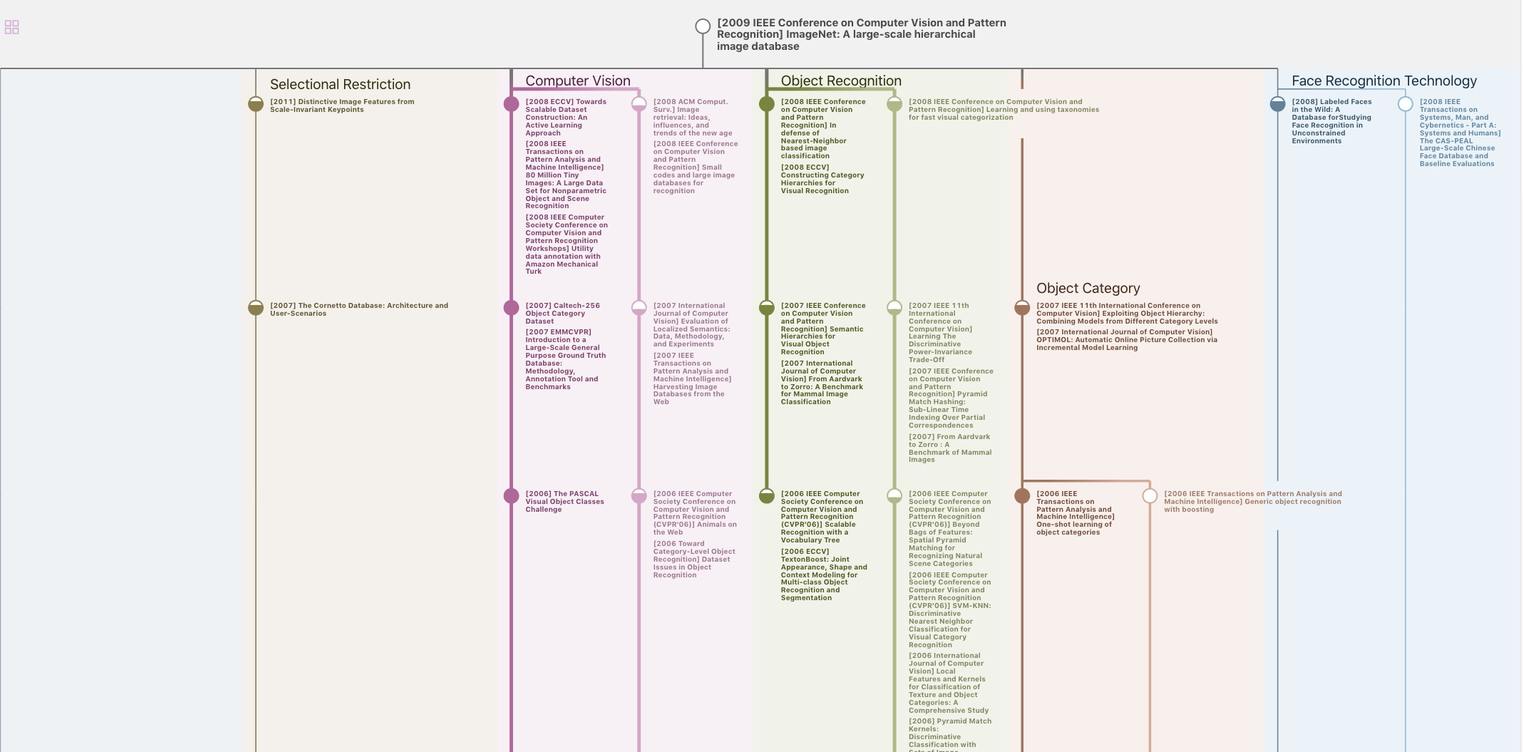
生成溯源树,研究论文发展脉络
Chat Paper
正在生成论文摘要