Hole-Making in D2-Grade Steel Tool by Electric-Discharge Machining through Non-Conventional Electrodes
PROCESSES(2022)
摘要
A low material removal rate and a high tool wear rate are two major concerns among the research and development community of electric-discharge machining. From the literature, it is evident that several researchers have attempted to improve the material removal rate and minimize the tool wear rate by different means, such as parametric optimizations, powder mixing in the dielectric, induced vibrations in the electrode and/or workpiece, etc. Herein, an attempt is made to make use of a non-conventional electrode with a relief angle along with the taper angle of the machined feature and perform electric-discharge machining on D2-steel using copper as an electrode material. Preliminary level mathematical models were developed and validated for sparking the area of each non-conventional electrode's design type. Three-stage experimentation was performed to identify the most appropriate electrode design. An approximately 70% improvement in the material removal rate, an around 45-50% reduction in the tool wear rate, and a nearly 10% reduction in the taper angle were realized with the newly designed non-conventional electrode. Similarly, to validate the machining performance, the most appropriate identified electrode design was used for each workpiece of different thicknesses. The confirmatory experimental results revealed that the identified electrode design is not only limited to a specific workpiece thickness but is well-suited for varying workpiece thicknesses as well.
更多查看译文
关键词
electric-discharge machining, electrode designs, D2 steel, sparking area, mathematical models, material removal rate, tool wear rate, through-hole, taper angle, relief angle
AI 理解论文
溯源树
样例
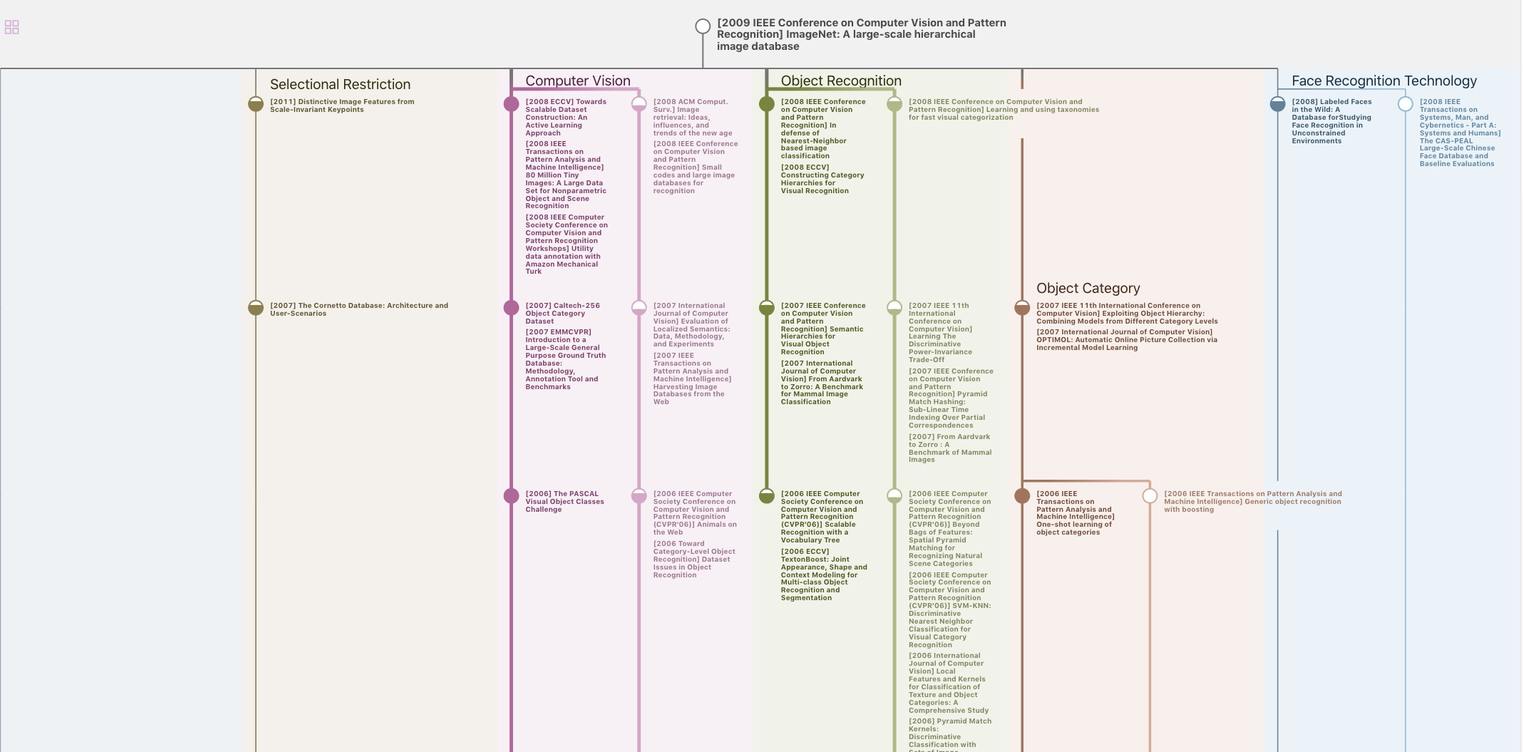
生成溯源树,研究论文发展脉络
Chat Paper
正在生成论文摘要