Optimisation of the swinging jaw design for a single toggle jaw crusher using finite element analysis
INTERNATIONAL JOURNAL OF INTERACTIVE DESIGN AND MANUFACTURING - IJIDEM(2022)
摘要
This study reports on the design optimisation of the swinging jaw crusher plate. Jaw crusher machines are used in the mining and construction industry for crushing rocks and mineral ores to the appropriate sizes for direct application or further processing. During the crushing process, large and non-evenly distributed impact forces occur, resulting from uneven feed patterns and nonhomogeneous material composition (varying hardness). Hence, the jaw plate experiences inhomogeneous stress distributions causing warping and fracture failure of the crusher plates. The plate warping reduces the crusher performance, resulting in low crusher efficiency, high cost of replacing the crushing plates, and higher energy consumption. In this study, the design parameters: plate profile, thickness, and the height of the jaw plate were optimised using ANSYS software. These design parameters were varied to analyse deformation and stress distribution during crushing. Design of experiment techniques was used to determine the optimal design parameters. Optimisation results showed that the optimal design parameters were: 40.06 mm thickness, 4.94 mm plate profile, and 996.21 mm height. An analysis using the optimal parameters produced the optimal outputs as 1.41 MPa for the maximum equivalent stress and 2.7 × 10 –8 m for the average total deformation. This study shows that the jaw crusher plate geometry influences the flow stress and deformation behaviour during the crushing process. The findings from this study provide the basis for future designs of swing jaw crushers for industrial applications.
更多查看译文
关键词
Crushing force, Deformation, Equivalent stress, Jaw crusher, Optimisation
AI 理解论文
溯源树
样例
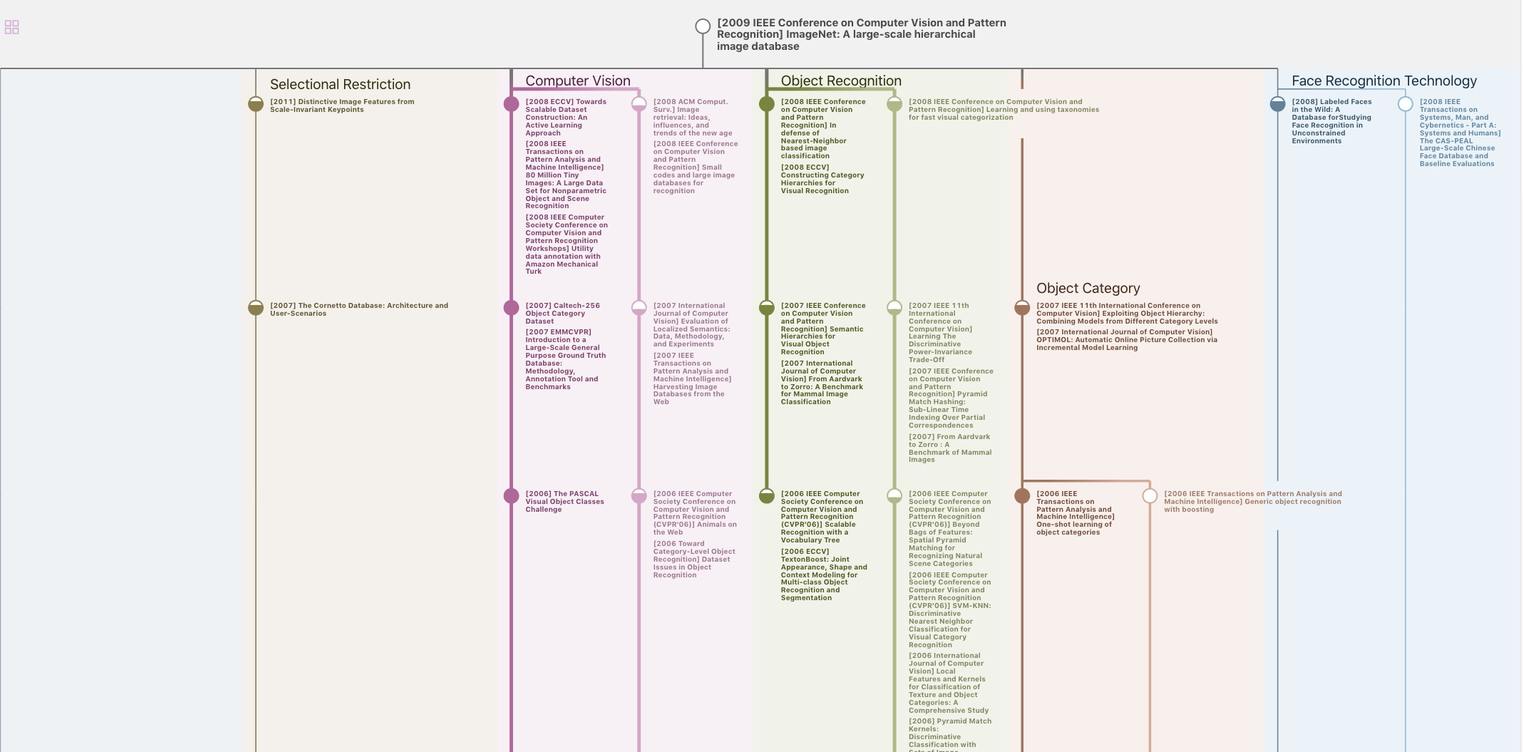
生成溯源树,研究论文发展脉络
Chat Paper
正在生成论文摘要