Error estimation and cross-coupled control based on a novel tool pose representation method of a five-axis hybrid machine tool
International Journal of Machine Tools and Manufacture(2022)
摘要
Five-axis hybrid machine tools combine the advantages of series and parallel mechanisms; however, the time-varying, non-linear, and strong coupled characteristics of parallel mechanisms cause contour control difficulties, particularly during high-speed motion. To solve this problem, this study explores the error-transfer laws between the five feed axes, tool centre position (TCP), and tool orientation (TO). It proposes a new tool -pose representation method, called 'TP', for five-axis machine tools; and designs a cross-coupled controller taking TP as the control target. Moreover, a kinematic model of the hybrid machine tool is established, and the error transfer law is solved through the first-order differentiation of the kinematic model. Subsequently, two points are taken on the tool axis, the redundancy of coordinates is removed by coordinate transformation, and TP is achieved. Finally, a cross-coupled controller is designed. The input of the controller are the tracking errors obtained according to the five feed-axes commands and encoder feedbacks. In the controller, according to the laws of error transfer, the TP contour error is estimated in real time, and the control variables are assigned to the feed axes. Finally, taking a five-axis hybrid machine tool as an example, the error transfer characteristic analysis as well as error estimation and cross-coupled control (CCC) experiments are performed. The experimental results obtained through the numerical control (NC) program feedback of the computer numerical control (CNC) system verify the correctness of the theory and validity of the method.
更多查看译文
关键词
Hybrid machine tool,Five-axis machine tool,Cross-coupled control,Contour error
AI 理解论文
溯源树
样例
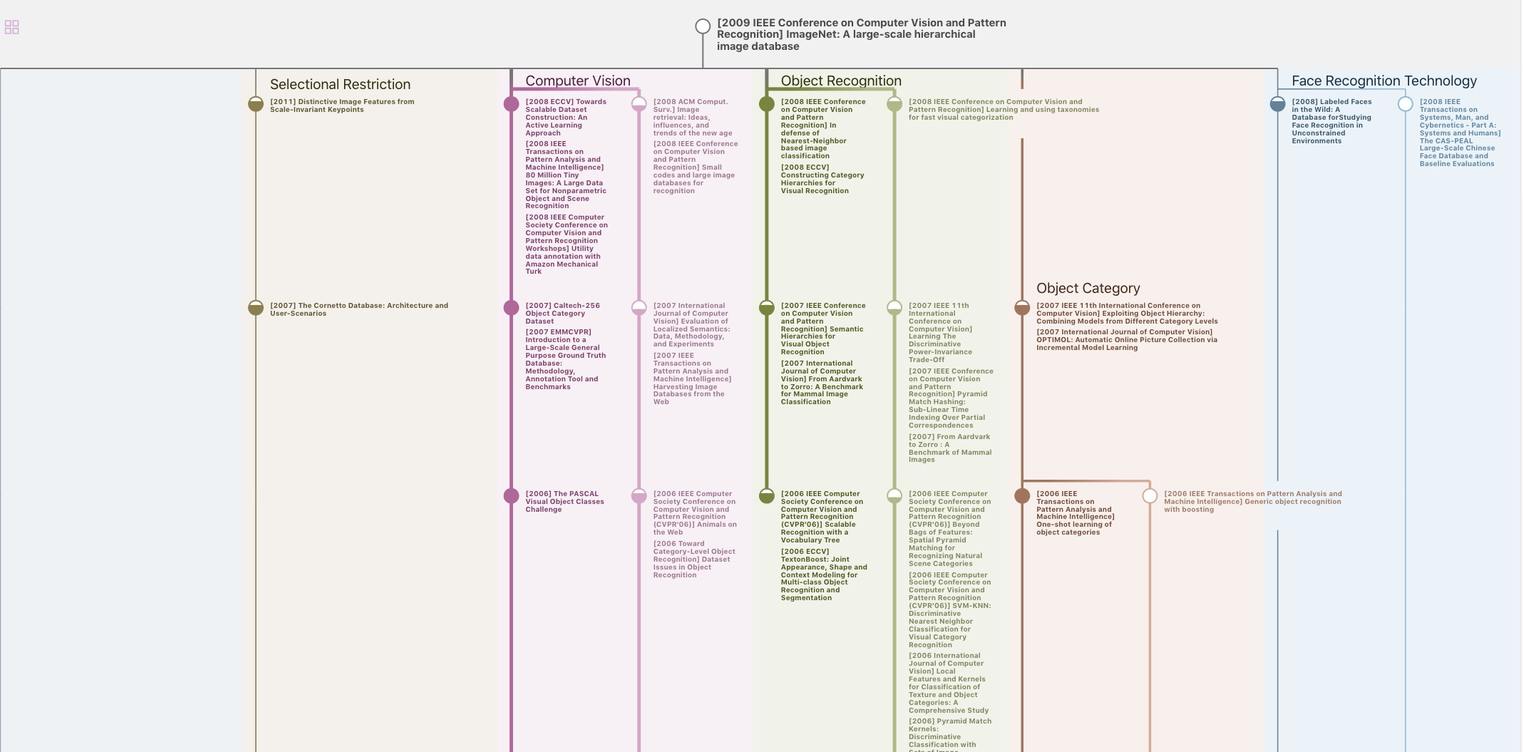
生成溯源树,研究论文发展脉络
Chat Paper
正在生成论文摘要