Mechanical failure analysis during direct shear of double-joint rock mass
Bulletin of Engineering Geology and the Environment(2022)
摘要
This study investigated the shear performance and failure mechanism of a complicated jointed rock mass by simulating the compression and shear of a layered jointed rock mass through the global insertion of a zero-thickness cohesive element. The feasibility of the model was confirmed through the comparison between the results of the indoor shear test and numerical simulation. Then, we studied the macro- and mesoscopic mechanical properties of jointed rock mass from the aspects of deformation and failure characteristics and shear strength variation. The major findings of this study are as follows. First, the stress concentration and shear failure of double-joint layered rock mass occur initially in the interlayer. The double-joint rock mass in the shear process suffers from not only the slip failure of the joint plane but also the brittle failure of the interlayer, which complicates the stress state of double-joint rock mass. Second, the peak shear strength of double-joint rock mass is positively correlated with the normal load, while the change in the shear performance of the multijoint rock mass shows little relation with the roughness of the joint plane. Therefore, more attention should be given to the interlayer material strength during actual construction. During construction around a layered jointed rock mass, the confining pressure should be observed first, especially in areas with high ground stress, and the layered jointed rock mass should be reinforced in time. This study provides theoretical guidance and a scientific basis for tunnel excavation and support optimization in complex layered jointed rock masses.
更多查看译文
关键词
Jointed rock mass, Shear failure mechanism, Macro- and mesoscopic analysis, Zero-thickness element, Shearing process
AI 理解论文
溯源树
样例
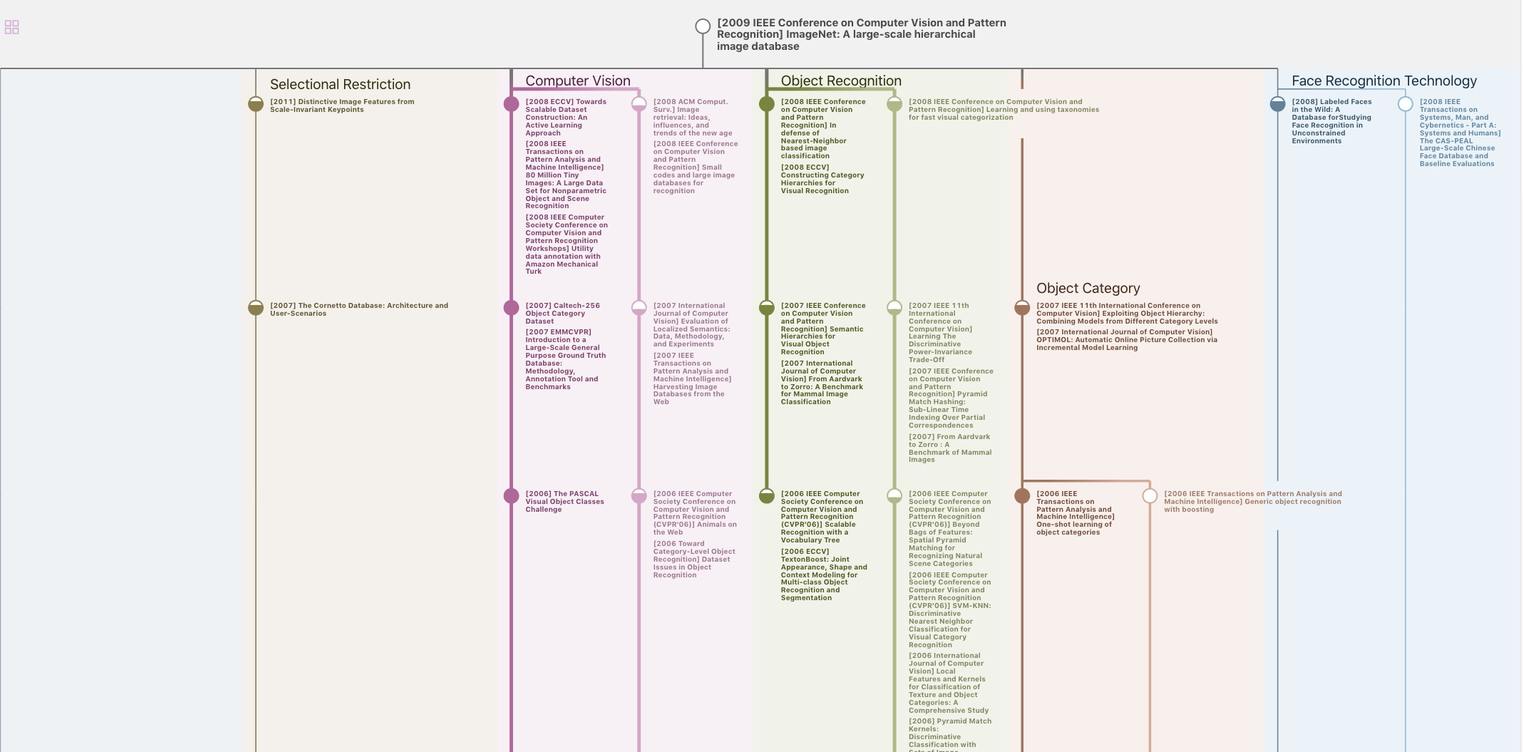
生成溯源树,研究论文发展脉络
Chat Paper
正在生成论文摘要